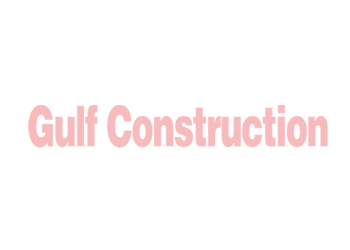

Saudi-based Ali Tamimi Sons - a market leader in the design, manufacture, and installation of tents and tensile structures - is looking forward to put in place an ambitious plan of expansion that will enhance its presence in the region.
Following its success in the domestic market, the company is planning to open new branches in the Gulf in the near future, says executive manager Ayed Tamimi.
The company has already executed several projects in Kuwait through its local collaborator FPS International Trading Company Kuwait and has also undertaken a few projects in Bahrain, including the prestigious Bahrain International Circuit for the Ministry of Works and Housing in Bahrain.
Ali Tamimi, established 55 years ago by Sheikh Ali Abdul Mohsin Al Tamimi on a small scale, is now one of the leading companies in its sector. Although its core business interests lies in the design, manufacture, and installation of tents, tensile structures for car parking and shopping malls, stadium covers, exhibition tents and custom-made structures for both the public and private sector. It also undertakes the supply of all type of tents and structural fabrics.
Says Tamimi: 'The company has considerably expanded into newer areas. Today, we are self-sufficient in cutting and processing the steel structures and accessories.'
From its 10,000 sq m factory premises located in Sulay, Riyadh, Ali Tamimi has also successfully offered canopy solutions to various projects, both within the kingdom and outside. Apart from the public sector, the firm has secured several million-dollar contracts from the private sector as well.
'Our projects are designed by an expert and highly-qualified team of multinational architects, engineers and skilled technical staff who not only lead the way in the region but have also seen the successful execution of projects in many of the European countries as well,' he says.
Besides the Bahrain International Circuit, some of major projects completed by the company include: Mina tent site project phase II in Makkah; sun shades at Al Faisaliah Centre in Riyadh; Hilton Hotel, Jeddah; car-park sheds at Doha International Airport, Qatar; and Tripoli south stadium in Lebanon.
'Construction activity in the kingdom has been on the rise,' says Tamimi. 'Our business has also been progressing gradually and the figures are much better than that achieved in the last few years. We have several projects in our order books for the coming year.'
The company has several projects on hand including the car park shades at the Air Defence premises in Riyadh, Badia Mall and Al Nakheel Mall in Saudi Arabia and work at the Kuwait Oil Sector Complex.
Al Nakheel Mall
For the Al Nakheel Mall, which is expected to open this summer, the company has designed and built a unique 7.6-m-wide tent-like structure over the centre of shopping centre made of PTFE fabric that is supported by a 50-m-height central spiral steel mast. The 4,000 sq m of fabric for the structure is tensioned from the top by a suspension cable from the mast, Tamimi explains.
'The mall that abuts the King Fahad Highway in the heart of Riyadh is truly a gift to the residents of the vicinity,' he says. 'The value of the project is $1 million and the main contractor is Saleh Al Habib.'
Drainage cover for STP
In southern Riyadh, the company has recently undertaken the design work for an architectural cover to enclose a sewage treatment plant operated by the Riyadh Sanitary Division. The $1.4 million contract project entailed covering tanks of 54 m diameter, in a bid to check the odour emanating from the plant. Ali Tamimi provided a galvanised steel frame structure with PVDF fabric placed underneath it.
Air defence premier & head Al Tamimi is also executing a $1.6 million project that entails providing shades for 13,000 sq m of car parking space at the new Air Defence headquarters. Says Tamimi: 'We have drawn up a unique design to complement the hilly profile of the location intended the parking area. Six circular rows of parking area - each with a differing radius - made the design more challenging. The company had to make use of 10,000 pieces of steel columns and plates to get the intended shade requirement.''