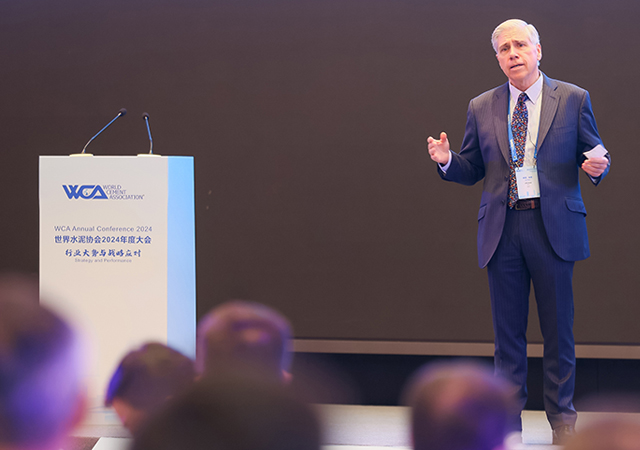
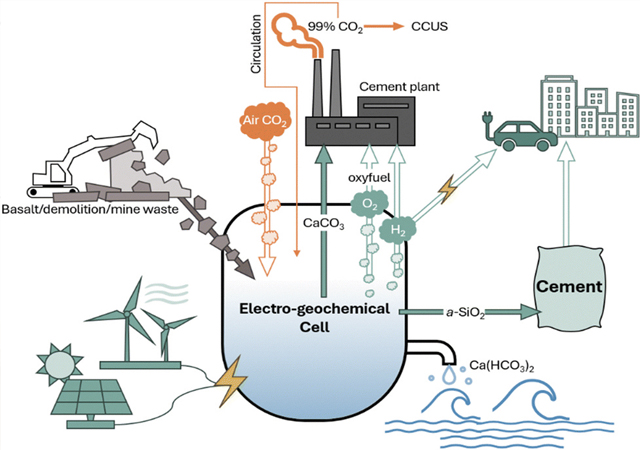
Cement production ranks as the second-largest industrial source of global greenhouse gas emissions, but researchers at the University of Michigan in the US have demonstrated how a low-cost, scalable method could significantly cut its carbon footprint. The approach could neutralise the most carbon-heavy step in cement production without changing the manufacturing process, according to a study recently published in Energy & Environmental Science.
While traditional cement production gets its necessary calcium carbonate from limestone that releases carbon dioxide when heated in a kiln, the University of Michigan researchers can make the calcium carbonate through an electrochemical process that captures CO2 from the air and binds it with abundant minerals or recycled concrete.
“Our newly developed electrochemical material manufacturing approach opens a new area in cement production and waste upcycling at scale,” said Jiaqi Li, a University of Michigan assistant professor of civil and environmental engineering, staff scientist at the Lawrence Livermore National Laboratory and corresponding author of the study.
Production of cement currently produces eight per cent of global CO2 emissions. Demand for the versatile building material, used to make concrete and mortar, is projected to increase by 50 per cent as the world continues to urbanise.
Ordinary Portland cement, the most common form, is made by heating crushed limestone and clay together in a large rotary kiln. Heating the kilns using fossil fuels contributes 40 per cent of the process’s CO2 emissions. The other 60 per cent is the result of heat breaking down the limestone – a sedimentary rock mostly made of calcium carbonate (CaCO3) – into calcium oxide (CaO) and CO2.
The proposed approach, which replaces naturally occurring limestone with electrochemically produced calcium carbonate, neutralises the CO2 released during kiln processing with the CO2 taken up from the air during the electrochemical production.
If implemented at full capacity, the new strategy could reduce global CO2 emissions by at least three billion metric tons – also known as three gigatons – a year, according to the researchers. For scale, 37.4 gigatons of energy-related, global CO2 emissions were reported in 20231. The eight per cent of global CO2 emissions that cement production contributes today could be reduced to three per cent or even further, to net-zero with carbon capture, the researchers add.
“The strategy can change the cement industry from a gigaton CO2 emitter to a gigaton-scale enabler for clean energy and carbon management technologies,” said Wenxin Zhang, a doctoral student at the California Institute of Technology, graduate research intern at Lawrence Livermore National Laboratory and contributing author of the study.
The process works by applying an electric potential across water containing a neutral electrolyte salt in an electrolyser.
As electricity flows, water at the anode splits into oxygen gas (O2) and positively charged protons (H+), while water at the cathode produces hydrogen gas (H2), releasing negatively charged hydroxide ions (OH–). This process creates increasingly acidic anodic electrolyte and alkaline cathodic electrolyte that is harnessed to process calcium silicates.
Protons break apart the calcium silicate to form solid silica (SiO2) and calcium ions (Ca2+). The calcium ions react with CO2 from the air and hydroxide ions in the water to form into solid, carbon-negative calcium carbonate.
While the calcium carbonate is the main product that will feed cement kilns, the solid silica can be blended into cement as a supplementary material to improve concrete or mortar strength and durability, the researchers point out. The gases can even be put to use, with hydrogen gas as a green fuel and oxy-fuel for facilitating carbon capture and storage from flue gas.
Going a step further, the researchers assessed whether the technology is economically viable, taking carbon credit savings into account. The electrochemical approach proved lower-cost and more efficient compared to existing techniques.
“As the present strategy requires minimal or no modification to the business-as-usual cement plants, it has low entry barriers to be adopted by the large cement businesses,” said Xiao Kun Lu, a doctoral student of chemical engineering at Northwestern University and lead author of the study.
This research was a collaborative effort between University of Michigan, Lawrence Livermore National Laboratory, Northwestern University and the California Institute of Technology.
References: 1. https://www.iea.org/reports/co2-emissions-in-2023/executive-summary