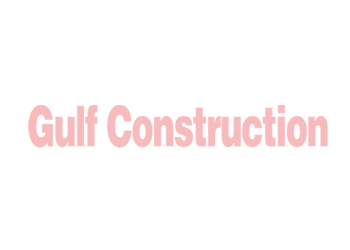
Each bench-drilling task poses a challenge of its own. Different work sites require various hole diameters and lengths depending on the work involved and rock conditions. Whether the rock is hard, soft, abrasive or fractured, today's customer looks for superior performance, fast penetration, high availability, high hole quality with long drill steel service life.
Sandvik Tamrock offers a wide range of hydraulic top hammer drills and down-the-hole drills for bench drilling in construction, quarrying and mining. This range provides a solution for each drilling task where hole diameter, hole depth, drill steels and drilling power are in balance, resulting in top performance and drilling economy.
Top Hammer Drills
Hydraulic top hammer drilling is the most modern of percussive drilling methods used in bench drilling. Hydraulics offer specific advantages in the transmission of forces and energy - as rotary and linear movements can be accomplished with a high degree of precision and applicability - while advances in automation and mechanisation have also helped improve performance levels as well as safety and the working environment.
The percussive energy produced in a rock drill by the piston is transmitted to the rock through drill steels. The piston is accelerated to a certain speed before it strikes the shank adapter. The kinetic energy is transmitted through rods to the bit in the form of a compressive shock wave, which travels along the steel at a speed of 5,000 m/s. When the shock wave reaches the bit, rock is broken by the crushing effect, producing penetration of the bit.
The rock drills' percussive energy derives from the pressure and flow of hydraulic oil. Various combinations of pressure and flow can be selected to provide the required energy per blow and blow frequency. Hydraulic rock drills are designed to operate at pressures ranging from 90 up to 250 bar.
An important design variation concerns the mechanism, which regulates the flow of oil to the piston in the cylinder. In a typical design operated at low pressure, a distributor in a form of a sleeve valve surrounding the piston, opens and closes ports to the front and rear chambers. The advantages of this design are short flow channels, low flow losses and low leakage due to long sealing lengths. There are only two moving parts, the piston and the sleeve valve.
The Ranger hydraulic crawler drills are Tamrock's response to the global needs of quarrying and mining industry, in terms of performance and total drilling economy. It is a track drill range designed to outclass all others in power, versatility, operator comfort and reliability. The Rangers are self-contained bench drills for quarrying and construction, for drilling 51 to 115 mm diameter holes on benches up to 25 m, using R32, T38, T45 and T51 series extension drill steels.
Drilling capacity of Rangers is boosted by a revolving superstructure, which allows the operator to move the boom through a 120-degrees arc to afford vertical drilling coverage up to 17.6 sq m. Because the boom and feed assembly is counterbalanced by the crosswise rear-mounted engine and power pack, these drills are inherently more stable even in the roughest terrain. As the FOPS/ROPS operator cabin turns with the superstructure and boom, for the first time, operators are offered better visibility while drilling. The new low-noise cabin offers plenty of space and a high level of comfort. A single joystick provides direct and stepless control over the whole drilling process.
All three Ranger models - 500, 600 and 700 - are powered by Caterpillar 3116 series diesel engines. Two variable displacement pumps and two gear pumps are directly driven while the air compressor is belt driven.
The Pantera range of heavy-duty hydraulic crawler drills help cut production costs in quarrying and open-pit mining. It offers best value in bench drilling of 89 to 140 mm diameter blastholes by combining high production rates with best hole quality. Panteras are designed to use 51 mm and 60 mm diameter extension drill steels. These heavy rock tools provide high bending resistance, enabling the use of maximum kinetic power for drilling large and straight holes fast, without compromising drill steel service life.
Drilling production holes requires stability from the crawler drill. A rock-steady penetration rate is achieved through its sturdy undercarriage construction, heavy-duty booms and cylinder-rope feeds. Pantera joystick controls provide direct and stepless control over drilling. Percussion power follows feed resistance to allow optimal settings in all rock conditions.
DTH Drills
Down-the-hole (DTH) drills utilise compressed air power in percussive drilling more efficiently than conventional pneumatic top hammer drills. A DTH hammer follows behind the bit into the hole and therefore little percussion energy is dissipated in pipe joints.
Penetration rate is nearly constant, regardless of hole depth. As the piston blows are transmitted directly to the bit, the drill string can be made considerably lighter as it merely imparts rotation to the bit and acts as an air passage to the hammer. A comparatively larger diameter drill pipe lessens the annular area between the pipe and wall of the hole, improving flushing of holes. Drilling accuracy is good. The air expelled by the hammer works as a flushing medium and is passed through the drill bit.
The noise level with DTH drills is lower since the hammer follows the bit into the hole. This helps muffle the noise generated by the piston striking the bit, the exhaust air from the hammer and the ringing pipe noises. With hydraulic rotation heads noise pollution is neglible.
Sandvik has put considerable investment into developing DTH drills in the past years and its BPI down-the hole drills are designed for drilling 85 to 152 mm diameter holes in construction, quarrying and mining industries. These light to medium-heavy self-contained drills are equipped with FOPS/ROPS operator cabins, advanced drilling control systems, automatic pipe changers and rugged telescopic or single section booms for maximum performance. Onboard air compressors, low centre of gravity and powerful oscillating crawler bases ensure maximum onsite mobility. BPI drills are fitted with silenced power packs comprising of diesel engine, hydraulic pumps and air compressor.
They are known for their rugged designs and are particularly suited for drilling difficult rock formations, for precision drilling and toe holes.
While the basic energy source for DTH hammers is compressed air, other functions on DTH drills are hydraulically operated. A conventional DTH hammer at 10 to 14 bar penetrates rock at about a third the speed of a hydraulic top hammer in medium hard and hard rocks, fitted with same diameter bit. About two-thirds the penetration of the hydraulic drill can be achieved by operating the hammer with a pressure of 20 to 25 bar. In medium-soft to soft rocks, penetration rates of high-pressure DTH hammers are similar to those of hydraulic top hammer drills. The main advantages of DTH drills over top hammer drills are:
There are two ways to increase blow frequency and consequently penetration rates of a DTH hammer: by using a larger diameter piston or by increasing the operating pressure.
For the same dimensions of the hammer, impact energy per blow is in proportion with the air pressure. However, the gain in blow energy is expensive in terms of hammer air consumption and drill fuel consumption.
The current trend is towards higher pressures since the percussion mechanism is limited by the diameter of the DTH hammer. DTH hammer manufacturers are also focussing on more efficient ways of using the air when it arrives in the hammer, to achieve greater impact power and higher penetration rates of both high and low air pressures.
Reader Enquiry No. 58