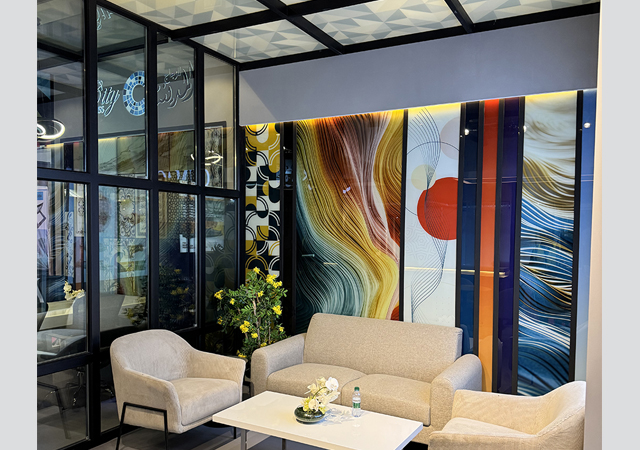
.jpg)
Citing a successful example, the Dubai-based protective coatings company has revealed its role in a key pipeline rehabilitation project at the Hatta Dam, UAE, utilising its cutting-edge polyurea-based lining technology. The project faced the challenge of internal abrasion and impact damage in GRE pipes, leading to reduced efficiency and lifespan.
Delta Coatings’ highly durable coating solution, approved for potable water by WRAS (Water Regulations Approval Scheme), offers long-lasting protection, reducing maintenance costs and extending the lifespan of critical infrastructure, the company says.
Hatta Dam, the first of its kind in the GCC region, is a large-scale tourism and recreational water reservoir feeding into the major hydroelectric power station in Hatta. The 250 MW station generates electricity by making use of the water stored in Hatta Dam – which has a storage capacity of 1,500 MWh – through a series of pipelines and canals. The overall project has a life span of 80 years.
![]() |
The GRE pipeline at the Hatta Dam project before coating. |
While GRE pipelines are valued for their corrosion resistance and durability, they are prone to internal abrasion and impact damage, compromising efficiency and the longevity of the pipes. The project owners, therefore, sought a retrofittable, cost-effective solution to address these challenges and ensure long-term protection.
After extensive testing, Delta Coatings International’s DeltaShield HP 500 PW emerged as the top choice for its superior abrasion and impact resistance.
The high-performance polyurea elastomer was deployed to retrofit the GRE pipelines. The material, applied as a seamless, hot-spray membrane, offers rapid curing and resistance to cracking, peeling, abrasion, and impact. The coating is certified under BS 6920, NSF, and WRAS for potable water use up to 85 deg C, ensuring safety for human consumption applications.
This entire turnkey infrastructure project was delivered on a supply-and-apply basis by Delta Coatings International, offering a single supplier advantage and a one-point multi-year warranty for its application and product performance.
Delta Coatings lists some of the technical advantages of DeltaShield HP 500 PW:
Abrasion resistance: It exhibits excellent resistance to abrasion, making it suitable for protecting pipelines from the erosive effects of suspended solids. Its exceptional abrasion resistance can significantly extend the lifespan of GRE pipelines, reducing the need for frequent repairs or replacements.
Chemical resistance: DeltaShield HP 500 PW or HP 400 is highly resistant to a wide range of chemicals, ensuring the integrity of the pipeline even in harsh environments. It protects pipelines from corrosion caused by harsh water conditions;
Rapid application: It ensures minimal downtime for pipeline repairs or maintenance due to quick curing properties;
Strong adhesion: This product adheres strongly to various substrates, including GRE, providing a durable and long-lasting protective layer;
Cost savings: By providing a durable and long-lasting protective layer, this product helps to reduce maintenance costs over time.
The technology is suitable for various projects, including potable water reservoirs dams, storage tanks, canals and viaducts; rainwater storage tanks; desalination plants; water bottling and cleaning plants; and fish breeding tanks, particularly where WRAS-certified coatings are required.