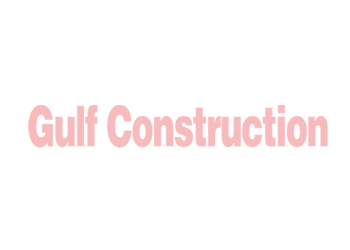
The GRC industry needs tighter controls to ensure that quality standards are strictly adhered to, says GRANT CORBETT, sales manager at Dubai International Reinforced Plastics (DIRP).
The GRC (glassfibre reinforced cement) industry entering into this new era with high hopes and a regained confidence, in a part of the world which has embraced all the fine attributes of GRC, is what we would have hoped for. But sadly, it is not the case.
The industry, in fact, has probably never been at such a low. The possible reasons are many and may include low oil prices (until recently), fewer projects, more manufacturers (of limited experience) and lack of control of the industry.
Let us focus on the last point. It is worth noting that since the introduction of GRC to the Gulf, approximately 20 years ago, the general rule has been for the manufacturer to carry out his own quality control (QC), usually at his own discretion. This is all well and good provided the manufacturer has:
Unlike the ready-mix concrete industry, where a tighter control on compliance was introduced to great effect in Dubai approximately 10 years ago, the GRC industry and its customers, throughout the Gulf, are yet to benefit from such a scheme.
Even though GRC is a 'non-structural' element, the fact remains that it is an architectural element which, if not properly designed, produced and erected (as with all other cladding materials) may present a safety hazard to the pedestrian traffic around it.
For any GRC manufacturer to suggest that its product is 'good quality', based simply on the fact that it has 'never fallen from a building, yet,' is wholly irresponsible.
Any other party accepting it on that basis is very much the same. Quality can only be guaranteed based on consistent conformance to standards at the design stage, the manufacturing/QC stage and erection works.
The British Standard BS 6432:1984 and, more recently, the new Euro Standard EN 1170-2:1998 (currently in the draft stage) both cover the following areas:
(i) Glass content (wash out);
(ii) Water-to-solids ratio;
(iii) Dry and wet bulk density (absorption and porosity);
(iv) Slump;
(v) Limit of proportionality (LoP); and,
(vi) Modulus of rupture (MoR).
At a minimum, with the possible exception of point (iv), all of the above are essential in ensuring the excellent quality of product which GRC should be.
Unless a manufacturer can produce continuous records of satisfactory conformance, there can be no real guarantee on performance.
Just because a GRC manufacturer is well-known, it is not a guarantee that the product is compliant. All manufacturers should be properly audited on a regular basis.
Other essentials for ensuring quality GRC include:
As guidance for engineers and inspectors on site, should you find a broken piece of GRC, it is worth looking at the glass content in as much as 'does it look reasonable', that is, 'does the glass appear throughout the product,' as it should with the exception of thin face mix.
Glass appearing only on or near the back face of the product would suggest an attempt to reduce manufacturing costs, but at the expense of the material performance, leading to early product failure.
Samples can easily be prepared for LoP and MoR testing, if in any doubt.
Another interesting point is white cement GRC required with a plain white finish only.
Good-quality white GRC should not require any coating whatsoever. If it's painted white, find out why. Could it be hiding something?
It is worth remembering that GRC is an excellent material and has a rightful place in architecture.
It should also be remembered that there is no such thing as poor quality GRC, provided it complies with recognised industry specifications.
However, when it doesn't comply, well, it's a different matter. After all, a fruit cake without fruit is not a fruit cake.