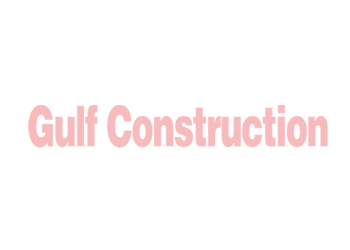
Microsilica has given the opportunity for builders to use concrete where it would previously have been thought impossible - or certainly not economic.
The Middle East is by far, the worst possible environment for placing concrete - especially high-performance concrete where long-term durability is paramount. Unfortunately, it is this very environment that requires high-performance concrete in order to achieve the long lifetime for the structures. A difficult 'Catch 22' situation.
However, concrete technology persevered and the use of microsilica concrete has become synonymous with high durability and long lifetime.
Projects such as Alba's potline 4 (Bahrain) - which demanded high electrical resistance and physical durability; Al Khobar power and desalination plant (Saudi Arabia); and precast operations (Dubai) started to run through the 1980s and into the 90s. In 1993, the Gulf's first skyscraper, the Baynunah Tower in Abu Dhabi was built using 80 Mpa, zero water permeability microsilica concrete.
More projects followed: The Burj Al-Arab, Dubai Airport extension, the Second Manama-Muharraq Crossing in Bahrain, LNG (liquefied natural gas) projects in Qatar, more power stations in Saudi Arabia and the huge Shoaiba oil pier in Kuwait.
By 2000, high-performance microsilica concrete had become a necessary part of construction in the Gulf.
As with all concrete, microsilica concrete needs the usual precautions to ensure best results.
Over the years a number of questions have been put forward concerning the use of microsilica in the hot environment of the Gulf: Problems with cracking, worries about heat evolution, mixing and handling, curing and similar.
Many of these are easily addressed by remembering that to derive maximum performance, all types of concrete needs to be cured properly - and microsilica concrete is no different.
The need for curing becomes more acute especially when using such high performance concrete. All normal forms of curing can be used in isolation or in combination to maximise the quality of cured concrete. Ponding, mist spraying, wet hessian, plastic sheeting, and membrane compounds are all effective methods of curing and can be used depending on the situation. Sometimes combinations of methods are found to be more effective. Just as the mix is designed for the purpose, the curing also must be designed for the situation. The Baynunah Tower was cast with 80 MPa concrete using a 10 per cent microsilica dosage. The curing regimen was specified at 14 days wet curing. This was done and the concrete had no cracking at all.
A perfect mix cannot be obtained by the mere dumping of microsilica into a concrete mix. Mix design is very important. The concrete should be designed for purpose - and certainly not overdesigned. The average dosage of microsilica across the Gulf is about eight per cent. Higher percentages need better design of the mix to prevent bulking, high water demand and handling difficulties.
Concern over heat evolution is a very misleading point. Just because the microsilica can increase the strength - and improve the rate of gain of strength - does not mean that it is going to generate huge amounts of heat. The heat of hydration of microsilica is similar to cement (kilo for kilo). Therefore, if you modify the mix to achieve a certain strength by reducing the cement content, say, from 450 to 350 kg/cu m and then on adding 35 kg of microsilica, the resultant mix will have an overall loss of heat by some 65 kg cement's worth.
Similarly, microsilica can be used to gain early age strength in very high replacement concretes - where 50 to 70 per cent of the cement is exchanged for PFA (pulverised fuel ash) or GGBS (ground granulated blastfurnace slag). The pozzolanic action of the microsilica will give an early strength, structural integrity, and reduce the permeability of the fragile concrete, while not increasing the heat by more than a few kilos worth of cement.
Self-compacting concrete
If anyone thought that microsilica concrete was sticky and difficult to move, then they haven't ventured into the world of self-compacting concrete (SCC). This is not a new concrete, but merely a method of mix design and control that enables much easier placement of concrete. Microsilica is the perfect addition for creating SCC.
Using particle packing methodology mixes can be designed with superb flow characteristics and no segregation. This reduces the use of 'fillers' such as limestone dust and the use of even more chemical admixtures in the concrete. The microsilica also gives much better hardened properties to the concrete. This is also true for SCCs made with large replacement levels of PFA or GGBS that are modified with microsilica additions.
Here and now
Microsilica concrete is currently being used across the Gulf in a number of highly visible and prestigious projects. Jordan, Egypt and Lebanon are now using microsilica concrete - just as Saudi Arabia, the UAE, Oman, Kuwait, Bahrain and Qatar.
The new airport extension in Dubai will use many millions of cubic metres of concrete and a large percentage of that will contain microsilica. The Burj Dubai will require very high strength concrete - almost certainly using microsilica - and as for the underwater hotel that's planned, well that will need some really high performance concrete.
The World Trade Centre in Abu Dhabi was built using microsilica concrete.
In Beirut, the Metropolitan City Centre is under construction using microsilica concrete, as is the Marina Tower. The Beirut Tower is due to start construction soon and that will also use microsilica concrete.
The use of highly durable, high-performance microsilica concrete in and around the Gulf has increased, year on year, as the improved qualities of the concrete are seen. Many millions of cubic metres of microsilica concrete have been placed in the harsh, unforgiving environment of the Middle East over the last 25 years. A large number of papers have been written concerning the technical benefits of microsilica in concrete for the Middle East. If that isn't testimony enough, the region is by far the biggest consumer of microsilica concrete, in the world.
More and more projects are specifying the use of concrete with microsilica in order to obtain the maximum potential durability, in all sorts of work: From housing projects to bridges, airports to towers, industrial units to adventure parks. Where durability is needed in concrete, there is only one word that comes up: Microsilica.
More information on SCC can be obtained at www.concrete.elkem.com. Information on microsilica can be obtained at the websites: www.concrete.elkem.com (Elkem Materials 'concrete' pages), www.silicafume.org (The Silica Fume Association)and www.concrete.org (The ACI web-site).