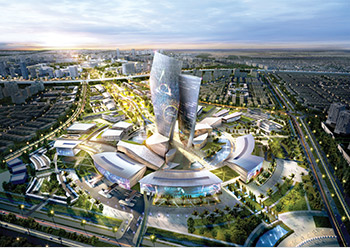
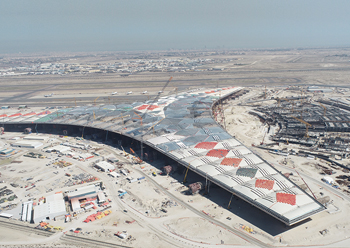
Construction work on the iconic Kuwait International Airport’s new Terminal 2 project continues apace, despite the setback caused by the recent fire at the construction site, according to the main contractor working on the landmark development.
In a statement to Gulf Construction, Limak İnşaat Kuwait Project Director Richard Meredith says: “Work on the Kuwait International Airport New Terminal 2 project is ongoing and continuing in full compliance with the full support of the government of Kuwait and the Ministry of Public Works. Although the fire on March 28 was a serious incident, the structural damage to the terminal is minimal. The structural area affected is less than 0.1 per cent of the building area and will be repaired this year in parallel with other activities.”
“We’ve been excited to work on this project since it started in 2016, and we’re looking forward to completing a unique, world-class terminal. It will be an iconic gateway to Kuwait and be among the world’s most advanced and environmentally conscious airports,” he adds.
![]() |
A rendering of the Fosters + Partners-designed terminal. |
The Kuwait International Airport T2 Terminal project is being handled by Limak İnşaat Kuwait, which was established in 2016 through the Kuwait Direct Investment Promotion Authority (KDIPA).
Under a contract awarded by Kuwait’s Ministry of Public Works in 2016, Limak was assigned the responsibility for the construction, completion, furnishing and maintenance of the Terminal Two project. The scope of works involves construction of the new terminal building, central plant building, water tank building, switching substations, utility tunnels and enabling works, over a 750,000-sq-m site.
The futuristic Fosters + Partners-designed terminal will have a capacity to handle 25 million passengers per year with an initial capacity of 51 gates and stands; and the ability to serve 21 A380s simultaneously. Designed to International Air Transport Association (IATA) Level of Service A, the new passenger terminal is targeting to be one of the first airport terminals in the world to achieve Leadership in Energy and Environmental Design (LEED) Gold certification.
The building will generate its own solar energy by combining a network of solar energy panels installed on the roof with the thermal characteristics of concrete construction, according to Limak.
Apart from the terminal, Limak was also awarded a $561-million contract in July 2020 to handle the construction, completion and maintenance of Package Two of the T2 project, which consists of a car-park building and escape tunnel (capacity: 5,137 cars), landside external works and landscaping, the roof, packaged wastewater treatment plant, roads and bridges, stormwater storage tanks, water supply and utility lines and warehouse.
![]() |
From concept... |
Construction
Limak marked a major project milestone on site in mid-March by erecting the final shell cassette required for the massive domes covering the inner roof of the Terminal 2 project. Fabricated entirely on site, the shell cassettes are a significant component of the terminal’s roof and the project’s objective to achieve LEED Gold certification.
“We marked our last significant project milestone on March 17 by installing the last of 36,964 shell cassettes required for the interior roof of the terminal, and we look forward to achieving more key milestones in the future,” Meredith indicates.
Despite the logistical challenges presented by the Covid-19 pandemic, T2 construction has continued in full compliance with the measures required to keep the site and employees safe, and Limak has invested in its own factories to combat any long lead times or shortages, he states. Limak built high-tech fabrication and concrete casting plants on site to speed up the construction process.
![]() |
All the 36,964 shell cassettes required for the interior roof of the terminal have been installed. |
The shell cassette moulds were constructed and assembled by Limak in Kuwait, and designed by Adapa, a Danish company specialised in mechanical innovation and computer-aided mould manufacturing. The design of the complex structure was undertaken by Germany-based Werner Sobek, while the roof’s construction methodology was handled by the Robert Bird Group, a member of one of the largest Asia-based urban, industrial, and infrastructure consulting firms.
The shell cassettes comprise a composite structure of steel and concrete reinforced with white Portland cement. Each shell, measuring between 3.5 to 5 m and weighing 2.5 to 6 tonnes, has been specially cured, sandblasted, and sealed.
The shell cassettes were fabricated in nine factory areas, equipped with nine portal cranes, two semi-portal cranes and 17 overhead cranes. On average, 100 shell cassettes were produced daily with output peaking at 127 per day. Of the 36,964 individual shell cassettes produced, 31,752 have single curved geometries while the remaining have double curved geometries. These cover a total area of 282,179 sq m.
The shell cassettes are grouped together as modular blocks that, when connected, form the massive domes that cover and span the terminal’s entire interior space. Mounted on the roof, these innovative and unique segmented dome structures span up to 137 m.
– By Bina Goveas