
In the previous tech talks, MH Hydraulics FZC, a leading hydraulic solutions provider in the Middle East, focused on oil contamination and talked about the importance of clean & dry hydraulic/lubrication oils and various ways to prevent oil contamination.
In this TechTalk#7 we will help you to measure contamination and understand the importance and benefits of knowing your asset’s oil contamination level.
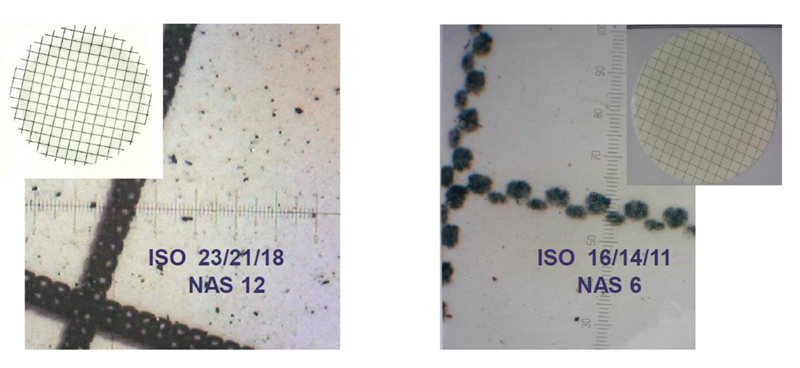
From our previous tech talks we have determined that the major contributor to equipment loss of usefulness is surface degradation, which is approximately 50 per cent mechanical wear, caused by particle contamination and 20 per cent corrosive wear, caused by moisture contamination.
I. CONTAMINATION STANDARDS
Standards were created to measure and express the cleanliness quality so that we are all on the same page and speak the same language in discussing oil cleanliness levels. For these standards, we refer to the size and quantity of particle contamination. For the fluid power industry, these standards are unified world-wide:
• ISO 4406:1999: This is the current method for coding the level of contamination by solid particles, as spelled out by the International Organization for Standardization (ISO). Its method has been developed to test and measure the average size and quantity of particles within a given volume of fluid.
Cleanliness levels are defined by three numbers divided by slashes ( / ). These numbers correspond to, for example, 4, 6 and 14 microns, in that order. Each number refers to an ISO Range Code, which is determined by the number of particles for that size (4, 6 and 14 microns) and larger.
To better understand this, below is the ISO 4406 chart that indicates the actual ranges:
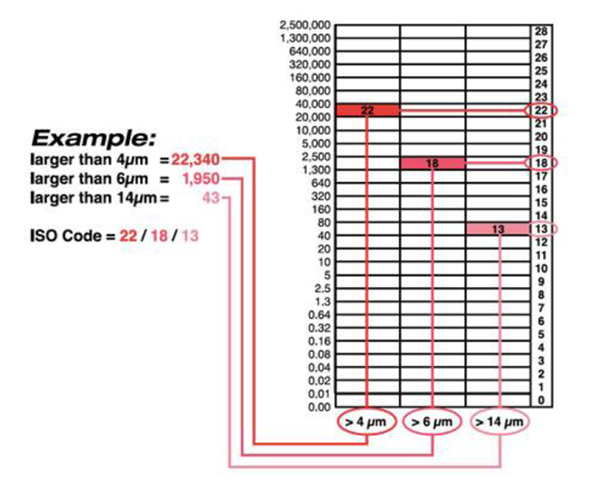
Another standard often used are NAS codes:
• National Aerospace Standard (NAS) 1638: Developed in the 1960s, this standard helps to control the contamination levels of hydraulic fluid within hydraulic components. NAS 1638 became a standard not only for the aerospace industry but also throughout many other industries.
• The newer version of NAS 1638 is AS4059: Is NAS 1638 dead? Well… not quite. NAS 1638 can be used for existing systems where correlation with earlier data is necessary. However, users are encouraged to change to ISO4406 as soon as possible so that everyone is speaking the same language.
