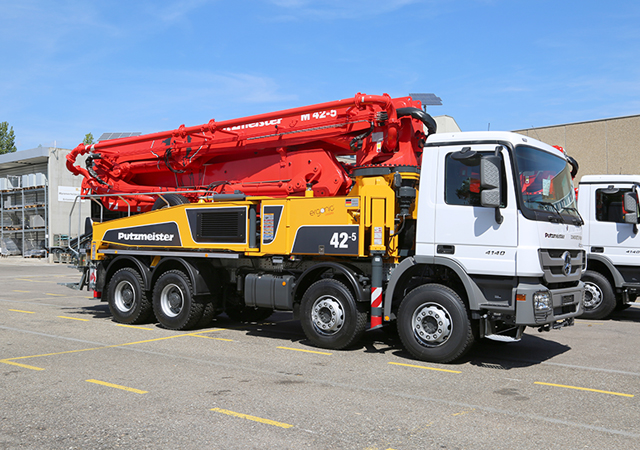
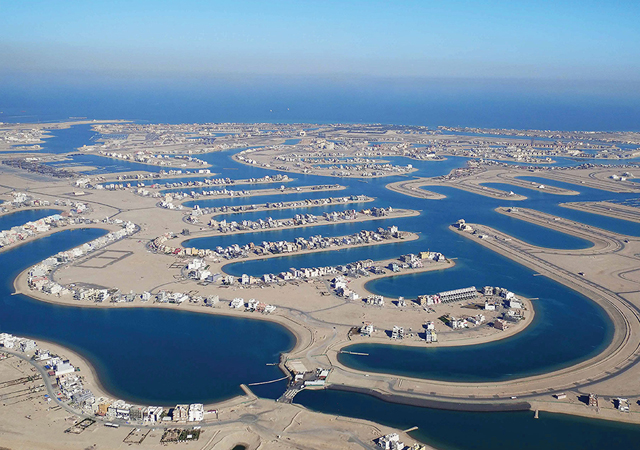
The ambitious Sabah Al Ahmad Sea City project is reshaping Kuwait’s desert landscape with a pioneering approach to urban expansion. This ambitious project involves the creation of approximately 300 km of canals in the Al Khiran region, a unique approach compared to other Gulf region developments that typically rely on coastal backfill.
Unlike traditional artificial land developments in the Gulf region that rely on large-scale land reclamation, Sea City’s canals are carved into the existing desert landscape and then flooded with seawater. This multibillion-dollar endeavour, slated for completion over 46 years in 10 phases, will eventually provide a fully integrated urban environment for up to 250,000 residents, complete with comprehensive infrastructure and luxury amenities.
Constructing large-scale infrastructure on desert sand presents significant challenges. German engineering expertise, specifically from Bauer Maschinen GmbH, is playing a crucial role in preparing the ground for this ambitious vision.
The Sea City project utilises dynamic soil compaction, a technique suited for increasing the density of non-cohesive soils common in arid regions. This method is particularly effective for the subsoil composition found in desert environments, explains Steffen Fuchsa, Head of the duty-cycle crane division at Bauer Maschinen. By expelling pore water, it also reduces the risk of soil liquefaction in the event of an earthquake, he adds.
![]() |
The sequential soil compaction process ensures a stable foundation for future urban infrastructure. |
Bauer Maschinen, a global leader in specialist foundation engineering, has deployed six Bauer MC 96 duty-cycle cranes for large-scale dynamic soil compaction.
The process involves using massive steel plates, weighing 25 tons each, welded together to form “pounders”. These pounders are hoisted by Bauer MC 96 duty-cycle cranes and then dropped from a significant height, creating craters upon impact. The kinetic energy compacts the soil by forcing the grains to rearrange. Bauer’s advanced technology allows for fully automated hoist control, where operators input target parameters like degree of compaction and number of impacts. The system then automatically guides the crane through the compaction process, creating a grid of impact points. A second phase of compaction targets the areas between the initial craters, resulting in a load-bearing construction surface.
Bauer’s duty-cycle cranes execute the process automatically, moving systematically across a predefined grid. This level of automation ensures accuracy while maximising productivity on-site.
![]() |
Six Bauer MC 96 duty-cycle cranes operate under extreme desert conditions at the Sabah Al Ahmad Sea City construction site. |
“Our duty-cycle cranes are extremely stable and robust specialist foundation engineering equipment designed for high dynamic loads,” remarks Fuchsa. The cranes feature robust steel construction, powerful diesel engines, and a coordinated hydraulic system that efficiently transfers power to the hoists, making them ideally suited for dynamic soil compaction, he adds.
Overcoming challenges with smart solutions
Executing soil compaction at this scale presents unique operational challenges. The sheer scale of the area requiring compaction, coupled with tight deadlines, necessitates continuous operation. The harsh desert climate adds another layer of complexity. Extreme temperatures demand constant cooling for the equipment, while the ever-present sand requires meticulous sealing to prevent infiltration. Bauer has addressed these challenges with specialised protective devices for the cranes.
The equipment runs around the clock, requiring robust design features and intelligent maintenance solutions.
One of the key challenges in dynamic compaction is maintaining perfect rope winding on the hoist drum, explains Fuchsa. Improper winding leads to excessive rope wear and increased costs.
To counter this, Bauer has developed proprietary technologies such as an active rope tightening system and a winding assistant – features that significantly reduce wear and lower maintenance costs for operators, says Fuchsa. These innovations set Bauer’s MC series apart from competitors, ensuring superior durability and efficiency in demanding environments, he adds.
Fuchsa emphasises that the optimisations implemented in Bauer’s duty-cycle cranes for dynamic compaction are a direct result of extensive practical experience. This commitment to real-world application ensures that Bauer’s equipment delivers exceptional performance and reliability even in the most demanding conditions.
Germany-headquartered Bauer Maschinen Group specialises in high-performance drilling rigs, duty-cycle cranes, trench cutters, and other advanced foundation solutions. With manufacturing facilities across Europe, the USA, and Asia, Bauer remains at the forefront of geotechnical innovation, delivering cutting-edge solutions for complex infrastructure projects worldwide.