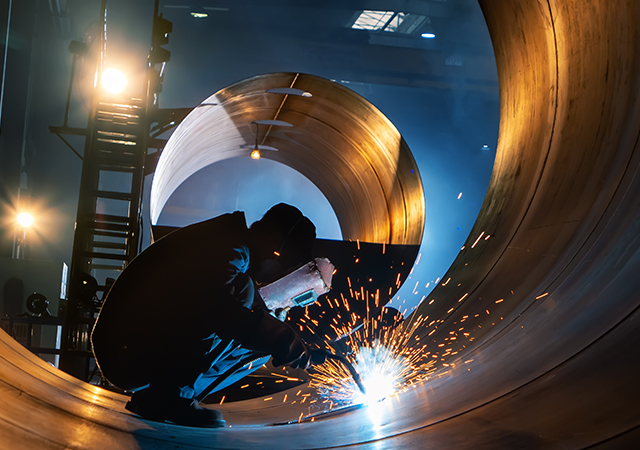
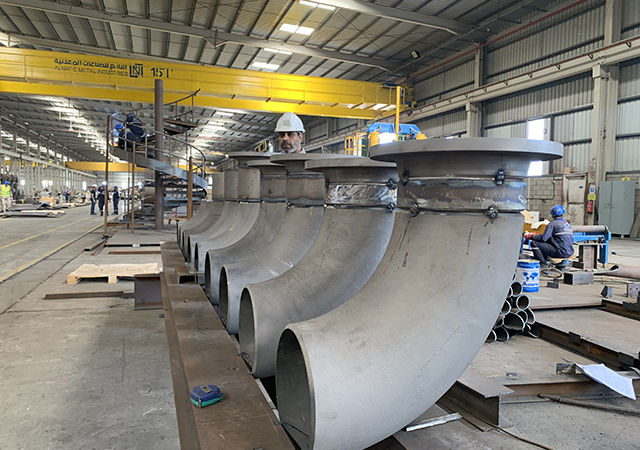
Saudi steel giant Al Nafie Metal Industries (NMI) is aiming for the top spot in the Middle East’s steel fabrication sector, according to its General Manager Majed Suleiman Al Nafie.
“Our vision is to become the leader of the steel fabrication and erection industry in the Middle East and we want to participate actively in realising Saudi Arabia’s Vision 2030,” Al Nafie declares in an exclusive interview with Gulf Construction’s Bina Goveas.
“Our aim is to serve the requirements of the numerous planned and ongoing construction projects in the Kingdom of Saudi Arabia, and the regional and international markets. The steel fabrication industry in the Gulf needs a continuous supply of products with the highest quality, and environmental compliance. Al Nafie Metal Industries is ahead of its competitors in adopting industrial practices and serving customers with the highest quality, cost-competitive products,” he emphasises.
![]() |
Al Nafie ... demand is going to rise to an all-time high. |
NMI, which is working on landmark projects like the Shuaiba III desalination plant, the Riyadh Metro and the Saudi futuristic city Neom, is capitalising on the surge in Saudi Arabia’s construction market, driven by the Vision 2030 programme.
“The demand for steel fabrication has witnessed a dramatic rise in recent years,” Al Nafie remarks, highlighting the crucial role steel structures are playing in realising giga-projects like Neom and others in Riyadh and Jeddah.
“Since Saudi Arabia has won the rights to host the 2034 World Cup, demand for steel structures is going to rise to an all-time high in upcoming years,” he adds.
To solidify this position, NMI is implementing a strategic expansion plan which encompasses increasing capacity and expanding its product portfolio to cater to the high-demand oil and gas and power generation sectors. This includes building capabilities to manufacture large-diameter storage tanks, heat recovery steam generators (HRSG) casings, and ducts for process and power plants.
![]() |
A storage tank fabricated by NMI. |
Located in the Al-Khumrah area of Jeddah, NMI’s current production capacity sits at an impressive 10,000 tonnes per month. The company has recently boosted the capabilities of its plant by acquiring cut-and-bend and straightening rebar machines, build-up assembly and straightening machines, high-speed drilling and CNC beam line machines, Al Nafie states.
NMI is positioning itself as a one-stop shop for steel fabrication needs across various industries. Its portfolio includes steel structures, storage tanks, pressure vessels, process and power piping and pipe spools, stacks, ducts, diverters, HRSG casings, silos and hoppers, catering to sectors like oil and gas, petrochemicals, power generation and desalination.
“We benchmark our processes against the best-in-class companies and practices. We rely on machine automation for mass production. And the latest software for design, nesting, cutting, welding and painting and delivery etc is one of our valuable assets,” he says.
![]() |
A stringent quality control process is in place to ensure the high quality and reliability of NMI’s fabrication. |
NMI strives for performance excellence in operations and customer satisfaction. It has ASME U, PP, S and NBIC R and NB certificates. The company credits its success to a team of highly trained engineers, project managers, and quality control specialists. Al Nafie underscores NMI’s unwavering commitment to quality and operational excellence. The company prioritises obtaining certifications like ISO 9001 and continuously invests in cutting-edge machinery to streamline production processes.
A stringent quality control process is in place to ensure the high quality and reliability of its fabrication, according to Al Nafie. “Our quality control/assurance team ensures that the production process runs smoothly without any major defect and deficiencies. Process control measures at each stage of production (fit up, welding, surface treatment) is implemented and monitored. Defects and variations in process are analysed and Root Cause Analysis (RCA) is performed to minimise such defects in future. Each process of the factory is measured for KPIs at set intervals and continual improvements are made to the same,” he explains.
NMI recognises the importance of environmental stewardship and integrates sustainable practices into its fabrication processes. The company prioritises material efficiency through optimised cutting techniques and implements a comprehensive waste management plan that focuses on minimising waste generation, reusing materials wherever possible, and responsibly recycling scrap metal. NMI adheres to environmental management standards. It also has certifications for its Occupational Health and Safety (OH&S) Management System (ISO 45001-2018) and Environment Management System (EMS ISO 14001:2015), he adds.
![]() |
Mall of Saudi ... a key project for NMI. |
NMI boasts an impressive portfolio that underscores its vast experience and technical capabilities. The company has played a key role in landmark projects like the Shuaiba III desalination plant, a critical component of Saudi Arabia’s water security strategy. NMI also contributed to the Riyadh Metro, a central element of the kingdom’s public transport infrastructure development. Its involvement in Neom projects (piled jetty and storage tanks) and the Formula 1 Jeddah circuit further highlights its ability to handle complex and high-profile undertakings. Other projects include storage tanks for Marafiq and Ma’aden, Saudi Mall and Jawhrat Mall.
The company’s prestigious clientele includes Siemens, Saudi Aramco, SSEM, Doosan, Acwa Power, MAN, Saudi Electricity Company, Sabic, and Neom, a testament to its reputation for quality and reliability.
Looking ahead, Al Nafie emphasises the importance of collaboration. “We welcome business partnerships, fostering long-term relationships built on sustainability, reliability, efficiency, and quality,” he says, extending an invitation to industry leaders to join forces in shaping the future of the region’s industrial landscape.