II. COMPARISON OF CONTAMINATION STANDARDS
Both NAS 1638 and ISO 4406 focus on the methods for calculating particle counts or solid contamination levels within a fluid. In many areas of the industry, NAS 1638 has largely been outpaced by the ISO 4406 standard in recent years. ISO 4406 gives a greater amount of useful data and is usually the preferred method.
Comparison Chart (The comparisons relate to particle count data only. To conform to any standard, reference should be made to the recommended experimental procedure):
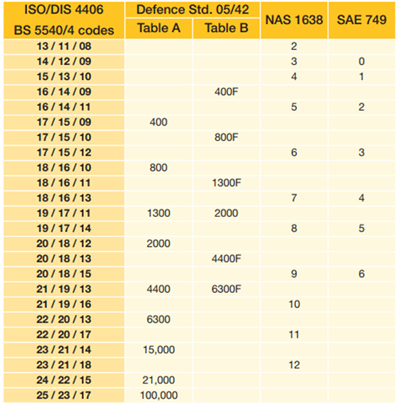
III. WHY IS IT IMPORTANT TO KNOW YOUR ASSET'S OIL CLEANLINESS LEVEL?
The size of the contamination can vary from the size of a grain of salt down to those undetectable by the human eye.
This contamination can either come from external sources (ingestion) or are generated from within (ingression). Even if no immediate failure occurs, contamination can dramatically decrease operating efficiency. Contamination can accelerate component wear, which in turn leads to inefficient operation, seizure of parts, higher fluid temperatures, leakage, and loss of control.
Analysing the oil will indicate how the system is performing, prompting proactive maintenance to ensure performance and reliability. Samples taken initially will provide a benchmark, and further routine samples will ensure the oil is in top condition and provide early warning of abnormalities so preventative action can be taken.
IV. HOW OFTEN SHOULD YOU CHECK?
When to sample and what results to look out for will be entirely dependent on the application and the Target Cleanliness Level (TCL) of a system.
The below table gives an indication of how often you should aim to analyze your oil, depending on the TCL.
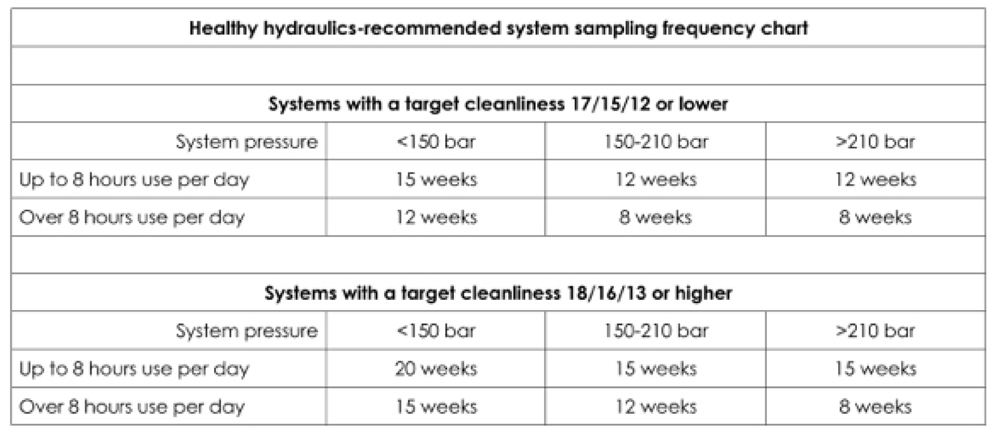
V. WHAT IS THE CORRECT WAY TO TAKE A SAMPLE?
It is best to take a sample from the return line before passing through a return filter. For the powerful hydraulic applications that are running regularly at high pressures, secondary sampling points around the hydraulic components are recommended.
This will allow us to diagnose accurately where the build-up of debris/particle contamination occurs.
