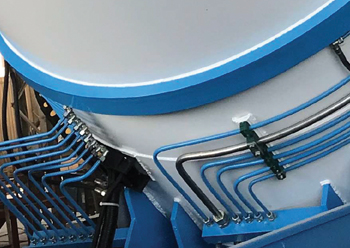
In the previous tech talks, MH Hydraulics FZC, a leading hydraulic solutions provider in the Middle East, discussed hydraulic oil contamination, ways of preventing oil contamination by means of effective filtration, use of desiccant breathers, selection of hoses and fittings, etc.
In this Techtalk, we will discuss the various points to remember while choosing hydraulic pipes and clamps for hydraulic systems.
Choosing the right pipes and clamps is of high importance in design and installation of any hydraulic system. It has a major impact on the efficiency and life expectancy as well as it contributes to energy saving and safety.
Seamless pipes are always used for hydraulic rigid piping. Material used is carbon steel as well as stainless-steel. Seamless pipes are used because of their high strength, low price, and easy leak-free connection. These pipes will be oiled and pickled, or pickled only. It comes with a finish of lacquer coating to protect the metal especially during shipping and storage. Galvanising the inside of pipe should not be done in hydraulic systems because zinc flakes and can mess up O-rings and seals.
The selection of hydraulic tubes is to be done based on the system hydraulic pressure, flow rate, and application. The inner and outer wall of pipes should not be rusted, uneven, and should not be elliptical. They must be smooth, with no corrosion, without oxidation, and free from other defects.
Nominal pipe size (NPS) is used to size the hydraulic pipes. For pipes up to 12 inches, NPS refers to its inside diameter and for sizes above 12 inches, NPS refers to its outside diameter.
There are schedule numbers for hydraulic pipes depending on the wall thickness. For example, schedule No 10 is a light wall, schedule No 40 will have standard thickness, schedule No 80 will be extra strong, and schedule No 160 is extra-extra strong. The most common pipe schedule used in the industry is schedule No 40 because it has the minimum wall thickness good for hydraulic systems and is easily available in the market.
Cold drawn low carbon pipes are preferred. The reason is that it can be easily welded to various standard pipe fittings. But where corrosion resistance is required, stainless-steel seamless pipes should be used.
The selection of pipe clamps is equally important to design a safe and reliable hydraulic system. Factors to be considered are the hydraulic line pressure, weight to be supported and the dynamic load apart from the size and application. The clamps limit the vibration in the system by securing the pipes in its place. There are some guidelines to be followed for clamp spacing in hydraulic piping. Table given below is an example.
Complete clamps will consist of the following parts: weld plates, body, cover plate, and a set of screws.
The weld plates, cover plates and screws are available in mild carbon steel for normal application; 304 stainless steel and 316 stainless steel are used for corrosive environment.
Mostly, the clamp body is made up of polypropylene, polyamide, and aluminum. Polypropylene material is used for normal temperature applications which is from -30 deg C to 90 deg C. Installation, which demands higher temperature polyamide, is used as a clamp body material with a temperature range from -30 deg C to 120 deg C. For temperature of 300 deg C or even higher, aluminum clamps are used.
Various categories are available for tube clamps, as listed below. When in doubt, MH Hydraulics helps you design and select the correct clamping lay-out. It is of utmost importance to select the right clamp for the desired duty.
Many overlook the extreme danger cheap clamps pose. Take great caution with cheap clamps that don’t have specified material certification. The use of unknown material can accelerate a fire. Correct selected clamps can avoid/ delay a fire.
1. Light construction clamps: These are mostly made of plastic and is used to clamp hydraulic tubes under normal or light mechanical vibration applications. Recommended pipe sizes are 6-102 mm.
2. Heavy duty pipe clamps: These are mostly used for clamping hydraulic tubes and pipes under higher mechanical vibration applications. Recommended pipe sizes are 6-508 mm.
3. Double clamps: These clamps are used to hold two parallel pipes in one clamp and only suitable for pipe sizes from 6-42 mm diameter.
4. Tube clamps made of fire-retardant materials: An ideal solution for transport and railway market because of improved safety and efficiency.
5. Steel clamps: These clamps are commonly used for mobile hydraulic because they enable a vibration-free laying of tubes and hoses.
6. Sensor clamps: Fixing clamp for proximity switch. The sensors can be adjusted axially and laterally when mounted on mounting rails.
7. Multi-clamps: These clamps are used to hold 2-10 parallel pipes in one clamp and only suitable for pipe sizes from 6mm to 25.4mm diameter.
8. Tube clamps with noise protection insert: These clamps are used to reduce noise and vibration. Clamp bodies with a separate noise protection insert are a highly effective noise protection and vibration dampening and at the same time a smooth fastening of hoses.
9. Tube fastening on a cylinder: These clamps allow the assembly of tubes and hoses on a hydraulic cylinder.
10. Corrosion-inhibiting clamps: These clamps are made from PP-CR material and commonly used for marine, oil and gas applications because it reduces crevice corrosion between the clamp and tube, and are only suitable for pipe sizes from 6-42 mm diameter.
To conclude, a well-chosen hydraulic pipe and clamp system will enable smooth transfer of hydraulic energy. It can keep vibration and noise levels to a minimum level. However, torque recommendations are extremely important to adhere to.
Vibration leads to leaks on any hydraulic system over a period, therefore, selecting the right solution will give many years of trouble-free operation. Material selection for tubes and clamps done based on the application and environment will offer the maximum safety, especially against fires.
MH Hydraulics can provide technical advice on any hydraulic piping and clamping system and with its CRC’s can install, flush, and commission complete hydraulic systems.
* This article is supplied by