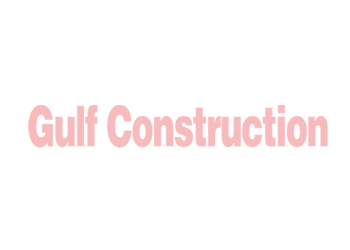

AN INNOVATIVE geomembranes system with electronic leak detection capabilities has been launched in the UAE and will be introduced to the rest of the Middle East soon by the UAE-based BMC Gulf.
Agru-Superflex-el, a product of Austrian company AGRU Kunststofftechnik, is a multi-layer geomembrane consisting of flexible polyolefin. The geomembrane system features an inside layer of electro-conductive polyethylene with a white signal layer, laminated with an electro-conductive geotextile. It is 3 mm thick and 2 m wide and is made up of very low density polyethylene (VLDPE) – 0.915 g/cu m – adding to the high flexibility of the material.
The system facilitates electronic inspection of, for instance, a tunnel liner before and after the installation process to ensure that it is fully intact.
![]() |
The infrared camera. |
“Polymeric geomembranes have been used in tunnel sealing for many years, however, the critical part is usually the vulnerability of the lining system during the construction process,” said Fabian Beermann, division manager at BMC Gulf, the agent for AGRU Kunststofftechnik in the region. “In particular, damages caused by a third party during the installation and construction process are very difficult to recognise. Thus, in case leaks are detected later on, repair is only possible through complex and expensive injection and backfilling procedures. Agru-Superflex-el is state-of-the-art technology that addresses this problem.”
“The system is ideal for the numerous tunnelling projects coming up in the region, particularly in the UAE and Qatar. It can also be used in other applications such as tanks, roofs and reservoirs. With this product, we can tremendously enhance the sustainability of those construction projects, while saving money for the client in the long run,” he pointed out.
The system was developed by AGRU Kunststofftechnik, in cooperation with Strabag and ProGeo using a patented technology, for the construction of tunnels on the Canadian side of the Niagara Falls, in what was a geologically challenging venture.
The gigantic Niagara Tunnel Facility Project (NTFP), which is currently being finalised, used the world’s largest hard rock tunnel boring machine (TBM) with a diameter of 14.4 m to drill through the different layers of sandstones and shales. However, an extensive over-break that slowed the progress of work was experienced due to the porous and brittle nature of the shales. In order to avoid any displacements of the geological formations which could lift the ground above the tunnel or induce earthquakes, an absolutely leak-tight sealing system for the tunnel became essential.
That’s when AGRU’s services were called upon to develop the multi-layer geomembrane with integrated leak detection capabilities. With this new development, it is now possible to check the integrity of geomembranes installed in tunnels. “Even the smallest damages (pinhole) can be identified at an early stage of the installation process and the exact location can be detected. This enables repair work before casting the inside concrete structure, which significantly reduces the risk of leaks in the tunnel, and due to repair having been carried out at an early stage, expensive injection procedures can be avoided,” he explained.
How does it work? The integrity of the geomembrane can be established in a procedure where both its electro-conductive layers are connected to a special monitoring device with the help of a special type of clamping device.
Then an automatic procedure is initiated which continuously increases the voltage to 10,000 V – which is only possible if the main body of the tunnel liner is fully intact. In case the liner is damaged, electricity will flow between the two electro-conductive layers and the voltage will discharge. The decision to use 10,000 V takes into consideration the electric strength of polyethylene, which is much higher compared to air. As a result, this method will not only detect holes but also a significant reduction of the wall thickness.
As it is vital to locate any damage detected in the liner, a special procedure was developed, where the monitoring device is first put into the so called “burn” mode. By continuously supplying 14,000 V, sparks will connect the two electro-conductive layers in the damaged area. Due to the flow of electricity, the temperature will locally increase. An infrared camera can then be used to find the spot with increased temperature, thus locating the damaged area.