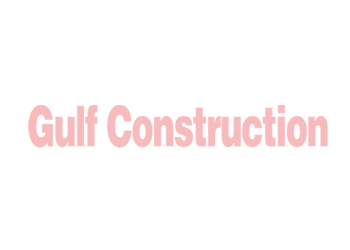
Sipco Paints Company (Sipco) has announced that it has received an accreditation to the ISO9001:2000 standards, upgrading its quality management systems from the previous ISO9001:1994.
The Saudi-based paint manufacturer has posted the new quality management procedures on the company’s internal website to enable employees to familiarise themselves with the system and their role in achieving and continually improving it.
“A recent audit by Lloyds International in November, has confirmed the approval of Sipco Paints Company to the new ISO 2000 standards,” says Dr Ahmed Jomha, Sipco’s general manager.
The new ISO9001:2000 is all-encompassing, quality management. It can help both product and service-orientated organisations achieve standards of quality that are recognised and respected throughout the world.
The updated system will reflect positively on the company’s products and services, as it focuses on the management of all activities that are geared to achieve high standards of quality.
“ISO9001:2000 is not just about quality control or assurance - it is total quality management, which sets out systematic, management and resource requirements that an organisation must meet to achieve its target,” says Dr Jomha.
The quality management system requires the company’s management to identify and meet the needs and expectations of customers and also improve the overall performance and capabilities.
The main principles of the system are based on ensuring customer satisfaction and sound leadership. It also entails involvement of people, a process approach, a system approach to management, continual improvement, a factual approach to decision-making and mutually beneficial supplier relationships.
The system focuses on customer satisfaction through understanding current and future customer needs and meeting their expectations, he adds.
“The management has to establish a unity of purpose and establish the course the organisation takes, thus creating an internal environment in which employees can become fully involved in achieving the common objectives of the company. Such an involvement will make optimum use of the skills and abilities of the staff and thus help achieve the desired results with greater efficiency,” he says.
The updated quality management system aims at continuous improvement and adopts a process approach.
“The new process-based structure of the quality management system is consistent with the plan-do-check-act improvement cycle,” Dr Jomha points out.
The 20 clauses of the old standard are clearly identifiable in this new structure, which encompasses the following:
“We are proud to have achieved this certification as it will hold Sipco in good stead in the local as well as the international marketplace,” Dr Jomha says.
“It is a reflection of the high standards of quality that the company has attained and will assure customers of top quality products as well as the excellent performance and service offered by our personnel.”
Quality and customer satisfaction is paramount at Sipco, he concludes.