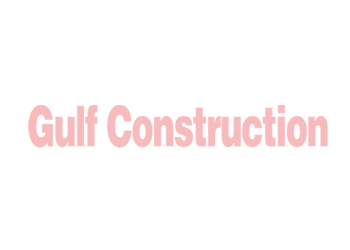

Aject, a leading Saudi-based company operating internationally to provide a complete contracting service covering survey, design, and the construction of Sewer Renovation approached UK-based TT UK for equipment consultation.
The task was to provide a cost-effective trenchless solution for the replacement of 2.6 km of 150 mm cast iron sewer pipelines to be upgraded and upsized to 355mm OD (outer diameter) polyethylene (PE) pipe in Jeddah, over a 12-month period. The depths range from five to 8.5 m with the water table averaging only two m below ground level.
The location, in 'old Jeddah', was first supplied with its sewage system more than 20 years ago.
Trevor Cox, manager of Aject's rehabilitation division, has a wealth of experience in Trenchless Technology and No-Dig Techniques, but had to look carefully and study the many problems facing him.
The project called for replacement lines ranging from 40 m up to 120 m in length and operating from conventional excavations where possible, but also from within manholes.
Cox's previous experience of pipe bursting led him to believe that a hydraulic form of static bursting - where the head opens up to expand and then close again - would not be possible due to the high probability of ingress of sand and water into the equipment mechanism.
Dynamic pneumatic impact pipe bursting was also considered but caution was required since no knowledge was available or records kept of the proximity of existing adjacent underground services, and more importantly, the fragile condition of them.
This left the relatively straightforward method of physically bursting the existing under-capacity sewer line, expanding up the ground to the required diameter and pulling in the new 355mm PE short pipes.
The TT Group's range of powerful (patented) QuickLock Rod hydraulic burst systems fitted this project profile perfectly and after only two technical meetings between Aject and TT UK, it was decided Aject would purchase the powerful Grundoburst 1,000g (100T) unit.
During early preparations, several problems were, as predicted, encountered. They were associated with the over-pumping, isolation work etc, which when carried out correctly is crucial to the overall success of this type of project.
Other complications included access of the narrow Jeddah streets as it was possible in places to touch dwellings on either side whilst standing in the middle of the street.
However, the major hazard was controlling the ingress of the groundwater in both the drive and reception manholes.
Aject's team overcame this by fabricating a seal fitted on the face of the close shuttered sheet piles in the drive shaft and also in the reception trench manhole.
This seal, which had a thick rubber centre, allowed sufficient entry of the Grundoburst's bursting head and the following two-stage expanders without risk of flooding or jeopardising the safety of the personnel working in these nine m-deep excavations.
Due to the enormous one step up size of this sewer line, the tooling set-up was a special three-bladed (star) cutting blade, a 270 mm intermediate expander, followed by a 420 mm final expander where the 355 mm PE (short) 0.6 m pipes were subsequently added as the burst progressed with the aid of TT's special pipe-tensioner device.
The sealing system worked perfectly, as did the bursting and docking, with the safe and dry arrival of the expanders into the Grundoburst's integral extension docking frame.
The total burst run took four hours, including the lowering, positioning, and attaching of each individual pipe length.
The actual set-up of the Grundoburst equipment took half a day, as did the demobilisation on this particularly difficult sewage line.
Aject Rehab is now currently in final negotiation for an additional 2.5 km of the same type of work in another area of 'Old Jeddah' and based on the success of the Grundoburst Equipment and this first drive, Aject has every confidence in the continuing success of this type of equipment and set-up.