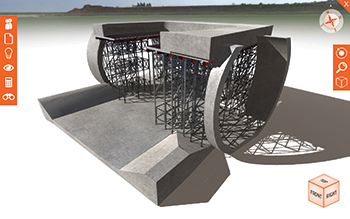
An increasing number of projects across the GCC are starting to utilise building information modelling (BIM), with both governments and contractors realising the benefits of using the software.
BIM adoption in the Middle East – which will change the face of the industry – is, however, still at an early stage in comparison to other countries across the globe. Although larger-scale projects have adopted BIM, which includes the Midfield Terminal Building (MTB) project at Abu Dhabi International Airport, we still have some way to go to ensure widespread understanding and adoption.
Following the Dubai Municipality BIM mandate in 2015, a report was issued in 2016 that explored the adoption of BIM across the UAE. The conclusion drawn was that although the industry conveyed an interest and appeared to understand the value BIM could bring, it was expressed as “beliefs for the future and not as a fact today”.
![]() |
Williams ... calls for the entire supply chain to work together. |
Despite the varied adoption rates across the wider industry, governments and key stakeholders are driving innovations and adoption across large infrastructure projects. In Dubai, projects that span over 200,000 sq ft, or high-rise projects with more than 20 floors are required to utilise BIM. However, if the UAE is to reach its target to 3D print 25 per cent of its new buildings by 2030, we must continue to educate and share the real-world benefits of BIM and technology adoption.
As a temporary works provider, RMD Kwikform recognised some years back that the industry would have to modernise, with traditional processes and methods overtaken by new technologies. More and more often, RMD Kwikform is being approached for 3D and BIM-compliant models by its customers; by working together with them and their clients from the beginning of a project, the company has seen how a joint commitment drives productivity and fuels better communications throughout the construction cycle.
Due to the sheer scale and unique architectural projects in the UAE, the design of the formwork and falsework solutions for these developments is extensive and intricate. To support its customers, RMD Kwikform has created an in-house developed visualisation tool called LocusEye. With engineering designs hosted in the cloud, and with the ability to view via virtual and augmented reality devices, the company provides customers with highly realistic 3D renders of their job site. This not only improves health and safety, but also drives productivity and ensures that its formwork and shoring is delivered and erected on time in line with the construction pipeline.
Through LocusEye, RMD Kwikform is able to generate IFC BIM-compliant models that can sit within its customers’ BIM software. It’s this level of integration the industry needs across all businesses within the supply chain.
There’s a common misconception that BIM is the responsibility of the clients and main contractors; it’s not. We can only successfully adopt BIM if the entire supply chain works together. In order for it to become ‘the norm’ and ensure widespread BIM adoption, it is essential that the entire supply chain collaborates at the start of any project. It’s a case of better communication and a change in mindset.