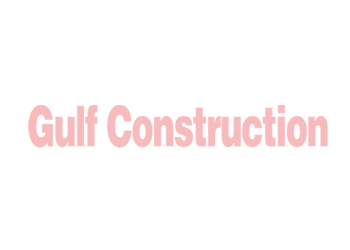
ALABNIAH Precast Concrete Building Factory of Saudi Arabia precast concrete specialist, which launched production late last year, has already registered projects worth SR170 million ($45.3 million) within its first year.
The Al Khobar-based company is hoping to double its sales over the coming year, while ensuring customer satisfaction through the supply of high-quality precast concrete products and on-time delivery.
Alabniah, which offers a diverse portfolio of products, has expanded its range with the launch of a new production line of pre-stressed double tees and beams in June. It provides various kinds of precast concrete products as well as intelligent precast solutions and concepts to the entire construction industry in Saudi Arabia and the other GCC countries, contributing to higher construction speed and quality, according to Ahmad El Lakkis, the company’s executive vice-president.
He claims that Alabniah is the first factory of its kind in Saudi Arabia and one of the few in the GCC countries to produce double walls using the latest technologies available in the world.
Its turnkey services include provision of design, production, delivery and erection of complete precast solutions. These solutions have already been supplied to a range of projects in Saudi Arabia including King Faisal University’s (KFU) Electronics Building No 46 in Al Ahsa, where it was also involved in the supply and erection of hollowcore slabs and double-tee slab under a subcontract from Issam Kabbani Group; and a 200-villa development for Al Fouzan Trading and General Construction, also in Al Ahsa.
Other residential projects include a 1,000-villa Saudi Arabia National housing project for Saudi Oger in Riyadh, and a 34-villa complex as well as boundary walls and hollowcore slabs for a 45-villa (RC-C01 type) development, for Redico in Jubail.
The company has been engaged in a large number of other projects, mainly in the Eastern Province including:
• Supply of wire mesh reinforcement and hollowcore slabs for Weatherford slabs facility and hollowcore slabs for Baker Hughes Technical Centre, both in Dammam under a subcontract from Arnaout Contracting Establishment (Arcon);
• Supply and erection of 200-mm-thick hollowcore slabs for King Saud shops for Al Wasseteah Contracting in Dammam;
• Supply and erection of a boundary wall for Tamdid Pipe in Dammam;
• Supply and erection works for Nesma & Partners/Roots compound in Jubail;
• Supply and delivery of KT-820 lattice girders for Saad Ali Ashamrani in Riyadh;
In addition, Alabniah also produced and erected the precast elements that have gone into the construction of the boundary wall, quality control laboratory and workshop at its own factory in Dammam.
Alabniah’s office and factory facilities are located in Dammam’s Second Industrial City over a 112,100-sq-m plot of which accommodates 23,000 sq m of covered production area.
“Alabniah’s manufacturing facilities comprise state-of-the-art, fully-automated production lines equipped with computerised plotters, shuttering-robots, fully-automatic mesh welding machines, extruders, computerised concrete distributor and curing chambers,” says El Lakkis.
Alabniah’s technical department is equipped with state-of-the-art design/modelling/structural design software, CAD/Tekla/STAADPRO, apart from the ERP (enterprise resource planning), CRM (customer relationship management) and production planning and delivery software, to ensure customer satisfaction.
He says the technology utilised is tailor–made for its fully-automated production facility and the information is transferred directly from the technical department to the computerised robots and plotters in the factory.
“Our highly-experienced engineers, designers and industrial professionals can support clients at all stages of their projects – from design, through production to erection – to provide intelligent precast solutions and ensure optimum results,” says El Lakkis.
With Alabniah, he claims, customers will achieve superior quality that cannot be matched using traditional building methods; improved project management; a safer working environment; zero waste; and improved fire safety.
“Using the company’s precast products eliminates the need for additional soundproofing or scaffolding and speeds up the construction of a structure while minimising defects. We provide timely delivery of products, thus contributing to overall cost efficiency,” he adds.