VI. CONTAMINATION CONTROL STRATEGY
Now that we know our asset’s lubricant condition, A contamination control strategy must be put in place and to implement this we must;
• Set targets: Every component/asset has a manufacturer’s specified ISO cleanliness and recommended target moisture levels.
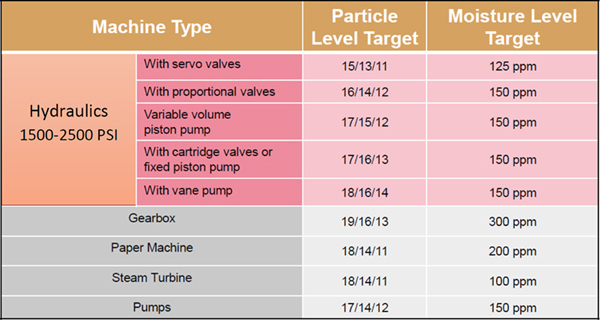
• Take action: Exclude and remove contamination by installing desiccant breathers that will absorb particles and moisture, install adequate additional filtration system.
Types of additional filtration systems:
1. Mobile Offline Filtration Systems: Often used for periodic filtration of less critical assets or where contamination build-up is less expected. Also Ideal for pre-filtering new oils as they arrive at your plant or facility.
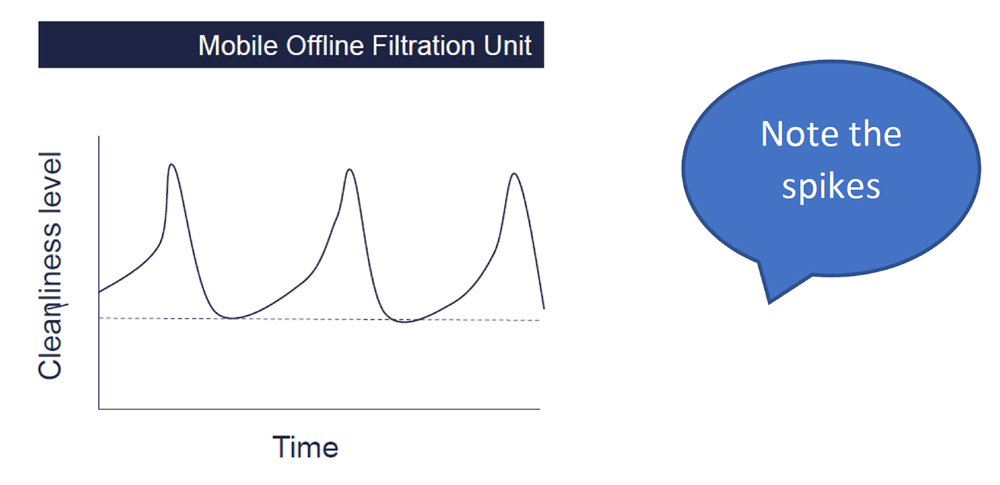
Disadvantages:
• Critical and/or high value systems require constant clean & dry oil, not periodic clean oil.
• As soon as filtration stops, the amount of contamination increases again.
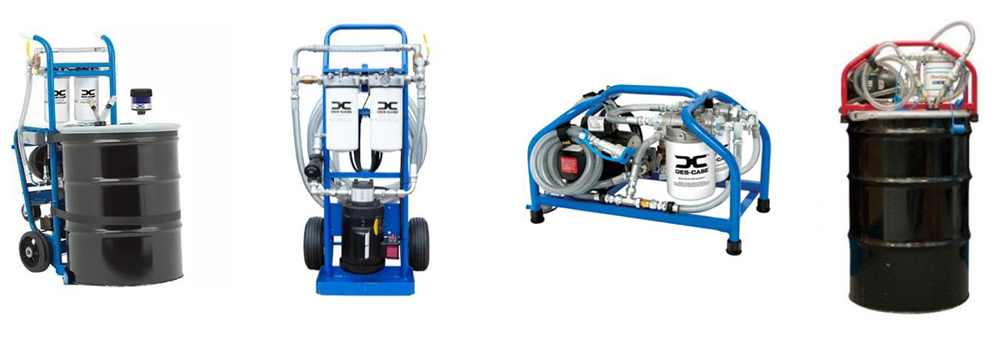
2. Dedicated offline filtration system: Dedicated filtration is especially used in equipment with critical applications. Maintaining the contamination levels as low as possible.
