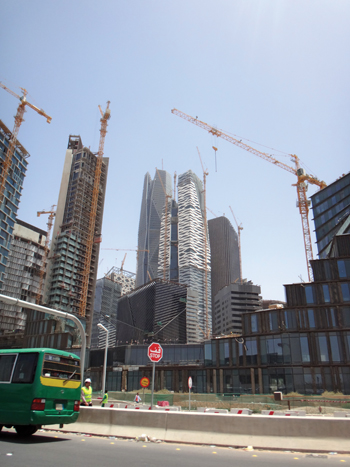
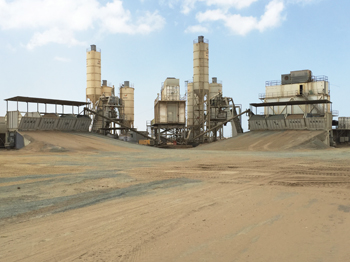
QANBAR READY MIX
Qanbar Ready Mix, a leading name in Saudi Arabia’s concrete industry with a proven track record gained from supplying several large Saudi Aramco construction projects, further enhanced its reputation recently when it deployed one of its rapid response site plant operations for the oil conglomerate’s latest project in Jazan Economic City (JEC).
The $7-billion Jizan Refinery project, which includes a marine terminal and an associated power plant, will be at the core of the massive JEC plan, which aims to transform the economy of the kingdom’s southwestern Jizan Province. An economic accelerator and job creator for the region, this project is also another chance for Qanbar Ready Mix – widely acknowledged as one of the leading, and most trusted, suppliers of quality ready mix concrete – to demonstrate its site production capabilities.
The company’s reputation, gained over three decades, was reinforced recently when it supplied 600,000 cu m of readymix to the giant Sadara petrochemical project in Jubail, an Aramco joint venture with US-based Dow. Qanbar set a record when, in early 2013, it successfully completed the largest single pour on the project with Nasser S Al Hajri (NSH) supplying 5,000 cu m in 18 hours, a delivery rate in excess of 275 cu m per hour.
The company is also an approved supplier to the Royal Commission of Jubail and Yanbu, Saudi Basic Industries Corporation (Sabic), Saudi Electricity Company (SEC), Saudi Royal Air Force and the Ministry of Defence and Aviation (Moda) and many more.
Qanbar’s formula for success in Jizan – as with previous Aramco projects – lies in its insistence on continuity, consistency, efficiency and reliability of plant, equipment, product and service. This policy was developed from experience gained on other similar Aramco projects such as Wasit gas plant, Satorp refinery and most recently at Sadara.
![]() |
A major concrete pour at Jizan Refinery. |
Qanbar Ready Mix general manager Mark Elliott is naturally proud of the company’s ongoing association with Aramco through the strategically important Jizan Refinery project. He says the stage it provides showcases Qanbar’s technical capabilities as it applies its expertise in this geographically remote, logistically challenging operating environment.
“Our business revolves around partnerships that are founded on reliability, a consistency of product and service, and a commitment to excellence, regardless of where the project is and the logistical or operating challenges associated with it.
“It is important to demonstrate to the client that we are in control, that they can trust our ability to deliver the consistent standards of quality and service they expect over a sustained contract period,” he notes.
The company’s commitment is supported by a team of extensively trained, experienced staff whose knowhow, client-centric focus and teamwork controls the production process, ensuring performance targets are achieved.
Qanbar’s Jizan operation was initially built to service a Korean consortium of SK Engineering, Hyundai and Hitachi. The consortium is focused on the primary structure on the project, the 2,400 MW power station. Qanbar’s marketing and business development manager Sharif Kamal has been able to establish lasting relationships with companies such as those in the consortium over a number of years, promoting the partnership philosophy that has been such a success on previous mega projects. The company will also supply other EPC (engineering, procurement and construction) contractors involved in the construction of the power plant and the harbour, as well as supporting industries.
To ensure the consistency of service delivery and to meet Aramco’s exacting product specifications, Qanbar mobilised a twin plant batching facility at JEC. The two plants had previously served the Satorp refinery and Wasit gas plant projects for Aramco and have a solid, well-documented operational track record.
Elliott says by replicating the manufacturing capability at Jizan, Qanbar was able to reach operational compliance before any of the other on-site readymix companies.
Qanbar’s manufacturing facilities in Jizan are supported by a fleet of trucks, including eighteen 12 cu m mixers and six pumps which will be expanded to 25 mixers and seven pumps by this summer, guaranteeing short-delivery cycle times to the refinery site which is only five-minute drive from the project.
