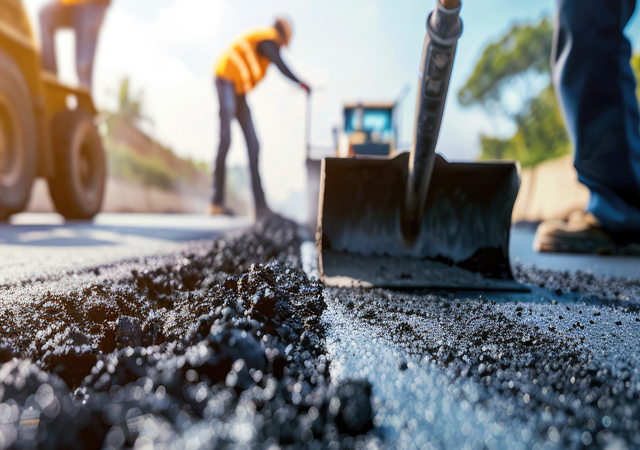
The pavement and infrastructure industry plays a vital role in global connectivity but faces significant challenges including environmental concerns, rapidly changing regulatory specifications and rising maintenance and ownership costs. As the industry continues to look for innovative and sustainable approaches to address these pressing challenges, Honeywell Titan® presents a groundbreaking low-carbon paving solution that is designed to deliver durable roads at lower ownership costs without compromising performance.
INTRODUCTION
Modification of paving-grade bitumen has increased due to heavier vehicle traffic on highways and refinery limitations related to high-quality bitumen. Polymers have shown to improve bitumen properties related to highway pavement performance. The most commonly used polymers are plastomers (such as PE, PP, EVA, EBA, etc) and elastomers (such as SBS, SIS, SEBS, etc).
Demand for highly modified bitumens - such as PG 76, PG 82 and PG 88, or PG 76V, PG 76E, etc - has increased significantly. These grades typically require high polymer content, resulting in high viscosity of the modified bitumen (especially with elastomers) and rendering the modified bitumen unworkable/difficult to pump and spray. Compaction of asphalt mixtures with elastomeric polymers (like SBS) is challenging as the higher viscosity modified bitumens resist compaction.
To address the increase in viscosity, suppliers of elastomer-modified bitumens often recommend increasing temperature up to 180-190°C, which results in higher energy consumption and rapid oxidation.
NEED FOR HYBRID MODIFICATION
Unlike elastomers, many plastomers have a melting point within range of the processing temperatures for polymer-modified bitumens (PmBs) and will melt and result in marginal viscosity changes. The low viscosity of modified bitumen will improve aggregates coating and allow easier compaction. Lower viscosity also reduces energy consumption and emissions during paving.
ACHIEVING HIGH-PERFORMANCE GRADE (PG) WITH HYBRID MODIFICATION
Honeywell Titan® polymers have been used together with elastomeric polymers like SBS (called hybrid polymer modification) worldwide to achieve various polymer-modified bitumen (PmB) grades meeting the requirements of AASHTO M320, AASHTO M332 and various global modified bitumen specifications. In all hybrid formulations, the viscosity is well within acceptable range. In addition, these hybrid formulations have been used to meet the highly challenging specifications such as PG76V, PG76E, and PG 82H where the SBS-alone formula fails to due to high viscosity.
EASIER COMPACTION & FASTER PAVING WITH HYBRID MODIFICATION
Honeywell Titan® provides asphalt mixtures with excellent workability – enabling lower mixing temperatures and construction temperatures, fewer roller passes and a longer paving season. During a Texas Department of Transportation (TxDOT) paving project in 2010, roller pass number was reduced by 33 per cent, fuel consumption was reduced by 13% and VOCs, SOx, NOx and CO2 emission were reduced by 19%, 82%, 43% and 18% respectively.
STRONG RUTTING RESISTANCE WITH HYBRID MODIFICATION
Both lab data and field performance have shown the hybrid modification solution provides better rutting resistance than SBS-only modification, and as a result, the hybrid modification solution has been applied worldwide to fix the rutting issues for highways, airports, racetracks, city bus lanes, and bus stops.
EXCELLENT FATIGUE RESISTANCE WITH HYBRID MODIFICATION
Lab results from Texas Overlay Test (Tex-248-F) show that using the hybrid modification formulation with Honeywell Titan® increases asphalt mixture’s fatigue resistance by 19 % in the short-term oven aging (STOA) condition and as much as 45% when the mixture is subjected to the long-term oven aging (LTOA) versus using the SBS-only modification.
SUPERIOR LOW TEMPERATURE THEMRAL CRACKING RESISITANCE WITH HYBRID MODIFICATION
Lab results show comparable thermal cracking temperature and low temperature strength between hybrid bitumen modification with Honeywell Titan® and SBS-only bitumen modification.
In addition to the lab data indicating excellent thermal cracking resistance, the hybrid modification solution has been used worldwide with excellent low temperature performance for more than a decade, such as in Wisconsin, Alaska (USA), Himalayan region (India), etc.
IMPROVED MOISTURE (WATER) DAMAGE RESISTANCE WITH HYBRID MODIFICATION
Lab data with AASHTO T283 test (used in North America) and the loose asphalt mixture boiling water test (used in Europe) have shown excellent moisture damage with hybrid modification. In fact, Honeywell Titan® polymers have been approved and used globally as anti-strip additives and hence for hybrid modification, there is no need to add the anti-strip additive to meet the moisture damage resistance requirements.
EXCELLENT FUEL DAMAGE RESISTANCE WITH HYBRID MODIFICATION
Hybrid modification with Honeywell Titan® can improve fuel resistance significantly in addition with the benefits listed earlier. Lab data showed SBS-only modification failed the FAA P-601 fuel resistance specification (mass loss <= 2.5%) badly with a mass loss of 13%, while the hybrid modification solution passed the specification easily with a mass loss of 1.8%.
The hybrid modification solution has been used worldwide in multiple airport projects with excellent performance.
SUMMARY
Hybrid modification with Honeywell Titan® polymers helps to produce high quality PmB products which can meet highly challenging specifications with low viscosity and good workability. Asphalt mixtures made with hybrid modification formulations have excellent resistance to rutting, moisture damage, fatigue cracking, thermal cracking and fuel damage. Hybrid modification also helps to reduce asphalt production temperature, paving temperature, compaction effort and environmental emissions significantly.
Honeywell invites readers to contact its experts to learn more about the benefits of Honeywell Titan for their infrastructure and paving applications.