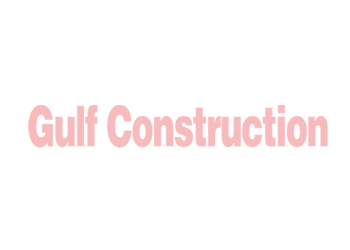
Glassfibre has long been recognised as a very efficient reinforcement material, and is widely used in plastic resins. In the 1950s it was recognised that it could have good potential as a reinforcement for concrete.
Concrete has a very good compressive strength, but is weak and unpredictable in tension and under impact. Glassfibres could offer tensile strength three times higher than steel, an elastic modulus three to four times greater than concrete; and as it does not rust, has no cover requirement. Therefore, it was considered to be a logical reinforcement.
In the late 1950s and early 1960s experiments were conducted in the USSR using E-glass as a reinforcement for concrete. However, E-glassfibres are not resistant to alkalis, and were soon damaged by the highly alkaline hydration products from the cement. Attention then turned towards using special low alkali cements and polymers to protect the glassfibres, but this did not succeed and activity stopped in the mid-1960s.
In the late 1950s the Chinese also started to produce GRC. They used C-glass (chemical glass) with ordinary Portland cement (OPC). C-glass also has no resistance to alkali attack, therefore the Chinese soon had many product failures and the GRC industry was stopped in 1961.
From this basis, the Building Research Establishment (BRE) in the UK started work in 1965. It recognised that what was needed was an alkali-resistant (AR) glassfibre which could be used with OPC, and in the late 1960s it succeeded in identifying a glass formulation which was resistant to alkali attack by using zirconia (ZrO2) in combination with Na2O and SiO2.
Pilkington, one of the world's largest glass producers, entered into a collaboration with the BRE and together they optimised the glass formulation to get the best balance between durability and glass processability. Pilkington then purchased all commercial rights to the development, patented the formulation, and in 1971 commercially launched Cem-FIL and started the GRC industry.
Pilkington and the BRE continued to work together to establish design procedures; methods of manufacture; quality assurance and quality control tests; continued fibre and matrix development; and ageing data, by exposing GRC test panels to natural weathering at sites throughout the world.
All of this was important to ensure the successful and safe development of a new building material, and the care which was attached to this development has resulted in a well-founded industry with the avoidance of problems which may have affected some other new materials.
Interest in GRC has grown steadily. An international trade association, the International Glassfibre Reinforced Concrete Association (GRCA), formed in 1975, has an important role in the issuing of codes of practice and guidelines for the use of GRC. Work now also continues on the production of European standards for GRC of which eight standards are already published covering test methods for GRC (European Norms EN 1170 parts 1 to 8). A new standard, currently in preparation, covers the specification of AR-glassfibre for use in GRC.
In 1990, Cem-FIL was purchased from Pilkington by Saint-Gobain, which is currently the world's largest producer of building products, and has far greater resources for the development of Cem-FIL glass and GRC.
Ageing and failure mode
It is worth considering the mechanism by which glassfibres age in cement. E and C-glassfibres have no resistance to the chemical attack from the alkali hydration products. And since these have a pH of approximately 13, this makes it a very aggressive environment.
E-glass or C-glass in OPC will lose its strength during the curing process, so by the time the finished product goes to the construction site (that is to say, in a matter of weeks only) it is effectively unreinforced. The use of acrylic polymer can provide some protection to the glassfibre, but the benefit is minimal.
Figure 1 visually shows the difference between the performance of E-glass in cement and cement+acrylic polymer after only eight days accelerated ageing (equivalent to a little over two years weathering in the UK), compared with Cem-FIL AR-glass after three months accelerated ageing (equivalent to 25 years weathering in the UK). The E-glass will have ceased to perform any mechanical function long before this. On the other hand, Cem-FIL AR-glass is substantially resistant to alkali attack, although the deposition of hydration products in between the glass filaments, which increases the bond, has an effect of causing some reduction of ductility with time.
GRC in practice
Today, there is a large and well-established GRC industry in the Middle East, founded on the basis of Cem-FIL AR-glassfibre, with local manufacture in many countries. Indeed, the scale of activity in the manufacture of GRC architectural elements - facade panels, sunscreens and decorative mouldings -puts the region in the forefront of GRC production worldwide.
The design freedom and mouldability of the material lends itself well to the style of architecture, and many of the most impressive and exciting examples of GRC in the world may be found in the region.
Allied to this, the maintenance-free performance and durability of Cem-FIL GRC has contributed to the well-respected image of the product.
Conclusion
A successful GRC industry has grown up based on the use of correct procedures and raw materials. Perhaps the most important factor to note is that it is essential for GRC to be made with AR-glassfibre, and that there is a fundamental difference in the composition of the glass itself between AR-glass and E-glass (or C-glass). AR glass contains the vital component Zirconia (ZrO2) in sufficient proportion to confer the necessary alkali resistance. The use of E-glassfibre in a product based on normal Portland cement cannot be considered as a true form of GRC and will almost certainly result in problems arising from a rapid loss of strength.