![]() |
Work on the Jizan Refinery is expected to be completed in 2017. |
The robust batching facility, part of a multimillion-dollar commitment to serve the Jizan project, is designed to withstand the high temperatures and sandstorms which prevail year-round at this coastal location. A third plant will be erected by this summer, together with a water desalination unit to comply with an Aramco mandate to make use of sea water to protect local resources in the region.
Playing a key role at Qanbar’s Jizan facility are two KTI ice plants, ensuring availability of ice even in the event of a mechanical breakdown or planned maintenance of one unit.
“Ice is a limiting factor in readymix operations, and we are the only suppliers on the project operating two units,” says Elliott, who says the availability of ice is critical, especially in JEC where it will be added to the mix year-round due to higher temperatures.
Control of concrete temperature is paramount to ensure a maximum 30 deg C; and at the time of placing, both chilled water and ice are used in the production process feeding directly into the batching plants. All aggregates are stored in shaded areas after washing.
While Qanbar’s investment at Jizan is impressive, it is the ‘behind the scenes’ activity where the company’s uncompromising approach comes into its own.
This is highlighted in the meticulous focus on quality control throughout the supply chain – from sourcing to processing raw materials. Every aspect of the mix is controlled to meet the concrete design – aggregates, cementitious products, water and admixtures are constantly monitored both in-house and independently not only to comply with Aramco’s specification but also to underpin the company’s quality commitment.
Elliott points out that the role of the quality control team is to act independently of the production process, ensuring the highest standards of compliance.
“They are our in-house police force tracking the production and performance. It is essential to predict characteristic strengths of the mix composition, and end-use trends in order to maintain consistent quality products,” he says.
At the heart of Qanbar’s model is a strict adherence to ISO standards. As a leader in quality and concrete technology, the company is certified to ISO9001:2008 by Bureau Veritas. A dedicated ISO manager continually reviews the company’s performance against internal systems and procedures. Elliott, a concrete industry veteran with broad experience in leading businesses in the Middle East, the UK and North America, demands the highest standards of health and safety and quality compliance. Qanbar is continually seeking ways of raising the bar in terms of compliance, challenging its staff and suppliers to play their part in the process.
Reflecting on Qanbar’s early successes at Jizan Refinery with the EPC contractors Tecnicas Reunidas (for the hydrocracker and diesel hydrotreater packages) and SK Engineering & Construction, and piling contractor Surjin, Elliott says any readymix manufacturer faces its greatest challenges at the start of a new project.
“The start-up process on a new project is the most demanding period. With a focus on consistency and quality and the lessons learned from other major projects in Saudi Arabia, we were able to move through this critical stage more efficiently than our competitors,” he points out.
To achieve success in completing projects of this magnitude, Elliott acknowledges the logistical challenges the company faces, not least the fact that plant, equipment and staff were deployed more than 1,600 km from Qanbar’s Eastern Province headquarters in Jubail.
“This unit is self-sufficient,” he says. “As a satellite operation, you have to quickly establish a supply network and support system. Supplying the Jizan project with high quality readymix products, we are part of a community of subcontractors who are making mission impossible possible.”
In March, the company, a flagship subsidiary of the diversified Al Ansari Holding Company, completed two 1,200 cu m concrete foundation pours, the largest on site so far, which were completed in less than 12 hours by Chinese contractor Sinopec on behalf of EPC contractor Tecnicas Reunidas on the refinery package. Qanbar supplied the microsilica concrete at below the specified temperature due the depth of the structure by adding additional ice to the mix.
JIZAN REFINERY PROJECT
The scope of the project includes a 400,000-barrels-per-day oil refinery, a marine terminal and an associated power plant. The total estimated cost of the project is $7 billion, and is expected to be completed by 2017, behind the original late 2016 schedule.
The engineering, procurement and construction contractors are: Petrofac and Hyundai Heavy Industries; Hanwha Engineering and Construction Corp and SK Engineering & Construction Company; Tecnicas Reunidas; Ali Al-Ajmi Group; Saipem; JGC Corporation and Daewoo Engineering & Construction; and Hitachi Plant Technologies. The contracts were awarded in 2012. Jizan calls for a total supply of more than 2.36 million cu m of concrete across all EPC packages.
The refinery will process Arabian Heavy and Arabian Medium crude oil to produce gasoline, ultra-low sulphur diesel, benzene and paraxylene. The marine terminal will be able to handle Very Large Crude Carriers (VLCCs).