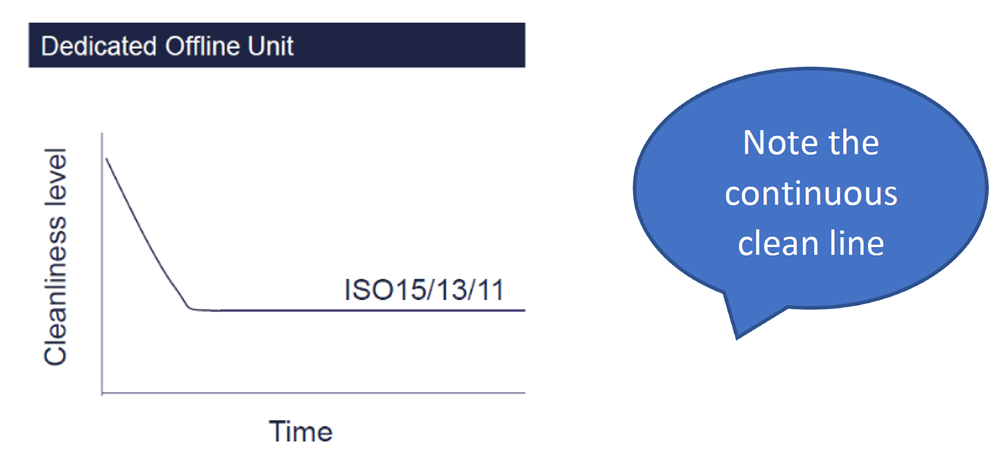
Advantages:
• 24/7 filtration.
• Continuous clean and dry oil.
• Extended lifetime of components, oil/lubricant and inline/full flow filters.
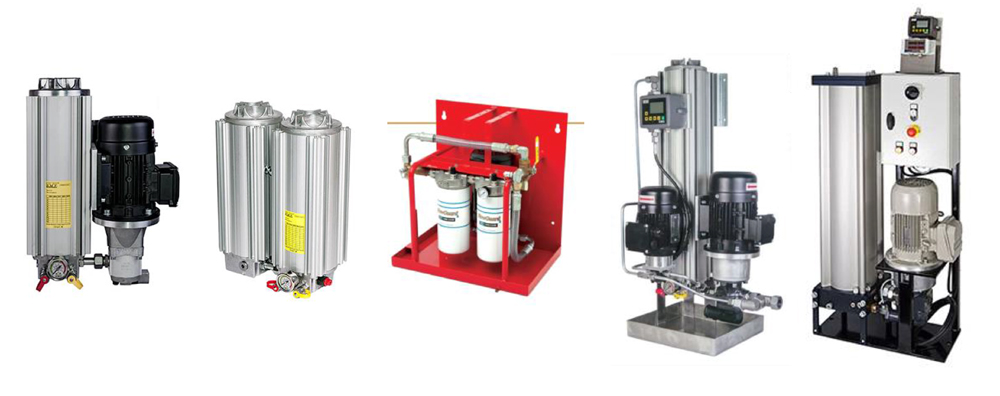
VII. Measure
It is important to measure or take samples on a regular basis to ensure that the equipment is working safely and to be able to evaluate the effectiveness of your actions.
There are many ways to measure the contamination of the oil:
1. Traditional oil analysis and common tests
• Manual bottle sampling: Possibility to get a very detailed report, which can incorporate particle count, membrane picture, water analysis, viscosity, TAN, wear metals & additive package and others.
• Particle count: This test employs a laser particle count instrument that counts the number of particles in a specific size range per a given volume of sample.
• Viscosity test: This is the measure of the oil’s resistance to flow (shear stress) under certain conditions.
