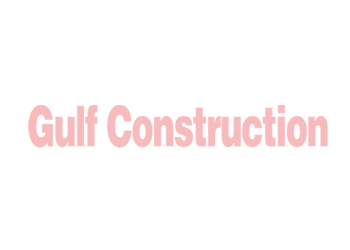

Bahrain's tallest skyscraper - the BD20 million ($53 million) Almoayyed Tower in the Seef District - is close to touching its final height of 172 m with the completion of casting of the central core at the end of last month up to level 47.
The building will soar 71 m higher than the National Bank of Bahrain (NBB) headquarters in Manama, which used to be the tallest structure at 101 m.
It has one basement level, one ground floor, one mezzanine and 44 upper floors, with a helipad facility on the roof. It
will have a shopping mall on the ground and mezzanine floors, while all other levels will be let out as offices. Besides space for 40 cars for VIP parking in the basement, there will be parking slots for 364 cars around the building.
The building sits on a relatively small footprint of 2,025 sq m but enfolds a total built-up area of 48,400 sq m. The project is part of a mega development planned by the Y K Almoayyed Group covering a 11,440 sq m site, which is eventually expected to include a multi-storey car-park and another towering office block. It comprises a central reinforced concrete core with composite floors of steel decks covered with concrete. Externally, the building is enclosed in glass, with touches of natural stone at the entrances.
Since March last year, it has been full steam ahead with the structure shooting skywards almost in lego-fashion. In fact, the structural steelwork contractor Sendai Eversendai of Malaysia - which is renowned for its involvement in towering projects such as the Petronas Towers, the world's tallest building in Kuala Lumpur, and the Kingdom Centre nearer home in Riyadh - was restrained from speeding ahead only by the fact that the core wall was still to be cast, comments Ranbir Mudaliar, senior architect at Mazen Al Umran Consulting Engineers, the local consultant on the project.
The main contractor is the UAE-based Fujairah National Construction (FNC) Company working with Sendai Eversendai. Shadid Engineering Consultants of the UAE is the designer of this project in association with Mazen Al Umran Consulting Engineers.
The civil works are due to completed in March this year and the building will be ready for handover in June.
Currently, a spectrum of activities is under way simultaneously with over 500 workers on site. Alico, the glazing contractor is erecting the curtain-walling which is presently up to the mezzanine level. Because of the special 'Z' sections involved on the lower eight levels of the structure, Alico is currently averaging a floor per week but, on the upper levels, the company hopes to complete a floor per day, according to Mudaliar. Alico's unitized curtain-walling system comprising panels which are 1.5 m wide and 1 floor level high are being installed. These panels are insulated up to a height of 2.5 m and also enclose the fire-stops on each level of the building.
The floor slabs surrounding the core wall have been cast up to the 33rd floor level, while the toilet block work is completed up to the 25th floor, the electrical conduit work is up to the 29th floor, wiring up to 20th, air-conditioning chilled water pipe works up to 26th, plumbing works at the 17th floor and sewage work and fire detection wiring up to 28th floor.
According to Mazen Al Umran, managing director of the consulting firm, a number of factors - right from soil investigation to selecting the MEP services - need to be considered when building structures which are more than 40 floors high.
'Generally, the vertical load on columns of high-rise buildings is over 500 tonnes. Therefore, at the Almoayyed Tower, a skin friction pile foundation has been adopted, as the conventional safe soil-bearing foundations would result in a large area and overlapping of each other,' he explains.
The building structure was analysed for dead, live and wind loads in addition to seismic loads.
A composite steel structure was selected because of its ability to support high vertical loads, as well as the speed and ease of erection, with a lower manpower requirement. In fact, most of the steel elements were fabricated much ahead of time, coded and labelled with their exact installation details and stored on site some three to four months prior to actual erection. Another aspect that the project has in its favour is the availability of extensive open areas around it, which has allowed the contractor to store material on site far ahead of schedule.
Bahrain Foundation Construction Company (BFCC) launched piling work on the project last November. Dewatering work continued from February to June.
Contiguous piles of 450 mm diameter have been used to retain the earth since the excavation went down to 9 m below the central core. A total of 169 friction piles were installed to a depth of -30 m.
The foundation work was completed on May 24 last year, involving one of the longest continuous concrete pours in Bahrain. This event drew up some outstanding statistics: some 4,000 cu m of concrete was poured continuously in 36 hours with the help of six pumps and the operation involved some 700 readymix truck loads. National Readymix was contracted to provide the concrete, however, to ensure a continuous supply Eastern Readymix was later enlisted to meet the required volume of readymix. Around 2.5 tonnes of ice was used to maintain the temperature of concrete at between 22 to 28 deg C from the mixing plant to delivery point at site. The thickness of the basement concrete slab varies from 2.5 m at the edge to 5.5 m towards the central core. A rockwool blanket insulation was laid over the top and sides of the mass concrete to achieve slow self curing and also to avoid differential temperature in and outside the concrete.
The concrete mix comprises Ordinary Portland Cement (OPC) of 280 kg/cu m and fly ash 120 kg/cu m with additives to enable the contractor to pump up to the top floors.
The building was erected at an average speed of two storeys per week, including steel beam fixing and metal decking placement. The central core has been constructed using the slipforming technique for the entire height of the building. The stiff central reinforced wall core houses two shafts of lifts and staircases respectively with a lift lobby. A stationary concrete pump pumps concrete both to the core wall and the surrounding floor on alternate days, thereby achieving a floor cycle of two days per floor. The steel columns of 10.5 m height for three floors were erected with supporting floor beams which abut the central core wall at one end. The steel columns are encased in concrete and the exposed steel beams are coated with a fireproof cementitious spray paint which affords a fire rating of two hours.
Because of the great heights involved, a lot of planning was required to ensure a high degree of safety when moving personnel and material to higher floors, according to Kantharaja, senior structural engineer.
Man and material are being moved up and down the tower using four Alimak hoists. In addition, two tower cranes - which were shipped into Bahrain from the UAE by the contractor specifically for the project - lift steel beams, metal decks and other materials. These cranes are tie braced to the west and east sides of the building at seven-floor intervals.
Another challenge is the coordination of subcontractors on site with the numerous trades involved at the same time.
Six Schindler elevators, the first of their kind in Bahrain, are being installed. They have a with a speed of 4 m/s. One service elevator is being installed for first three floors from basement in addition to two escalators connecting the ground and mezzanine floors.
At handover, the contractor will provide a basic shell of the offices. The air-conditioning equipment, ducting, false ceilings and lighting fixtures etc will be installed by tenants to suit their particular requirements. Common areas will have marble/granite flooring and pantry and toilet areas will come fitted.