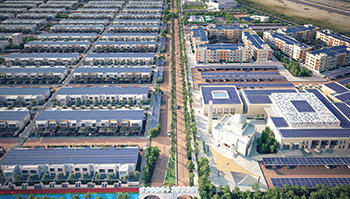
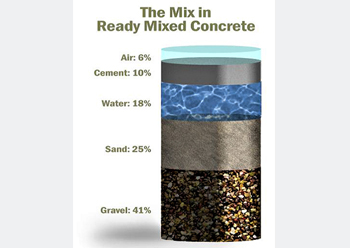
Discussions on sustainable construction have gained momentum as globally roughly 10 billion tonnes of engineered materials are consumed annually for use in industrialised societies (Ashby, 2009).
Construction materials comprise cement, aggregates, concrete bricks, metals, and other associated materials that are extensively used to build infrastructure, commercial and residential projects. These products are utilised in new construction as well as in remodelling, adaptations, maintenance, and repair activities.
Considering the limited global natural resources (40 per cent which is consumed for construction) and 1.3 billion tonnes of construction and demolition waste annually, it is imperative that the construction industry and all stakeholders begin employing sustainable measures in the use of building materials.
Concrete is often at the forefront of the sustainable construction discussion as it is the world’s most widely used material. Globally, 4.4 billion tonnes of concrete was utilised in 2018; and given the population rise and urbanisation trends in conjunction with infrastructure development needs, the demand for concrete is projected to increase to 5.5 billion tonnes in 2050.
And while concrete has a low embodied energy in comparison to other commonly used construction materials (Figure 1), the sheer volume of its use has a significant impact on natural resources and the global environmental footprint.
Concrete’s environmental footprint should be determined with a full lifecycle assessment (LCA) that transparently calculates all direct and indirect environmental impacts and not just carbon dioxide (CO2) or embodied energy.
An LCA systematically assesses multiple environmental impacts of a product, activity or a process over the lifecycle of that product, activity or process. The multiple assessment categories under LCA include impacts on natural resource depletion, climate change, ecosystem degradation and human health. Carbon footprint analysis (aka greenhouse gas – GHG – emissions assessment) is a subset of LCA analysis and focuses on only one environmental impact, climate change by GHG emissions.
Embodied energy is the energy consumed (often measured as CO2 produced) by all the processes associated with the production of a product, from the mining and processing of natural resources to manufacturing, transport and product delivery. Embodied energy does not include the operation and disposal of the building material, which would be considered in a LCA approach.
An LCA provides a holistic approach to quantifying and accounting for environmental impacts from the extraction and manufacturing of raw materials, the manufacturing process of the product itself, the use of the product in service, and its end-of-life fate.
With respect to concrete, an LCA can be quite challenging as concrete is proportioned with multiple raw materials from various extraction points (for example, cementitious binders, coarse and fine aggregates, water, admixtures, etc); produced, transported, placed and cured by various means and conditions; in-use and maintained for decades or centuries depending upon its durability and resilience in service; and then at its end-of-service life recycled into another product or disposed into landfill.
While a concrete’s LCA appears complicated, it is more practically digested in reviewing it within smaller increments and focusing on lessening the product’s environment footprint by reviewing and addressing inputs from materials, the manufacturing processes, in-service maintenance cycles and the end-of-service life.
Sustainability of concrete
Proportioning a concrete mixture to meet the performance criteria on a project such as strength (early age and ultimate), flowability, set time, durability, aesthetics and so on depends on careful mix design, experience and testing. In addition, low environmental impact also depends on careful mixture proportioning.
With the advent of sustainable construction, specifiers are including additional prescriptive requirements to specifications in an attempt to lower the environmental impact of concrete. However, prescriptive requirements, such as maximum cement content, can be limiting and not fully embrace all the strategies that allow the manufacture of sustainable concrete mixtures.
Below is a review of some potential strategies to lower the impact of cementitious materials on the environment:
• Alternative cement constituents and binders: Concrete’s most scrutinised ingredient is Portland cement, the production of which is energy-intensive as it utilises almost seven per cent of industrial energy, globally; and releases about five per cent of CO2 emissions from energy usage and the decarbonisation of limestone reaction during manufacture.
Industry research has focused heavily on reducing cement’s CO2 emissions through improved energy efficiency in production (reduced thermal energy), the use of alternative fuels (reduced carbon intensity), the manufacture of blended hydraulic cements (reduced clinker-to-cement ratios), and employing emerging and innovative technologies such as renewable power generation and carbon capture, storage and utilisation (IEEE, 2018).
European countries, which have been leaders in addressing sustainability and climate change, have a long tradition in producing blended hydraulic cements.
Blended cements with lower clinker-to-cement ratios require less clinker and therefore generate less CO2 emissions when manufactured, as the CO2 footprint of some clinker substitutes is low or even zero.
