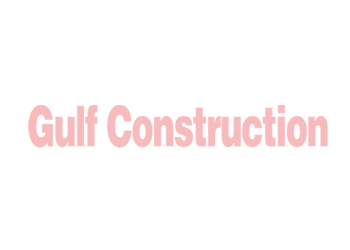

Large variations in temperature and humidity, and erosion by salt and sand in the Middle East makes it one of the harshest environments for metals. To protect metal from corrosion, coatings have to withstand extreme fluctuations between heat and cold as well as high humidity and desert sandstorms.
“Thermoplastic coatings such as Plascoat’s PPA 571 are widely specified in such harsh environments where polyester, galvanised and PVC coatings do not survive for long and require frequent replacement,” Patrick Benson, director of Plascoat Systems.
The UK-based Plascoat Systems achieved an industry first in 1989 with the production of a thermoplastic polymer alloy coating – PPA571 – that provided a long-lasting tough coating for exterior applications. Although laboratory tests could prove its protective characteristics, PPA571 required the evidence of long-term field tests to consolidate its position as one of the leading products in the world for protecting metals from corrosion.
“After 15 years of uninterrupted production, Plascoat has become a benchmark for corrosion protection. The climatic conditions of the Middle East have proven to be just the environment required to test PPA571 in providing protection from sand and salt erosion, ultraviolet (UV) and humidity.'
Whilst modified thermoplastic coating powders have been used for a variety of applications, it is now that the long-term benefits, and therefore cost savings, of such coatings are being fully realised, says Benson.
He remarks: “We are beginning to see a major shift in the market towards thermoplastic coatings, particularly in the Middle East. One reason for this is that a significant number of projects are now seeing a distinct long-term benefit from the use of PPA571 over polyester or PVC-based products.”
Plascoat PPA 571 has proved to be ideal for more than 300 km of fencing poles that stretch across the desert of Dubai, he says. Two lengths of 2-m-high fencing stretching 160 km across the desert have been erected to provide protection for buried gas pipes against damage from vehicles and other passing traffic.
One of the earliest fences to be coated in PPA571 was constructed nine years ago in Dubai. It has shown no evidence of corrosion whatsoever, while the PVC coating nearby has already badly deteriorated, says Benson.
Explaining the properties of the product, Benson says: “Thermoplastics are used primarily for their barrier properties as they form protective layers that are effectively impenetrable to vapours, gases and liquids. For this reason, they are ideal for protection of metal against corrosion as they stop the ingress of oxygen and water as well as prevent the formation of cathodic cells.
“Polyesters, by their chemical nature, are often slightly permeable. Water passing through the coating will bring with it acids or salts from the environment, which attack the substrate beneath and cause blistering and cracking of the coating.
“Functionalised polyolefin alloys (FPA), on the other hand, are hydrophobic so that water will not be absorbed by the coating. Salts cannot attack the coated substrate unless the coating is damaged. Even if the coating is damaged, the adhesive mechanism of FPAs will resist under-film creep and the coating itself is flexible and cannot crack off.
“Cost advantage has also proven to be a decisive factor in the selection of the appropriate coating material. Although the base cost of traditional polyester coatings may sometimes be lower than that of thermoplastic, the life-time cost can be significantly higher, particularly in areas of very high corrosion such as the Middle East because of its shorter lifespan. In addition, thermoplastic coatings can be used without the need for a separate primer, again offering cost savings in application.”
This was one factor in the decision to use PPA571 at one of the best adventure playgrounds in the world at The Jumeirah Beach Hotel in Dubai where five-year tests have just been completed. “The coating has perfectly withstood the harsh effects of coastal salt and sand, intensive UV rays, 100 per cent humidity, high desert winds and rapid temperature fluctuations as well as the wear and tear of over 25,000 children who have used the playground since it opened in 1998.”
This has proven that Plascoat PPA571 really out-performs more traditional products in extreme environments and may explain why a large proportion of PPA571 is sold for use in the Middle East where border fencing provides a major application, he adds.
“With evidence from projects like these it is easy to understand why thermoplastic coatings are becoming increasingly popular,” Benson says. “With demand further strengthened by the achievement of worldwide approvals for the coating of potable water pipes and for food contact, PPA 571 has become one of the most versatile and environmentally sound products on the market.
“Although the exact composition is a well-kept secret, the versatility and durability of these products are derived from a clever blend of functionalised carboxyl-modified-polyolefins. The functionalised carboxyl groups provide adhesion whilst the polyolefins provide the water barrier properties. This makes the coatings free of halogens and of other reactive chemicals and ensures that combustion fumes are low in smoke and have a very low toxicity index.
“In both laboratory salt spray tests of 1,000 hours and in 10-year field tests by the sea, the under film corrosion of PPA571 from a pre-cut scribe was less than 1mm, whilst the coating remained flexible with an elongation at break of over 800 per cent. In addition, any graffiti could easily be wiped clean. This performance noticeably exceeds that of polyester based materials over similar pre-treatments.”
Benson continues: “We knew when we developed the product that it would change the way coatings were applied all over the world. Now we have some excellent long-term field tests to back that up as well as some high profile projects under our belt including the Channel Tunnel and Hong Kong Airport.” More recent applications include the Grand Prix facility in Bahrain and No 1 Court at Wimbledon, skateboard parks in France and even a yellow submarine.
“These high-profile projects demonstrate the fact that architects as well as manufacturers are now specifying thermoplastic polymer alloy coatings as opposed to standard polyesters particularly in harsh or polluted environments.”
“Our experience in the last 12 years has shown that, in harsh environments the long-term benefits of a coating like PPA571 can far outweigh the short-term cost of more traditional methods,” he adds.