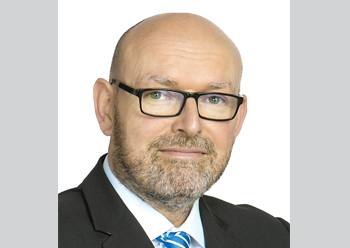
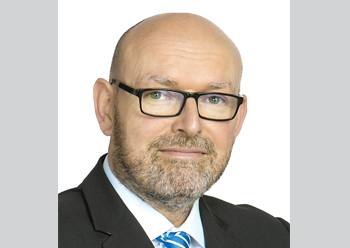
Last month I covered the arrival of the first published form of EPCM (engineering, procurement, construction management) contract: The Blue Book, published by the Institution of Chemical Engineers (IChemE), and we’ll have a closer look at it here.
To recap on EPCM: this is not a construction contract; it is a contract for services. An EPCM contractor will provide services in engineering design development and in procuring materials and equipment, defining works packages, tendering and selection of works contractors, all to be engaged by the project owner directly. During the construction phase, the EPCM contractor will manage the performance of works contractors, suppliers and service providers, on the owner’s behalf.
The layout of The Blue Book is straightforward. The contract comprises the:
• ‘Agreement’ (the signed document, including commercial contract data);
• General Conditions (fairly compact, covering 55 pages);
• Optional Conditions (for the parties to incorporate if they choose);
• Special Conditions (bespoke conditions for the parties to draft, if wanted);
• Specification (the technical definition of the project); and
• Schedules (beginning with the services and the works).
Also included in the booklet are extensive guidance notes on compiling the contract and guidance on contractual issues. As with the other IChemE contracts, The Blue Book is intended for use in the construction of process plant. It contains the expected procedure for process plant, around completion, commissioning and testing, but with amendments, this contract is applicable in other sectors.
![]() |
|
The fee for the EPCM services can be anything from a “cost-plus-percentage” fee to a fully fixed lump sum. Interestingly, one section of Optional Conditions is Target Cost. This provides a mechanism for adjustment of the amounts paid to the EPCM contractor, depending on whether the final outturn cost of the works (and/or the outturn cost of the EPCM services, if they are not priced as a lump sum) are less than, or greater than, the target cost. In this way, the EPCM contractor shares some of the risk (or benefit) in the final cost of the works.
The big question is: how tough is it? To what extent is the EPCM contractor responsible for (and potentially liable for) outcomes? For instance: delayed completion, cost overruns, defects and failure of the plant to meet performance guarantees? What if these things arise from poor decisions by the EPCM contractor in (for instance) programming and sequencing of the works or selection of works contractors or management and enforcement of the works contracts? To answer that, we need to look at the EPCM contractor’s core obligations.
The central obligation is to carry out the services:
• Regularly and diligently; and
• With reasonable skill and care that is expected from a qualified and competent EPCM contractor experienced in the provision of services of similar scope, size and complexity to the services.
This central obligation is supplemented by sections related to the different services, including:
In procurement:
• The EPCM contractor proposes the scope of works and the commercial basis for each works package – which is then “discussed and agreed” with the owner and if they can’t agree, the owner decides the scopes and commercial basis for each works contract. And if that decision causes more cost to the EPCM contractor, it is added to the EPCM contract price.
• The works contract conditions are provided by the owner. The EPCM contractor identifies “suitably qualified” tenderers, conducts tenders and makes reasoned recommendations on works contract awards. Again, if the owner disagrees with a recommendation, its decision prevails but the EPCM contractor may notify its view that the selected works contractor is unlikely to be reliable or competent.
• The EPCM contractor submits a programme for the owner’s approval, showing the sequence and dates for certain events, including performance of the works.
In construction management, the EPCM contractor:
• Takes the role as nominated contract administrator in each works contract.
• Is required to pay delay liquidated damages if the services are not provided in accordance with the services schedule – but time extensions are available for events including unforeseen site conditions, instructions, any event entitling a works contractor to a time extension and (most importantly) breach of a works contract by either the owner or a works contractor.
• Manages the correction of defects by works contractors, and the additional cost of doing so will be added to the EPCM contract price – unless the defect arose from the EPCM contractor’s failure to carry out the services with reasonable skill and care as above.
It is difficult to see much benefit in liquidated damages applying to delays in provision of the services, except perhaps in early activities such as design development and procurement. Once the works get underway, it is obvious that the pace of delivery of the services will be largely determined by works progress.
The Blue Book is (rightly) a services agreement. So long as the EPCM contractor applies the required skill, care and diligence in providing those services, it has no risk exposure to project outcomes such as delay and disruption to works progress, cost overruns, defects or problems with performance testing. On the contrary, these problems are mostly events entitling the EPCM contractor to additional money.
So to answer the question: The Blue Book is not very tough. Could it be tougher? Should it be tougher? Let’s look at those questions separately.
Making a “tough” EPCM really means focusing on outcomes and placing due reliance on the EPCM contractor’s skills and experience. For instance, requiring the EPCM contractor to:
• Warrant that the selected works contractors, suppliers and service providers have the resources and skills to complete the project successfully, that is, to specification, time and budget;
• Warrant that the terms of the contracts with the above parties (including specification, coordination, sequencing, quality assurance, levers for management and enforcement, etc) are sufficient to enable the successful delivery of the project; and
• Undertake to bring about the successful delivery of the project by (and subject to) the above contractual means.
Many big players in EPCM are also EPC contractors. They are expert in managing exactly the same risks when assembling their supply chains and delivering projects under an EPC. It seems logical that the owner should be entitled to rely on the EPCM contractor’s judgment rather than (for instance) interrogating its proposed works sequencing, in order to agree it or correct it. If the owner could do that effectively, why would it need an EPCM at all?
Whatever your view on toughness, clarity is essential. In my experience of disputes following poor outcomes on EPCM projects, owners are frustrated by their inability to pin down liability between the EPCM contractor and works contractors. It is easier to identify liability if the EPCM contractor has at least warranted that it has the tools to deliver the project.
But tougher is not necessarily better. It depends on what the owner and funders are trying to achieve in choosing the EPCM model. Many observers would point out that if owners want to measure contractor performance through outcomes, they really want a fixed price construction contract.
The comparison between EPCM and EPC is usually a false one because rarely will these two models be competing options in any given project. EPCM is most often considered in high-risk projects, with novel technology and built-in difficult or unpredictable conditions. In these projects, the EPC option is either expensive (threatening project viability) or non-existent. I don’t generally see EPCM considered for bank-funded mainstream projects where there is a competitive EPC contractor market.
The Blue Book is a very useful development. I make no criticism of the balance it strikes on risk. There is no right and wrong in this. The publishers have set a benchmark and parties are free to use it as it is or change it through Special Conditions or the Services or by other means. The guidance on completing the Schedules and the guidance on contractual issues are both helpful. And the Target Cost section does introduce outcomes, if that option is taken.
As the IChemE points out, the process engineering world is less adversarial than other sectors. There is more emphasis on cooperation to optimise plant performance, rather than immediate pass/fail tests; and I guess The Blue Book reflects that.
It will be interesting now to see how Fidic approaches EPCM. Its version is due out before the end of the year, and I presume it will be intended for all sectors.
* Stuart Jordan is a partner in the Global Projects group of Baker Botts, a leading international law firm. Jordan’s practice focuses on the oil, gas, power, transport, petrochemical, nuclear and construction industries. He has extensive experience in the Middle East, Russia and the UK.