• Moisture test: This is the method of choice when accuracy and precision are required in determining the amount of free, dissolved, and emulsified water in an oil sample.
• Elemental analysis: This is a process where a sample is analysed for its elemental and sometimes isotopic composition.
• FTIR analysis: This is used to Identify and characterise unknown materials; identify contamination on or in a material; and identify additives after extraction from a polymer matrix.
• ACID Number (AN): This measures the level of acidity in a lubricant an indicator of oil serviceability. It also is useful in monitoring acid buildup in oils due to depletion of antioxidants. Oil oxidation causes acidic byproducts to form.
• Base Number (BN): Measuring the BN can help ensure that the oil is able to protect the component from corrosion due to acid.
• Ruler test: This measures antioxidant additive levels present in lubricants to monitor the depletion rates of the antioxidant protection package in the oil.
• Membrane Patch Colorimetry (MPC) test: This is used to check the varnish potential of the asset.
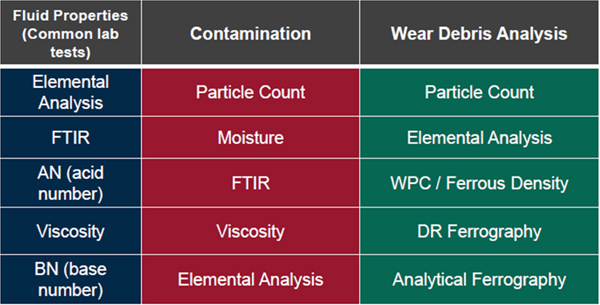
2. Condition monitoring systems
Portable online sampling: This is a perfect solution for a quick and accurate ISO cleanliness analysis (onsite). The results can be checked against required cleanliness levels immediately.
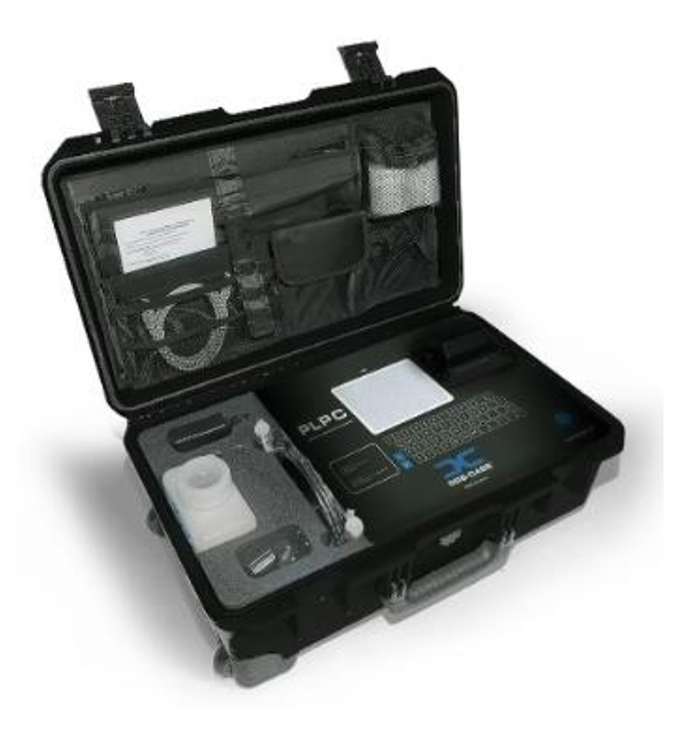
Twin laser and twin optical diode detectors Based Light extinction Automatic Optical Contamination Monitor. Full calibration is based on ISO11171 and thus give official ISO-certified lab results.
Permanent online sampling: This is used to observe the trends of the contamination values to determine sudden change in oil quality. Also capable of setting pre-warning alerts to notify changes in oil quality.
Condition monitoring sensor: This measures the size and quantity of particle contamination, temperature, and relative humidity percentage. The instrument uses a light extinction principle, high intensity LED light source shines through the fluid and lands on a photodiode.
