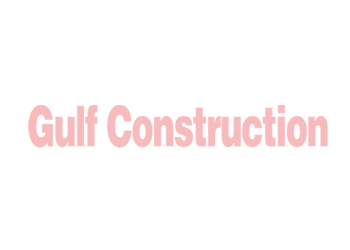
Waterproofing of basements is a risky business. The cost of making the underground structure watertight represents a small percentage of the initial project cost. However, failure of this project element - which is generally underestimated - could cost many thousands of dollars in damages through a subsequent leak.
The risks borne by the designer in regards to responsibilities when specifying a waterproofing solution is relatively high. The designer takes responsibility not only for the specification of a waterproofing product, but also the compatibility of that product in conjunction with other elements of the basement design, and the impact of inadequate workmanship and site conditions on the integrity of the solution.
In short, it is not enough to pick a product. The designer must also consider whether that product will work alongside the other products needed to achieve watertightness, and even go as far as to consider the buildability of the specified solution given the likely quality of site labour and typical site conditions.
Who is this enlightened designer?
In waterproofing design for basements, this is often a point of contention. The architect is typically the lead designer but often assumes that the structural engineer will look after detailing up to DPC (dampproofing course) level. The engineer, meanwhile, considers the architect as being the primary specifier for waterproofing, both above and below ground, and will make a cursory mention of 'waterproofing membrane' or 'waterbar' on the drawings in the hope that the details behind this will be filled in by the architect.
In reality, the engineer is often held to have the design responsibility for waterproofing below ground. However, on many schemes, the uncertainty over specific design responsibilities results in the waterproofing specification being left too open and little attention being given to proper detailing.
Given the ambiguity as to the specific roles and responsibilities of the architect and consulting engineer, together with the inadequate time allocated to thinking about making the below-ground structure watertight, certain pitfalls are common in the design of typical projects. These pitfalls can be avoided through the correct choice of supplier and of products.
Let's focus on how to reduce the designer's risk in choosing both suppliers and products for their specification. The following are points to consider in general when specifying for a waterproofing solution, and how to overcome the risks at this point in the process:
Solution: In all waterstop design, continuity of the network is critical. So, ensure that you specify a solution supplier who has a standard detail for connecting these two disparate technologies together, and who supplies both technologies. If its technical service desk or representative cannot provide a detail as a matter of course, there is a risk that the company has not ironed out the problems in connecting the technologies.
Solution: Ask suppliers to show the products in the office or on site. Touch and manipulate the products to see how robust they feel. Demand project references and ask to speak to contractors who have worked with the products.
Solution: Quality-waterproofing manufacturers offer a free-of-charge full design and specification service to create design details on a bespoke basis for your project including writing tailored specification clauses.
Solution: Ensure single point of responsibility. Interview manufacturers with a full product suite and design capability, and stick with them. Call for a warranty covering the project rather than the products; this can only be achieved if one company supplies the entire solution.
Now that we have established the importance of choosing a single supplier with a full suite of compatible and continuous products, backed up by design and specification support, standard details, experience and project references, we can move on to the specific products which make a project successful.
Waterproofing products can be broken down into a number of categories. Within each category there are a number of key considerations, which can reduce the risk of failure of the waterproofing system when the project is still at design stage. The two primary categories are waterproof membranes and waterstops.
Waterproof membranes
These are physical barriers to the passage of moisture into the structure. In recent years, these have taken the form of 'cast-in-situ' membranes formed from polyethylene sheeting with an integral bonding mechanism or bentonite clay bound in geotextile. These 'grab' the concrete as it is cast and are designed to form an intimate watertight skin cast to the surface of the structure.
Examples of the questions to ask manufacturers in order to reduce risk when choosing these systems include:
1. Is the product tolerant of hard and soft water, impurities and surface contamination? Ensure that the local groundwater does not affect the performance of those systems, which work by means of swellable agents in the membrane. Ensure that the presence of mud, shutter oils, diesel and other surface contaminants cannot affect the nature of the bond between the membrane and the concrete.
2. Do laps encroach into concrete cover? Ensure that the thickness of laps between and at the ends of adjacent rolls does not create such a thickness of membrane that the designed cover is compromised. It is possible with some systems that are nearly 10 mm thick that at the junction of an end lap and an edge lap, a nearly 40mm of encroachment into cover is created.
3. Is it gas-resistant? If the project also requires protection from common gases such as carbon dioxide then this implies the need for a polyethylene rather than a bentonite type system.
4. Is the product reliant on a mechanical or a chemical bond? Some systems have a physical grab mechanism that adheres the membrane to the concrete, while others rely on a chemical adhesive type bond. Given the dirty, wet and inherently variable nature of the construction environment, mechanical systems will tend to offer better assurance of keying to the concrete.
Waterstops
These are cast into the concrete structure at construction or expansion joints and are formed of either PVC or hydrophilic, water-expansive materials. Hydrophilic materials are now much preferred over PVC due to their ease of application on site which tends to reduce the likelihood of poor positioning in the joint.
Examples of the questions to ask in order to reduce risk when choosing hydrophilic waterstop systems include:
1. Is the product a base polymer hydrophilic or a blend? To form a swellable waterstop, hydrophilic molecules are either blended into a carrier matrix, such as neoprene rubber, or are inherent within the material, which is used to form the waterstop strip. The latter is called a base polymer hydrophilic and is preferable to the blended format because of the propensity for the water-swellable component to leach out of the matrix to which it is loosely bonded. A base polymer hydrophilic does not offer this risk. The performance benefits of this include perfect reproducibility of swell over many wet and dry cycles, and maintenance of its volume increase over time. The performance of blended products is impaired after four to five wet and dry cycles, and early volume increases are rapidly reduced after a few days of wetting.
2. Is the product tolerant of groundwater containing salts? The performance of all hydrophilic products is negatively affected in some way by salts. However, some are worse than others. If the project has salt-bearing groundwater, particularly if building near the coast might mean seawater, checks must be made on the impact of this on the performance of the hydrophilic waterstop. The important factor to look out for is medium-term deterioration of volume swell. The swell curve should show no deterioration of swelling over time in the presence of salt water, even if the overall volume of swell is reduced from that in tap water. Choosing a base polymer hydrophilic reduces the chances of deterioration of swell.
3. Can the swell be delayed to cope with site delays? The swelling action can become a problem if this occurs before the product is built into the concrete structure. If delays occur on site and the product is available to become wet before being cast in, then pre-swell can occur which will cause a gap to be cast into the concrete around the waterstop. This problem can be ameliorated by the use of a delayed swell product which can cope with up to 48 hours wetting before swelling commences. Some products use a water-soluble delay coating applied to the waterstop but this may be affected by surface contaminants. Other products offer a retarded swell polymer which are unaffected by the vagaries of site conditions.
4. Is the product resistant to microbiological attack? Hydrophilic waterstops work by forming a positive sealing pressure between themselves and the surrounding concrete in the presence of moisture. If the product is also a host to aquatic bugs then this surface contact can be compromised. Tests have found that even some of the leading brands of hydrophilic waterstop display a degree of microbe growth. Ask suppliers for proof of the resistance of their products to microbe growth.
5. What are the concrete cover constraints? Some manufacturers specify the need for at least 100 mm cover in front of their product in order to cope with the swelling pressures created. However, not all products yield the same amount of swelling pressure and some manufacturers offer products which can be installed with as little as 75 mm cover. It is generally preferable to use products requiring less cover because these allow for smaller section sizes to walls and slabs.
Conclusion
Waterproofing is a risky business. The designer, typically the engineer, carries a heavy burden of responsibility. Future problems can be minimised by: