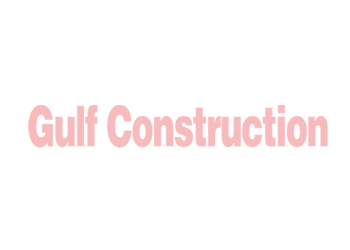

Some 7,800 sq m of precast concrete panels have gone into cladding the landmark Citibank headquarters building in the Seef District.
In what is the first large-scale application of acid-washed precast concrete in Bahrain, Bahrain Precast Concrete Company (BPC) supplied and installed 6,500 sq m of insulated panels to clad the facade and 1,300 sq m of solid panels to clad the columns, beams and other solid structures in the building.
The company also supplied 3,600 sq m of tiles for use in the portal area, on the terraces on the sixth and seventh floors and along the tracks of rail-mounted window cleaning equipment on the roof. These tiles have different finishes, colours and dimensions to suit their applications such as areas of light and heavy traffic. A 2-m-high boundary wall along two sides of the site has also been installed by BPC. This structure serves as a retaining wall for the car-parking area, with about 1 m of it filled in, as the terrain surrounding the site is at a lower level.
Erik Christensen, chief engineer at BPC, summarises the challenging aspects of the project succinctly: "The surface, the geometry, fixings of precast panels and the coordination with contractors."
This high-specifications project did not allow any room for error, according to Christensen.
"We had to produce curved panels of four different radii and ensure total uniformity of colour and texture. The building has many twists to it like a spiral staircase where the outer edge has a wider curve than the inner. With these panels any irregularities in the surface can be immediately detected," he says. "One mistake or flaw and the whole panel had to be rejected."
"Acid-washed precast concrete has a very smooth surface. To produce this type of precast concrete, we created special steel moulds coated with an epoxy paint to ensure a glass-like smooth production surface. These moulds have different curvatures to accommodate the various concave and convex-shaped panels required by the project,'' says Christensen.
The colour pigments were selected by the consultant and BPC imported aggregate from Oman by barge specially for the project as its usual supplies would be too dark for use on the development.
"The Omani aggregate is yellowish or whitish in colour and well-suited for the requirements of the project. The maximum size of aggregate for this project was 14 mm compared to an aggregate size of a maximum of 20 mm that we would normally use on other projects."
This care to ensure uniformity of raw materials also extended to sand which was procured from a single source and carefully stored for the project.
Elaborating on how the panels were installed, he says: "Each facade cladding panel was fixed on four points - the full weight resting on the two points at the base on corbels, with each panel attached to the two upper points with stainless steel threaded rods. The panels - which were up to 6 m wide by 4 m tall, were allowed a movement tolerance level of 5 mm. This meant that additional reinforcement beams were required to hold the panels firmly on the frame of the structure from edge to edge. We also incorporated stainless steel C-rails on the precast panels supplied by the curtainwalling subcontractor to help him in installing the glass.
"Also all seals and joints had to work together. On our panels, for example, we had two joints - a deep and an external mastic joint."
"The panels weighed up to 12 tonnes and we had to use mobile cranes to install some of the heaviest panels at the corners which were out of the reach range of the tower crane."
The contractor had appointed a special facade consultant to ensure a top-class external facade.
Among the areas where installation of panels was complex was the soffit of the 35-m-high portico area.
"The installation work was compounded by the fact that the tower crane's hook was too high and too wide. BPC created a special fork-like contraption which was attached and suspended from the hook to support the panels in place. Here, the panels - which were lighter at 2 tonnes - were fixed with stainless steel threaded rods and locked into place with counter nuts," he says.
Following the completion of cladding works, the entire precast facade of the structure has been cleaned with pressurised air to remove any dust which may have settled on the panels and coated with a colourless water-repellent paint.
Bahrain Precast Concrete was awarded the contract in March 2000. It then set about creating numerous samples in order to perfect the panel production technique. The first panels were cast in June of that year while the last small components for the project were cast as recently as May of this year - the bulk of production having been completed during the second half of last year.
The project required very close coordination with the main contractor Cybarco as well as other subcontractors such as Schmidlin which undertook the curtain-walling - especially in ensuring the compatibility of fixings, he says.
Other precast components produced by BPC to ensure a uniform finish to the structure are precast concrete doors - which have been cast on a steel frame - conduits and boxes to install external lights.
Commenting on the project, Christensen says: "It has been an exciting experience. Our design department has done an excellent job and the entire staff has produced a good team effort. In all, 1,040 panels and 9,000 tiles were cast. We had to work longer hours. However, we are very satisfied with our work and very proud of the job we have done - which has been helped in no small measure through the good coordination with Cybarco and the subcontractors."
Bahrain Precast Concrete Company which has supplied precast concrete to most of the landmarks in Bahrain, right from the monuments at various roundabouts in the country to Bahrain's tallest building the National Bank of Bahrain tower, is currently working on a number of projects in the country.
The company is now seeking to further enhance its strengths in engineering projects such as bridges having already established a stronghold in the cladding sector.