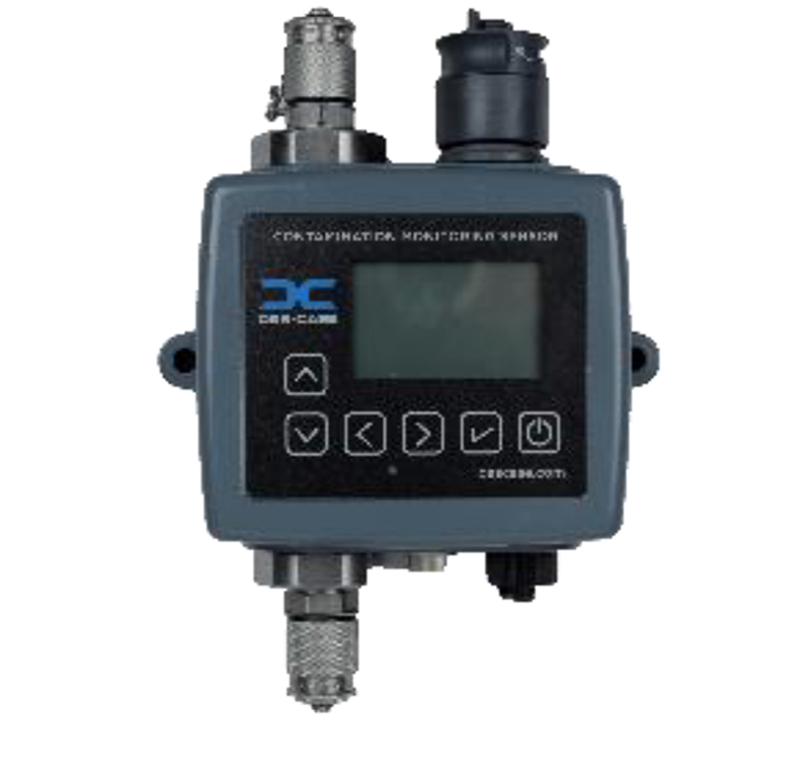
Oil quality sensor: A dielectric sensor measures oil degradation caused by various failure modes such as TAN increase, viscosity break down, oxidisation, TBN degrease, additive depletion, etc.

Moisture content sensor: This is used for long-term measurement of even the highest relative humidity levels up to 100 per cent.
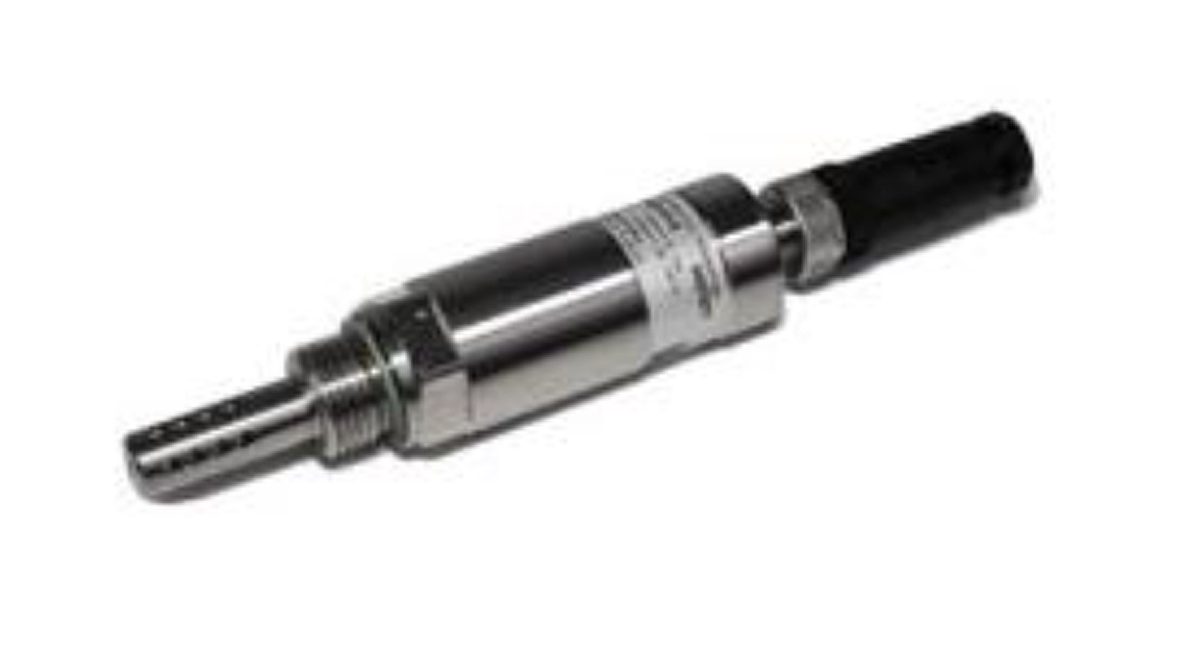
Connected breather: A desiccant breather that can monitor/track exact moment of water ingress.
