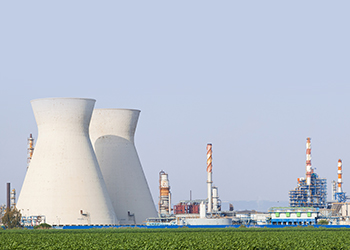
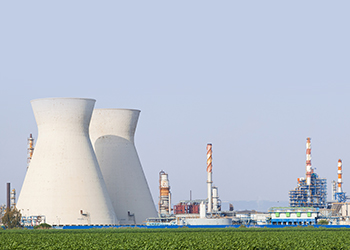
Cortec continues to expand its range of corrosion inhibitors to provide enhanced protection to plant and equipment that can suffer rapid deterioration, particularly in humid climates.
Cortec, which has been boosting its range of Vapor phase Corrosion Inhibitors (VpCI) products to address corrosion over the past four decades, has added two more innovative products to the line. It has recently rolled out VpCI-649 BD that protects metals from corrosive solutions, and VpCI-706 for the protection of diesel fuel tanks and systems.
The VpCI-649 BD is a unique, concentrated liquid formulation that has been designed to provide long-term protection in fresh water, steam and glycol closed loop systems. It also includes preservatives against biogrowth and contains an acrylic polymer to prevent scale formation. It is effective as a replacement for nitrite/chromate-based formulations. The product combines contact and volatile corrosion inhibitors along with anti-scalants in a non-toxic formulation.
“This readily water-soluble liquid for easy application helps solve the problem of disposal, particularly for large quantities of water. It is effective for a broad range of multi-metal applications to stop aggressive corrosion in systems containing fresh water, glycol coolants, etc,” says a spokesman for the US-based Cortec.
VpCI-649 BD is cost effective since low concentrations provide economical treatment. It is also environmentally safe, and does not contain nitrites, phosphates, chromates or heavy metals. The product contains molybdate tracer (VpCI-649 BD MF does not have molybdate).
Typical applications include as inhibitor for close loop cooling systems; in fire extinguishing systems; inhibitor for hydrostatic testing of pipelines, casings, tanks and valves; inhibitor for packer fluid applications; for preventing water-bottom corrosion in oil storage tanks; alkanolamine sweeteners; pulp and paper process equipment; mines, mining and earthmoving equipment; and as inhibitor for lay-up application of cooling towers.
VpCI-649 BD was specified for Abu Dhabi’s Reem Island, which has more than 100 towers consisting of 1.4 million sq m of office space and 850,000 sq m of retail and community facilities. The site will have four district cooling plants with a capacity greater than 1,000 cu m. Two of these are complete, but the towers they are to support are not. The client, Tabreed – Cooltech Energy, required a mothballing solution for the facility for up to two years.
And so Cortec’s VpCI-649 BD was proposed to provide a long-term environment-friendly and cost-effective solution. Dosage was 0.4 per cent to achieve the 24-month protection required.
![]() |
Cortec’s VpCI-649 BD ... protects ferrous and non-ferrous metals from corrosive solutions. |
Fuel tanks protection
Corrosion is also a common problem on carbon steel components shipped overseas or stored for months in humid climates. Metals in good condition when manufactured may be severely corroded by the time they reach their destination or are unpacked from warehouse storage.
VpCI-706’s development came about when Cortec’s was looking for a new VpCI fuel additive for the protection of diesel fuel tanks and systems, according to the spokesman.
“A corrosion problem on carbon steel diesel fuel tanks of a major manufacturer’s heavy equipment prompted the discovery. Corrosion would occur on the equipment tanks after about one month of overseas shipment and would increase during long months of storage in the humid climate of Brazil,” he explains.
Cortec responded to the problem by designing VpCI-706, an additive fully compatible with diesel and biodiesel fuel and tailored to work in diesel tanks and systems. The product provides superior corrosion protection for ferrous metal surfaces both in contact with the fuel and above the fuel level.
Amongst its many important features are its ability to be used in operation, storage, and shipment; compatibility with diesel and biodiesel fuels; protection in liquid and vapour phase, and at liquid/air interface; it does not contain trace metals, chlorides, chromates, nitrites, or phosphates nor additives known to create precipitates and filter issues; and can be fogged or poured directly into gas tanks.
After running tests and ultimately developing VpCI-706, Cortec did a trial on the heavy equipment carbon steel tanks that had inspired the product. The additive was applied to the heavy equipment tanks (which were filled with an operational amount of diesel fuel for equipment loading and unloading) before approximately one month of shipment to Brazil, where further storage would occur. When the equipment arrived at its destination, the filler necks of the untreated and treated tanks were compared. Corrosion was found on the filler necks of the untreated tanks, but the filler necks of the treated tanks had been preserved, and the customer expressed the desire to adopt the new protection method.
“Adding VpCI-706 to diesel tanks before shipment or storage is an important new strategy for protecting truck and heavy equipment fuel tanks and systems from corrosion. It lowers the risk of monetary loss and customer dissatisfaction from equipment that arrives at its destination in a corroded condition,” says the spokesman.
An important advantage of using VpCI-706 is that it does not affect engine performance and can be used in the tank during engine operation. The engine can be safely started in order to drive heavy equipment in and out of the shipping or storage compartment for easier loading and unloading. VpCI-706 can then be left in the diesel tanks for continued corrosion protection during storage and operation of heavy equipment or trucks.
The additive offers protection at a very low dosage rate of 0.5 per cent per volume of the tank to be protected. The presence of Cortec’s proprietary VpCIs means that the tank does not need to be completely filled with fuel, since protection will occur on metal surfaces both above and below the surface of the fuel.
Cortec manufactures VpCI and MCI corrosion control technologies for the metalworking, construction, water treatment, oil and gas, and other industries.