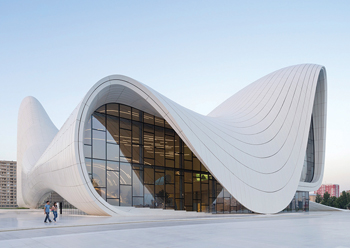
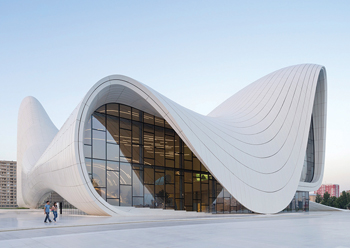
Cladding and façade designs have, in the past, tended towards two-dimensional façade staples glass and aluminium, or maybe occasionally natural stone or even heavyweight options like precast concrete. In recent years though, high-performance materials like GFRP (glass fibre reinforced polymer) and ultra high-performance concrete (UHPC) have been affording a new dimension to the world of architecture.
GFRP has actually been at the forefront of engineering for decades. Think of the sleek shapes of ocean-going yachts. Beautiful, sweeping, elegant vessels built from GFRP – a material durable enough to withstand the harshest marine environments, under constant attack from salt water and pounding bow waves.
This advanced, composite material has also been used to create other striking structures, for example, the elegant and world-famous nose cone of the TGV, France’s intercity high-speed rail service, or the beautiful, powerful forms of offshore wind generators.
![]() |
The San Francisco Museum of Modern Art. |
Consider the conditions in which they must function and survive, retaining their forms and finish with minimal maintenance over decades! Pretty impressive.
Yet GFRP has, until recently, not always been widely considered as an architectural material for cladding and facades.
The use of composite materials such as GFRP is now growing as architects and designers tune in to the benefits of the lightweight, complex shapes that can be produced to provide visually stunning cladding solutions for buildings. No longer constrained by materials where shape and form are limited by coil size, weight or manufacturing process, architects are beginning to recognise that they can achieve a new dimension in their facades.
Around the world, visionary architecture is being realised in GFRP with stunning, almost sculptural facades on buildings such as the San Francisco Museum of Modern Art in the US by Norwegian practice Snøhetta, the Stedelijk Museum in Amsterdam, the Netherlands, by Benthem Crouwel and the Heydar Aliyev Centre in Baku, Azerbaijan, by Zaha Hadid.
![]() |
Al Majlis Pavilion at the Expo 2020 Dubai features a geometric façade in a high-gloss, primary blue colour. |
GFRP can be moulded into a virtually unlimited range of shapes and sizes for cladding, roofing or shading panels. As a cladding material, it can be manufactured in large, long-span elements, limited in size only by transportation considerations. This results in faster installation, with fewer panels to handle and fewer connections to make. This apart, it can achieve a more monolithic appearance with greatly reduced visible panel joints and unsightly mechanical fixings. GFRP panels are lightweight with high strength-to-weight ratios, meaning that they achieve the required performance characteristics at far lower weights than concrete, steel or aluminium, significantly reducing loads on the building structure.
One recent, high-profile example of this was the integration of stunning long-span cladding panels into the façade of the 63-storey KAFD World Trade Centre in Riyadh, Saudi Arabia. For this project, Bahrain-headquartered BFG International, a world leader in composite materials, fabricated 3,180 lightweight composite cladding panels spanning up to 14 m each and capable of resisting the sand-laden loads carried in high winds some 300 m above ground level.
The cladding meets stringent fire and smoke criteria and is compliant with the International Building Code (IBC) based on ASTM E 84 Class A and NFPA 285 requirements. This is key in light of the many recent fires linked to other types of product. BFG GFRP cladding uses constituent non-combustible material in its construction, compliant with the EN 13501-1 standard for resistance to fire.
![]() |
For the Doha Metro, BFG produced curved rainscreen cladding panels. |
Thanks to the laminating process used in production, GFRP cladding panels can also integrate a far wider range of finishes than other cladding products such as aluminium panels. These can include finishes and textures as diverse as travertine, bronze metallic, stainless steel, natural stone veneer and wood effect, as well as a wide range of RAL colours.
The award-winning façade for Qatar’s Doha Metro network – designed, manufactured and installed by BFG International – simulated the natural sandstone of the region in almost 200,000 sq m of curved rainscreen cladding panels. Unique geometric patterns were developed for each station, making each one a recognisable landmark along the city’s newly-laid metro lines.
Whether for the nose cone for the TGV in France, or supplying over 10,000 fully engineered toilet cabins to rail companies such as Virgin Trains, Alstom and Bombardier, or supplying wind generator nacelles and spinners to the likes of Hitachi and Siemens Gamesa, BFG provides highly engineered GFRP solutions for the most demanding of clients and applications across sectors including rail, transportation, marine, wind energy, industrial and leisure.
Like GFRP, UHPC was developed for applications other than facades and cladding – in this case as a non-corrosive, structural product for use where steel, for instance, would previously have been used in bridge construction.
![]() |
KAFD World Trade Centre in Riyadh ... BFG fabricated 3,180 lightweight composite cladding panels spanning up to 14 m each. |
As with GFRP, UHPC is characterised by its incredible strength and durability. This cementitious material is virtually non-porous and has a compressive strength up to 10 times that of traditional concrete. It lends itself well to creating stunning façade and cladding panels in complex three-dimensional shapes for applications where durability and low maintenance requirements are key.
UHPC, when sculpted using precision-engineered moulds produced with multi-axis CNC robotic machines, can help create stunning cladding elements. These robotic machines can create finely detailed tooling for moulds, allowing cladding panels to be produced in highly complex, three-dimensional elements, thus faithfully reproducing even the most detailed shapes imagined by architects and designers.
For example, the Al Majlis Pavilion at the Expo 2020 Dubai features an eye-catching geometric façade in a high-gloss, primary blue colour palette, manufactured using ForteKret UHPC by BFG Advanced Facades. The crisp lines of the three-dimensional panels and the sharp relief were created using BFG’s high-tech mould-making expertise and ForteKret UHPC to stunning effect.
Architecture continues to push boundaries. Buildings are no longer simply conceived as functional boxes, and the shapes and forms being created for structures in recent years continue to excite. The proposed hotel and leisure complexes in some of the Saudi mega-projects such as The Red Sea Project are great examples of architecture that showcase the designers’ creativity and prowess; high-performance composite materials can help translate their vision to reality.
The future of cladding and facades has a new dimension, no longer constrained by traditional materials.
* Peter Walker is Director - Architecture and Infrastructure, at BFG International.