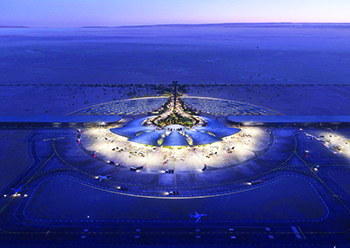
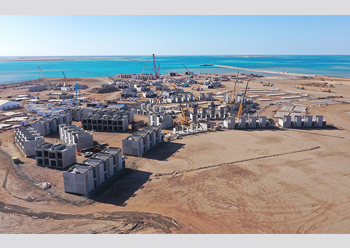
The Red Sea Project, the world’s most ambitious luxury tourism development, has passed significant milestones over the past year and work is on track to welcome its first guests by the end of 2022, when the international airport and the first hotels will open, according to a senior official for The Red Sea Development Company (TRDSC).
Spanning a 28,000-sq-km area along Saudi Arabia’s west coast, the destination is home to a vast archipelago of more than 90 pristine islands, mountain canyons, dormant volcanoes, sweeping desert dunes, and ancient heritage sites. Upon completion in 2030, The Red Sea Project will host 50 hotels, offering up to 8,000 hotel rooms, and around 1,300 residential properties across 22 islands and six inland sites.
“Key milestones already achieved for this year are the completion of the Construction Village, a waste management facility, a central medical facility and 80 km of new roads to better connect the destination,” Ian Williamson, Chief Projects Delivery Officer of TRDSC, tells Gulf Construction.
![]() |
The Construction Village was opened in January. |
“We will soon open elements of the Coastal Village and welcome the first residents. The accommodation and amenities have been built with the comfort of our employees and their families in mind. We want them to be as happy at the development as our future guests, which is why we are developing a livable and sustainable community where they can live, work and relax,” he adds.
Launched in July 2017, the Red Sea Project will in its first phase – which is due to be completed in 2023 – see the development of 16 hotels and 3,000 rooms on five islands and two inland resorts, as well as commercial, retail and leisure facilities and other infrastructure.
This phase also includes the construction of a Construction Village to house the numerous workers that will work on the project; the Coastal Village, which will accommodate the staff working within the development when it opens; an international airport; and extensive infrastructural work including some 80 km of roads, power and desalination network; and district cooling facilities.
“We’re starting to shift our focus from design into completing the procurement phase and construction of key assets. Next year, we welcome our first guests and, while we remain on track, there is still plenty of work to be done,” says Williamson.
![]() |
Williamson ... setting new standards. |
The ambitious project, which aims to tap the natural beauty of its location, has made commendable progress in a short time, with contracts worth over SR15 billion ($4 billion) having been awarded. With work nearing completion on the essential infrastructure and design contracts for the 16 hotels, construction is now under way on the first hotels following the award of two major contracts for hotel development at the Southern Dunes site and Ummahat Al Shaykh Islands.
Early this year, TRSDC awarded the contracts to Saudi-based Al Bawani for civil and structural works across 40 hotel villas as well as utility works and site-wide roads on the Southern Dunes site; and leading Swiss timber construction company Blumer Lehmann, which is responsible for timber construction planning and fabrication as well as supply works for a resort designed by Kengo Kuma and located on Ummahat Al Shaykh Island.
“In the coming months, we will continue to award contracts for hotel construction, largely using off-site manufacturing and modular construction techniques, and the supporting infrastructure needed at each location,” Williamson adds.
Work is also under way on the project’s iconic international airport designed by the UK’s Foster + Partners. Currently land levelling works are well under way to prepare the site. A contract for the airside package has been awarded to an all-Saudi JV of Nesma and Almabani while Aecom will supervise airside construction and control quality. Daa International has been appointed as the airport operator.
![]() |
Artists’ impressions of the hotel developments at the Southern Dunes and Shurayrah island. |
CONSTRUCTION VILLAGE
The Red Sea Project’s Construction Village opened in January this year and is capable of housing up to 10,000 workers. The accommodation exceeds International Finance Corporation (IFC) guidelines, ensuring residential buildings and facilities are both comfortable and safe, Williamson points out. Rooms in the village are equipped with partitions between beds for privacy, bathrooms and showers in the same building, personal safes for belongings, and Wi-Fi coverage in all areas to allow workers to stay in touch with family and friends.
“In addition to high quality accommodation, Construction Village is home to grass cricket pitches, volleyball and basketball courts, football pitches, gyms and cinemas. A supermarket and barber shop will also be provided on-site. Essentially, the village and its amenities will create a real sense of community amongst our workforce, by allowing them to enjoy their spare time and socialise with one other. It is exciting to see the first workers moving in and making full use of all there is to offer at the village,” he says.
To ensure the health and wellbeing of its staff and workers, TRSDC has already set up a 700-sq-m central medical facility within Construction Village.
The central ‘hub’ medical facility, which opened in March, and mobile satellite clinics at construction worksites across the development mean that all workers can readily access medical assistance should they need to.
Commenting on the priority given to setting up the central medical facility, Williamson says: “The project site is on the west coast of Saudi Arabia and its sheer remoteness presented us with a challenge in ensuring that all workers and contractors were in close proximity to medical facilities at any given time. At the peak of construction activity, up to 30,000 workers could be in multiple locations over a huge development area. We knew that having the ability to respond rapidly to medical emergencies had to be a critically important component of TRSDC’s worker welfare programme.”
