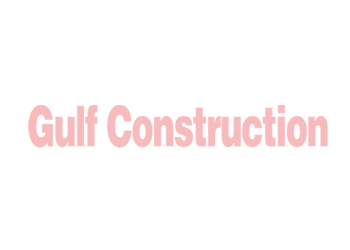

EF Products (EFP) has introduced what it describes as a revolutionary machine that helps composite panel fabricators create difficult shapes quickly and accurately.
The PanelMaker Vertical Router, as it is called, is a CNC (computerised numerical controlled) machine that has been designed from the outset as a fast, efficient composite panel processor.
The machine eliminates the arduous task faced by fabricators in meeting the demands of today’s architects for complex shapes. A spokesman for EFP elaborates: “Since the introduction of composite panels to the region in the 1980s, fabricators have had to make do with vertical panel saws designed for cutting plywood and MDF (medium-density fibreboard) board. They do the job but are slow, very labour intensive and prone to human error. They cut and groove straight lines but when it comes to coping with the modern shapes that architects love to use in today’s buildings, then a proportion of the work has to be done with a manual router. This is very slow, inaccurate and not cost effective.
“In an effort to mechanise the processing of the difficult shapes, aluminium fabricators had to make do with the introduction of the horizontal router to the Gulf some six years ago. But that too was a machine designed for the woodwork and signage industries. It was slow but nevertheless a big step forward from the original panel saws.”
The PanelMaker Vertical Router offers a fast, efficient solution to these problems, according to EFP.
“Being vertical, it saves space with a substantially-reduced footprint – a big plus for cramped workshops where space is at a premium. With the gantry travelling in the vertical plane and the rare disintegration of a tool bit flying out of harm’s way, any health and safety risk is reduced to an absolute minimum,” the spokesman points out.
Being CNC controlled, PanelMaker can accommodate any shape to please the most demanding architect, he adds. Drilling, routing, grooving and cutting with different tools immediately available from the 10-station built-in tool changer is all done automatically without the need for the operator to physically change tools, he says, adding that all tools supplied with the machine have been designed specifically for composite panels with precision and long life being the criteria.
In addition, it has a uniquely-shaped circular cutter head for ultra-high-speed grooving at speeds five times faster than the horizontal routers available in the market today, he claims. The specially-shaped grooving tool ensures the fold always takes places on the centre line of the groove, facilitating accurately-sized panels every time so that panel creep on site does not become a problem.
Sturdy construction, a gantry beam with twin motor drives, a motorised fan-cooled 5.5 kW router motor and an enviable vacuum hold down the system to keep the work piece in place on to an MDF sacrificial board to ensure that there is no damage to the tool tip.
An efficient dust collection system ensures a clean work place coupled with the advantage that being vertical, any residual swarf falls to the floor and will not get trapped between the board and the panel.
“The vertical loading of the machine is easier and more operator friendly than horizontal machines,” he continues. “Manoeuvring large sheets of composite panel is much easier in the vertical plane whereas horizontally it is often a three or four-man problem.”
To save labour, EFP has even developed a unique Panel Loader that can be added in line with the vertical PanelMaker to make one-man processing of the largest panels simple, thus saving time, money and backache.
A fully-programmed industrial PC with a 17-inch colour screen makes easy work for the operator who controls the operation from a remote controller. Alternatively, the controller can be linked via an Ethernet cable to the drawing office linking to another optional copy of the software. Files in DXF format from customers or architects can be managed and sent direct to the machine where the operator can launch all the processes.
“The ultimate advantage is the sophisticated user-friendly software that enables the operator to enter the panel shapes and sizes and then nest and optimise. The material saving can quickly pay back the cost of the investment. In addition, the software can be used for estimating at the tender stage of projects, even down to calculating the time taken to produce the panels,” the spokesman says.
At the production stage, it can be linked to a bar coding system to monitor production and even integrated with “E to I” software to produce the estimate, full production reports and costing then finally prepare the invoice.
PanelMaker can machine many different types of panels from conventional aluminium composite to stainless steel and copper as well as plastics and wood. A range of different-sized machines to meet all eventualities and budgets ensures that this is the “must-have” machine for automating the manufacture of composite panels, the spokesman comments.
“Demonstrations can be arranged in EFP’s workshop where prospective clients can experience the high performance and superb quality of the finished panels processed on the PanelMaker. The workshop also doubles as a training centre for operators so they can be trained in advance of the delivery of the new machine. Therefore, no time is lost,” he concludes.