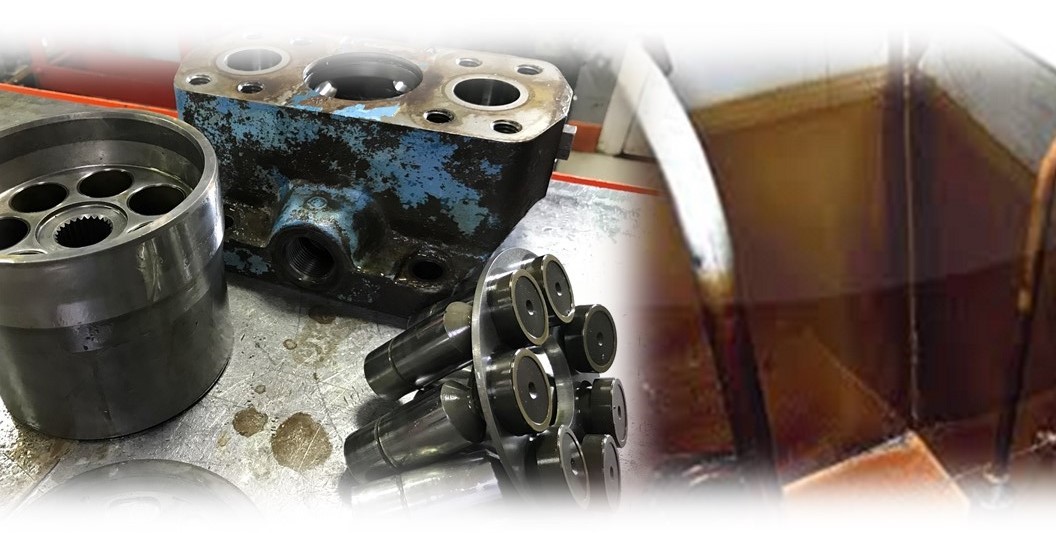
In the third of the TechTalk series on the importance of oil cleanliness for equipment, leading hydraulic solutions provider in the Middle East MH HYDRAULICS focuses on another culprit responsible for oil contamination – varnish, and highlights a solution from Des-Case RMF Systems, a market leader and manufacturer of advanced filtration systems/solutions and desiccant breathers from the US and the Netherlands, to tackle the problem.
In the previous TechTalks released in September and October 2020, it discussed the importance of oil cleanliness for equipment and the ways to prevent oil contamination.
Varnish is a common problem for a wide range of hydraulic fluids and lubricants. It results in valve sticking, shorter fluid life, shorter filter life and unscheduled downtime.
What causes Varnish?
Varnish formation is mainly from oxidation and thermal degradation. When oil molecules come into contact with oxygen under favorable condition, they react to form acids and oil insoluble by-products that form sludge and surface deposits such as varnish.
![]() |
|
Varnish reduces clearance zones. This means a transition from hydrodynamic lubrication to boundary lubrication which increases wear rates of pumps, bearings and gears. Varnish increases friction in components which will result in higher energy requirements. Varnish acts as an insulator, lowering the effect of heat exchangers and lessening the ability of oil to cool. Varnish accelerates wear by attracting dirt and solid particles.
Oil degradation leads to dissolved sludge |
![]() |
|
Oil quickly becomes saturated and suspended sludge makes oil appear dark and cloudy |
![]() |
|
Oil comes in contact with cool surfaces and causes suspended and dissolved sludge to adhere to machine surfaces |
![]() |
|
How to detect varnish?
Early detection of varnish is important and can be done by inspecting oil for visible deposits and discoloration. Oil is susceptible for varnish if switched from Group I to Group II oil or if the oil is blended. A reduction in filter efficiency, filter plugging, high operating temperature, spark discharge in oil reservoir are other symptoms of varnish formation.
Membrane Patch Calorimetry (MPC) is one of the tests used for varnish detection which measures how “dark” the oil is as a result of suspended by-products of oil degradation.
![]() |
|
![]() |
|
The more severely oxidised the oil is, the longer it takes to “turn the clock back”.
Other tests in use for detecting varnish include Ultra Centrifuge (UC); Remaining Useful Life (RULER); Acid Number (AN); Varnish Potential Monitoring, which uses all above tests and includes Particle Count (ISO Code) measuring particulate contamination; Karl Fisher measuring water; and IR Spectroscopy (FTIR), measuring wear metals and additive degradation.
![]() |
How to remove varnish?
There are different technologies to remove and control varnish. One of them is using electrostatic separators, which place a charge on the oil to cause sludge and fine particles to precipitate to a charge collection plate. This is very effective for removing semi-soluble soft particle and preventing deposits. The disadvantages are that it is affected by moisture contamination, expensive and often not well maintained.
Balanced Charge Agglomeration (BCA) is another way where the separators place a charge on the oil to cause sludge and fine particles to agglomerate so they can be filtered out of the oil. This is very effective for removing semi-soluble soft particle and preventing deposits. It is affected by moisture contamination.
![]() |
![]() |
The Des-Case RMF solution is one of the most efficient in varnish removal. The filter unit acts as a kidney loop, continuously circulating fluid through the filter media. This varnish removal system can be configurated for applications with fluid volumes up to 36,000 litres (9,500 gallons). For the best (continuous) results and for the unit to be most efficient, it should be installed permanently or, at least, for an extended time period.
The Long Fibre Cellulose/PP cartridges are specially designed for the removal of varnish byproducts, which are dissolved in the fluid. These cartridges adsorb polar acids by means of special compacted fibres which create an intricate internal flow path. Unlike other technologies, the cartridges do not add water to the fluid. They actually remove water and other solid contaminants. Other advantages include that the unit works independent of (high quantity) water presence in the oil and also works within a wide window of oil temperatures.
![]() |
To conclude, with the changes to oil formulations that have inherently lower solvency and solubility for varnish precursors, varnish will continue to grow as an issue. Much like the impact of cholesterol on the human body, the impact of varnish can remain hidden until the problems become too late. For critical systems with servos and other critical control valves, removing “bad cholesterol” from your oil is as important as removing solid particles and moisture.
Des-Case’s new RMF varnish removal system results on a plastic injection moulding machine
![]() |
* This article is provided by MH Hydraulics
![]() |