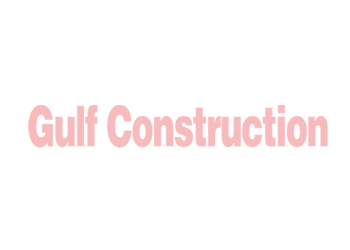

Michael Weinig, one the world's woodworking machinery giants, has expanded its range of machinery following a recent acquisition.
With the acquisition of Interholz Raimann earlier this year, Weinig now offers systems and machinery for ripping solid timber to size, in addition to its line of moulders, saws, finger jointers and edge-gluing machines.
"Raimann's multi-rip machinery complements the range of machinery within the group and strengthens Weinig's reputation for supplying everything from one source, for solid wood manufacturers," says spokesman for the Germany-based group.
Raimann is located in Freiburg, Germany. In its last financial year, its turnover exceeded DM30 million ($19.17 million), with an export share of 70 per cent.
The latest acquisition to the group - which includes Waco Jonsereds of Sweden and GreCon Dimter - has made Weinig the world's biggest solid wood machinery group, according to the spokesman.
"Each company in the group operates independently from each other, concentrating in its own specialised fields and continuous and heavy group investment in technology has ensured uniquely innovative products," he says.
One of Weinig's new products is its Unimat 3000 Brillant moulder. "This one-of-a-kind moulder is completely computer controlled and incorporates a new PowerLock automatic tool clamping system," says the spokesman. "Its concept and technology is truly unique in the woodworking industry."
Launched just over a year ago, the Brillant has been installed in over 50 production facilities worldwide. "It is attracting enormous interest and orders from many more companies, some smaller than initially expected, because of the advantages it provides and its pay-back on investment," he says. "Customers have reported faster set-up times of five minutes compared with 35 minutes for conventional moulders and two-and-a-half times more productivity than normal moulders. They also say that the machine doubles the normal feed speeds with an excellent quality finish, ensuring faster delivery times on short runs."
A new economically-priced Unimat 2000 is also available with the benefits of the PowerLock tooling, running at 12,000 rpm. Feed speeds of up to 30 m/min are easily achievable with perfect surface quality, without jointing the knives, according to Weinig.
Weining also offers a range of mechanised handling options for its moulders. "The faster a moulder works, the more difficult it becomes to feed and off-load manually and with feed speeds of 60 m or more, mechanical handling becomes essential," says the spokesman. "Weinig offers a range of economically-priced standard or specially-tailored equipment for this purpose, comprising destackers, infeed and outfeed tables, stackers, bundling and wrapping equipment. Depending on a customer's requirements, additional equipment such as Unscrambler units can also be supplied."
"Mechanical handling equipment is proven to increase production efficiency by around 30 per cent, ensuring faster pay-back on investment," he adds.
For smaller companies, Weinig says it has developed new machinery that is high quality, versatile and very affordable. These include the Weinig Quattromat 23 P and Profimat 26 super moulders, and the OptiCut S 75 automatic cross-cut saw and the ProfiPress edge-gluing machine, both from GreCon Dimter.
These new machines are designed to help the small and medium-sized manufacturer compete with bigger companies on flexibility and quality.
"The OptiCut S 75 is available in four versions, from a basic cross-cut saw for cutting fixed lengths of timber or packs of timber, to the top-of-the-range model which offers optimised defect removal with simultaneous length cutting for maximum yield," the spokesman says. "The basic machine can be extended as the customer grows by retrofitting the extra features, which makes the saw an attractive proposition and more affordable for smaller companies, because they only need to buy the features they actually need.
"The ProfiPress is an economically-priced edge-gluing press which should be of wide interest for solid wood panel producers. It is also available as a simple, basic machine for customers that only need edge-gluing capability - at a price that is within reach of smaller companies. Additional features can also be retrofitted as requirements dictate, to convert the ProfiPress into an automatic press line.
Waco is the high-speed, heavy-duty moulder specialist in the Weinig Group. Its planer/moulders have feed speeds of over 100 m/min and up to 350 m/min, and are mainly used in sawmills throughout the world. Waco also supplies specialised tooling and tool room equipment that is required for its moulders. The company also manufactures single and twin-band resaws and mechanical handling equipment for these machines.
"The latest high-speed moulder, Hydromat 30XL, was jointly designed by Weinig and Waco," says the spokesman. "It operates at 150 m/min. and bridges the gap between Weinig's Hydromat 23 moulders that can operate at speeds up to 80 m/min and the famous Waco Maxi moulders that take feed speeds up to 350 m/min. Waco high-speed moulders are in greater demand today, because of their very high production capabilities."
GreCon Dimter is steeped in technology and machinery for optimising and finger jointing timber - to increase yield, reduce waste and improve quality. GreCon Dimter products are growing in popularity because of environmental as well as practical reasons for the changing patterns in timber demand, according to the spokesman.
"Many forward-looking companies who have installed finger jointers are reaping benefits above all expectations," he says. "In addition to higher profitability, they are able to use off-cuts, as short as 150 mm, normally wasted, to produce lengths of useable, upgraded timber. Timber lengths produced are structurally stronger, straighter and longer and of higher quality - being defect free."
He continues: "Finger jointing technology has improved vastly over recent years. Tooling is much more precise for cutting finger joint profiles and adhesives have been perfected to advanced levels. The result is that finger-jointed components are used increasingly in furniture and in structural applications such as glulam beams for main building structures, laminated timber for window scantlings, panels, and more recently, decking."