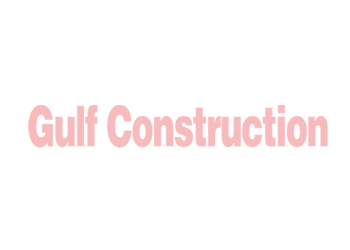

Aluminium Products Company Limited (Alupco), one of Saudi Arabia's top 100 companies, is pressing ahead with ambitions to become one of the world's leading extrusion and surface-finishing facilities.
An extensive restructuring programme was launched by the company in the late 1990s which has underpinned its objective of becoming more customer-oriented, forward-focused and quality-conscious.
In a bid to meet the needs of the market, the company has launched a number of expansion programmes to expand capacity and enhance production facilities at both its Jeddah and Dammam plants and is now looking at setting up extrusion plants in the UAE as well as in Europe.
According to general manager Khalid Mohammad AlFuhaid, Alupco is looking at investing around $80 million by 2010 in installing new equipment, modernising existing lines and constructing new facilities.
Once the UAE facility is on stream, Alupco will focus on setting up a facility in France to meet increasing demand in Europe.
Meanwhile, at its Jeddah plant, a new powder coating line was commissioned at the end of last month (April), increasing the plant's production capacity for coated profiles by 30 per cent. The company's seventh extrusion press of 2,750 tonnes capacity is expected to be fully operational by the end of May. A new storage facility of 3,500 sq m was also recently completed.
At its Dammam plant, a 2,500-tonne press was recently refurbished and modified, increasing its production capacity of extruded profiles by 3,000 tonnes per year. Work is currently under way on a new casthouse building, the central maintenance building and a central storage area, which are all scheduled for completion in June. The casting equipment and installations at its existing casthouse are being refurbished and modernised before they are transferred to the new building. The casting production capacity is expected to increase by 50 per cent.
The company also produces technically-advanced extrusion dies at its state-of-the-art die-making plant (DMP) in Jeddah.
"The DMP is a world-class centre not only for our own extrusion requirements but to eventually meet demand for aluminium extrusion dies on an international basis," says AlFuhaid.
"Besides providing technical advantages locally, the DMP has also curtailed our lead time, reducing costs, improving the quality of the profiles, and allowing Alupco to be more agile and flexible in meeting customers' requirements. Previously, it would take six to eight weeks to source dies from Europe. Now the DMP can turn around dies within two to three weeks. Essentially it means that our customers' requirements can be met with efficiency and urgency," adds AlFuhaid.
The 6,000 sq m DMP facility currently has a capacity to produce upto 2,500 dies, meeting about 50 per cent of Alupco's demand. Production of dies will be increased progressively to a target of 4,000 dies per year in line with demand from other aluminium extruders worldwide.
The expansions are certain to boost sales to new highs, according to Alupco. Total sales grew to $125 million in 2002 from $110 million in the previous year and are expected to exceed $145 million this year.
Most of the company's extrusions are consumed by the Saudi market, but export markets in recent years have grown beyond the traditional GCC and Arab region to the wider international field, including Europe and the Americas. The exports range from extrusions for architectural purposes in construction - the main item - to those for signages, furniture, decoration and industrial applications.
Local sales, which reached 70 per cent of total sales in 2002, are targeted to touch 30,000 tonnes this year and 40,000 tonnes in 2005.
Sales in the GCC region, Middle East and Europe were 30 per cent of total sales and are expected to reach 20,000 tonnes in 2005.
The company has witnessed a more than 60 per cent growth in sales volume over the last five years and is forecasting a minimum growth of 10 per cent per year over the next five years, according to AlFuhaid.
Parallel to the company's expansion programme, Alupco's R & D Department is introducing new products and services suitable for all applications including windows, doors, shop-fronts, curtain-walling and thermal break systems to enable it to expand its market share in local and export markets, says AlFuhaid.
Alupco, the first 100 per cent Saudi aluminium extrusion company when it was established in 1975, currently has a total extrusion capacity exceeding 60,000 tonnes per year.
Since its inception, the company has commissioned seven immense extrusion presses, four anodising lines and four powder coating lines (two of them vertical lines, the first of their kind in the Middle East) in its massive 140,000 sq m combined production facilities.
Following the restructuring, the new management has been the driving force behind a "no compromise" approach to the planning and execution of quality-assured production. Alupco is recognised as the first aluminium extrusion company in the Middle East to bag the prestigious ISO 9001 certification.
The company continues to build on its reputation, producing items of the highest quality and making timely deliveries to meet the needs of contractors and end-users.
AlFuhaid, who became general manager of Alupco in 1998, has inspired a growing customer-focused approach and several strategic investments which have included the 3500/3800 Cadex press (the largest extrusion press in the Middle East), and the vertical coating lines, demonstrating his engineering skills and vision for their unique design.
Alupco facilities, including the DMP, have been closely involved with several major architectural projects including Riyadh's Kingdom Centre, for which it was the sole supplier of 1,200 tonnes of extrusions using 72 different dies produced for the exacting specifications of the aluminium profiles required by the client. Alupco also provided more than 8,000 separately curved cladding sheets for the Faisaliah Center in Riyadh.
Other major projects associated with Alupco include the prestigious Burj Al Arab in Dubai, Dubai Internet City and the National Bank of Abu Dhabi, all in the UAE; the Telecommunications Tower in Kuwait; and the Citibank and National Bank of Bahrain tower, both in Bahrain.
AlFuhaid acknowledges that competition is getting stronger, but believes it is imperative that day-to-day users know "who we are and what we stand for". The awareness campaign he has initiated embraces every link in the distribution channels. The aim is to acquaint them with the reliability Alupco offers from applying international standards in products as well as services.
Having impressed local and foreign markets with the quality and range of its products, Alupco is confident it can embrace additional buyers from a wider spectrum of markets and is expanding capacity to meet the anticipated demand.