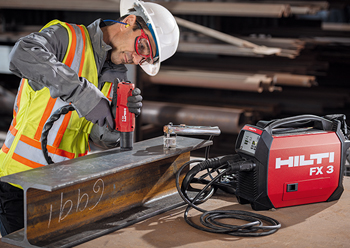
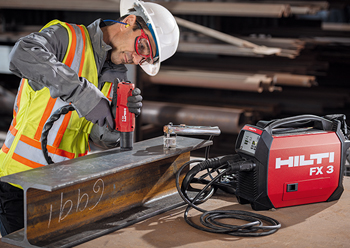
In the shipbuilding and oil and gas business segments, high-quality welding, bolting and clamping is sometimes considered an art in itself. Plus, skilled labour is always in high demand and affects the overall cost and delivery of any project.
Liechtenstein-headquartered Hilti, a leading provider of high-quality, innovative and specialised tools, fastening systems and software-based solutions for the professional user, recognised this as an opportunity for disruption, developing products that can revolutionise fastening on steel.
After years of research and development, Hilti is set to unveil cordless stud fusion, a system that is “nothing less than a game changer for the industry”.
To begin with, cordless stud fusion can cover higher loads (up to 11.2 kN) and thinner base materials (2 mm) than previous Hilti products and is up to 95 per cent faster compared to traditional methods like welding. This fastening method is also safer as it is closer to cold work with almost no splatters or fumes, says Hilti.
![]() |
With virtually no sparks, fumes or radiation, and no angle grinder needed for the surface preparation, cordless stud fusion offers significant health and safety advantages. |
End-user benefits
For customers running their own businesses or managing operations for a company, cordless stud fusion brings a host of benefits. Compared to welding and other methods like bolting and clamping, cordless stud fusion allows for more speed and flexibility in engineering, procurement and construction. Engineers know they will get reliable loads – through repeatable and consistent fastenings – and, therefore, peace of mind that you “get what you spec”, as well as flexibility for design changes. Procurement can choose from a wide portfolio of studs with international codes and corrosion resistance (up to C5). Construction is not only faster than traditional methods, but it can also be done by almost anyone, with minimal training, reducing the risk of installation error.
All of this gives customers more flexibility and more capacity to finish the work earlier. It’s also a cleaner system with no welding slag, burn marks, ceramic ring waste or post-painting. With the easy-to-follow H-code setting, high-quality, consistent and repeatable fastenings are achieved. Plus, with the Active Fusion Indicator (AFI), the installer also gets systematic real-time feedback to help improve the quality of fastening. It is a fully mobile and autonomous system and, therefore, no mains power or trailing cables are needed. With virtually no sparks, fumes or radiation, and no angle grinder needed for the surface preparation, it also offers significant advantages from a health and safety perspective.
Bogdan Radu Mamina, Head of Energy & Industry Region META at Hilti, says: “Cordless stud fusion is a complete shift in the way the industry can now approach fastening on steel. Bolting and clamping can be unreliable, and welding is a skill in short supply on most large shipbuilding or oil and oil operations. Business owners as well as operations managers can now rely on cordless stud fusion to save time, effort, and cost while increasing quality. A simple and standardised fastener design can be used for a wide range of applications and there are virtually no emissions, compared to traditional welding. I believe as time goes by, more and more users will see the benefit of this new kind of fastening on steel and it will disrupt the industry in a big way.”
Further details on the product can be obtained at www.hilti.ae/content/hilti/META/AE/en/business/business/engineering/fastening-on-steel or from the local account manager.
Hilti has expertise in powder-actuated fastening, drilling and demolition, diamond coring and cutting, measuring, fire-stopping, screw fastening, adhesive and mechanical anchoring, digital solutions for fleet and asset management as well as worker health and safety trainings.
Headquartered in Schaan since its founding in 1941, the Hilti Group employs 32,000 team members in more than 120 countries. The company has more than 1,200 highly trained account managers, engineers, and technical specialists throughout Middle East, Turkey, and Africa.