![]() |
Artists’ impressions of the hotel developments at the Southern Dunes and Shurayrah island. |
So in 2020, International SOS-Al Rushaid were brought on board to manage all medical services across the project. The main building contains an emergency room, consultation rooms and a pharmacy, as well as a fire station and helipad for serious emergencies.
“An exceptional team of nurses and doctors have been onboarded to deliver medical services and treat patients at the central ‘hub’ medical facility and satellite clinics across the development,” he comments.
COASTAL VILLAGE
The 1.5-million-sq-m Coastal Village area will be a permanent asset of The Red Sea Project and is envisaged as a vibrant community, positioned in a prime location on the waterfront. Set to become home to around 14,000 people who will work at the destination, it includes villas, townhouses and apartments and will provide a range of amenities like hospitals, schools, leisure facilities, fitness centres, and beach clubs including retail and dining outlets.
“In addition, it will be home to our first hotel, geared towards providing a place to stay for visiting employees and consultants during the development phases, and later a place for guests of residents to stay. Work on the management hotel is close to completion and the asset will open in June this year,” says Williamson.
Elaborating on the construction of the hotel, he says: “The contract for the construction of the management hotel was awarded to Saudi Amana Contracting, a subsidiary of Amana Contracting Group, which took a schematic design and developed a detailed design and construction documents that fed directly into its manufacturing processes. Room modules are delivered with bathrooms, lighting, power, ceilings, and tiled floors, all completed.”
“We challenged our new partner to bring a fresh approach to construction that aligns with our sustainability commitments. The hotel consists of pre-finished volumetric concrete, modular units built in a dedicated factory opened in nearby Rabigh, which have been delivered and set in place on-site,” he remarks.
![]() |
|
SUSTAINABILITY
Throughout the development of The Red Sea Project, TRSDC has maintained a focus on sustainability and the use of renewable energy, while setting new benchmarks in regenerative tourism.
“A tourism project of this size (roughly the size of Belgium), powered solely by renewable energy, has never been achieved on this scale anywhere in the world,” Williamson remarks.
“We want to deliver a tourist destination that limits the environmental impact through the provision of zero-carbon emitting and zero-waste generating utility services that truly sets new standards in regenerative tourism,” he adds.
In fact, the highest value contract to date on The Red Sea Project was to provide environmentally responsible energy for the project, with the public-private partnership (PPP) having been signed with Acwa Power at the end of last year.
Under the PPP, TRSDC will power the first phase of the destination by 100 per cent renewable energy, using solar panels and wind farms, with no connection to the national grid.
“As part of this partnership, we are creating the world’s largest battery storage facility at 1,000 MWh to enable the entire site to be powered by renewable energy 24 hours a day, seven days a week. Additionally, there are plans to create the biggest district cooling plant in the world powered by 100 per cent renewable energy. The resulting saving in carbon dioxide (CO2) emissions to the atmosphere is equivalent to nearly half a million tons each year,” he claims.
TRSDC has partnered with green concrete experts, AlFalah Ready Mix, to supply a part of the destination with structural low-carbon concrete, manufactured using recycled raw materials.
In addition, since the outset of the project, TRSDC has worked hard to adhere to its zero waste-to-landfill policy across all areas of the project, even in the construction phase. It opened a waste management facility on site earlier this year to ensure no materials used during the development of the project end up in landfill.
“Our waste management facility creates a new benchmark for large-scale development projects not just in the Gulf region but globally,” he says. “We’ve considered all forms of waste generated by the construction process and are using manual picking lines and advanced machinery to sort and treat the different materials. As a result of this process, tons of waste material is turned into smaller elements that can be reused for other purposes, such as for building roads.”
Furthermore, all food and organic waste at the project is turned into nutrient-rich compost that is used to supplement the 15 million plants at our 1-million-sq-m landscape nursery. As construction continues, this compost will also be used for the landscaped areas across the development.
Any non-recyclable, non-compostable materials that remain after this process are incinerated, and the resulting ash used for the manufacture of bricks.
The plants grown in the landscape nursery, opened in March 2020, will predominantly be native species. Additional desert-dwelling species may be included, after ensuring that any imported species will co-exist with the local flora and fauna.
CHALLENGES
Commenting on the challenges of the project, Williamson says: “Our commitment to sustainability has presented us with challenges, particularly as it has meant that we do most of our manufacturing off-site. Reducing the materials being handled, fabricated, and consequently wasted on site has allowed us to reduce the overall environmental impact of the project.
“However, logistically this has been a challenge as it has meant that we have had to carefully transport each of the 70-ton units by road, and then use a very large 600-ton crawler crane to install them. This required us to be meticulous in our approach as any mistake made during this process could have had a detrimental impact on the surrounding environment.
“Furthermore, a lot of what we are doing at The Red Sea Project has never been done before which presents us with unique challenges that we have to overcome day to day. With a remote location, it was essential that we have the correct infrastructure in place so that work could be carried out effectively and efficiently. It was, therefore, a priority for us to develop comfortable accommodation for our workers to live in while they help make our project a reality.
“I am proud at how we have successfully managed to create a thriving community with top-class housing and amenities, despite being situated hundreds of kilometers from the nearest city,” he adds.