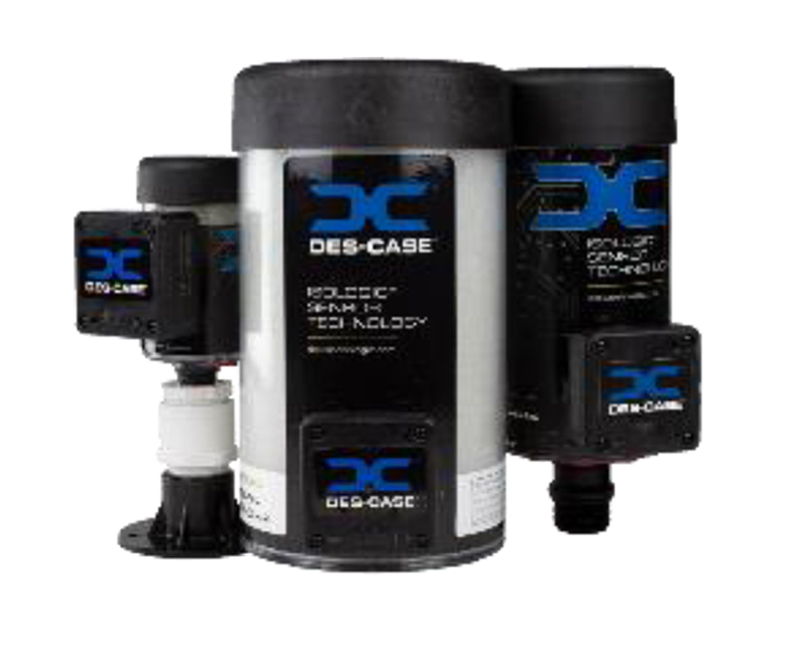
Note: Although these condition monitoring systems are very accurate and important, they do not substitute a detailed lab analysis. The earlier described equipment are excellent tools to see a trend, identify a sudden increase of contamination or a lubricant health change, as well as giving us a better understanding of our assets health with all the data provided.
VIII. CONCLUSION
Assets, machines, equipment, systems require a certain cleanliness level to operate properly and efficiently. With the use of contamination standards, tiny amounts of water and micron-sized particles cannot be seen with our eyes. It’s mostly these particles that are causing failures in assets like hydraulic systems, gearboxes, reducers, and pumps.
The remaining life of the asset and lubricant are seriously jeopardised when systems are operating with contaminated oil or not operating with the required cleanliness level.
Implementing the right strategy in keeping your oil clean and dry will result in:
• Increase of overall equipment reliability.
• Reduction of downtime and maintenance costs (thus saves money).
• Decrease our clients’ footprint on the environment.
• Less breakdowns.
• Less oil changes.
• Longer remaining life of components and oil.
• Ultimately, result in a higher return on investment.
* This article is supplied by