Over the last three decades, the use of fly ash, slag cement, silica fume (industrial byproducts) and limestone have become common blends. In North America, ASTM and CSA standards for Portland limestone cement (PLC) allow five to 15 per cent limestone replacement; other international standards allow higher replacement values.
There are advantages in the use of blended cements (as opposed to concretes with supplementary cementing materials – SCMs – added separately to the concrete mixer) with regards to chemical and physical properties that can be better controlled. However, some concrete producers feel that more flexibility in use of different replacement levels of SCMs is available than with fixed-proportion, blended cements.
Other alternative cement constituents such as natural pozzolanic materials, gypsum and calcined clay can be used as a partial replacement for clinker to produce blended cements. Notably, the reduction of clinker content is highly dependent upon the availability of alternative materials, required cementitious properties of the final product, regional standards, and technical requirements in end-use applications.
In addition to blends, other alternative non-Portland-based binder systems with lower energy and CO2-intensity can be used in lieu of Portland cement. Most studied by the industry include cements and binders from belite clinkers, calcium aluminate and sulphoaluminate clinkers, and alkali-activated binders of slag cement and fly ash (geo-polymers). Many of these non-Portland cement binders have been used in project-specific applications.
• Proportioning concrete materials: Most concrete mixtures contain, by volume, seven to 15 per cent cementitious materials, 60 to 75 per cent aggregates, 15 to 20 per cent water and small amounts of chemical admixtures to control plastic (fresh) and hardened properties (Figure 2).
The quantity of cementitious materials depends on the performance requirements for the concrete with the average quantity of Portland cement approximately 420 lb per cu yd. As a result, approximately 170 to 500 lb of CO2 is embodied in every cu yd of concrete produced or approximately five to 13 per cent of the weight of concrete produced, depending on the mixture proportions (Marceau et al, 2007). This average quantity has consistently decreased with better optimisation of concrete mixtures and increased use of SCMs that can improve the strength and durability characteristics of concrete and lengthen its service life.
A lifecycle inventory performed by Prusinski et al (2007) found that when slag cement replaces 50 per cent of Portland cement in 7,500 psi concrete, the energy required to produce one cu yd of concrete is reduced by 37 per cent; carbon dioxide emissions are reduced by 46 per cent; and virgin material used is reduced by 15 per cent.
Similarly, the EPA (2008) calculated the environmental impact of fly ash, silica fume, and slag cement in concrete and expressed the result in energy efficiency savings and corresponding levels of reduced CO2 emissions.
Table 1 summarises the savings and reductions for each of the three common SCMs using 2017 North American volumes from industry sources. A row in the table includes reasonable rates of SCM substitution by type and estimated energy savings and CO2 emission reduction. These rates can vary significantly depending on the application, desired properties, and durability requirements and often a ternary mixture (using two SCMs along with Portland cement in the same mixture) may be the preferred alternative to achieve the desired properties. Different SCMs also use different replacement rates. For instance, very high replacement percentages of cement with Class F fly ash or slag cement may be appropriate for specific applications.
The regional availability of current SCM materials and shifts in industrial processes, for example, shuttering of coal-fired electrical utility plants that produce fly ash, make it imperative for research and implemented use of natural and alternative pozzolans such as metakaolin, expanded shale, expanded slate, expanded clay, pumice, rice husk ash, volcanic ashes, diatomaceous earth, and ground glass. Many of these materials may require processing prior to use in concrete and such processing would add to, and need to be accounted for when assessing, the environmental impact of such materials.
Conclusion
While the cementitious (binder) portion of concrete mixtures may be altered through the use of blended cements, alternative cement constituents, alternative binders, SCMs, and other natural pozzolans, the environmental impact of concrete mixtures may further be decreased with the use of recycled/reused aggregates, mineral fillers, chemical admixtures, and non-potable water alternatives.
ACI 130R-19: “Report on the Role of Materials in Sustainable Concrete Construction”, elaborates further on how materials in concrete can influence environmental impacts; while “The Sustainable Concrete Guide” and “The Sustainable Concrete Guide-Applications” gives a more in-depth understanding of how concrete contributes to sustainability goals.
References:
• Ashby, MF, Materials and the Environment – Eco-Informed Material Choice, Second Edition, (2009), Elsevier Inc, Oxford, UK.
• Marceau, M, Nisbet, M, and VanGeem, M,(2007) Life Cycle Inventory of Portland Cement Concrete, Portland Cement Association, Skokie, Illinois, US.
• QECD/International Energy Agency, (2018), Technology Roadmap: Low-Carbon Transition in the Cement Industry, France.
• Prusinski JR, Marceau ML, VanGeem MG, (2004), Lifecycle inventory of slag cement concrete.in: CANMET/ACI, editor VM Malhotra. Eighth CANMET/ACI International Conference on Fly Ash, Silica Fume, Slag and Natural Pozzolans in Concrete –Supplemental Papers. Farmington Hills, Michigan, US.