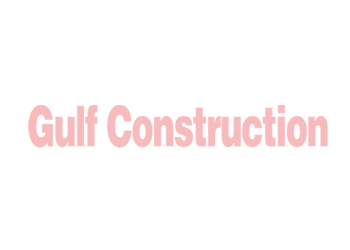

A NEW software and mass production process by UK’s Formtexx is set to give flight to the architect’s imagination by enabling the creation of flowing freeform curves for the latest organic designs, as either façades or features inside or outside buildings in a wide range of metal panels.
The technology – launched recently at The Building Centre in London – makes it possible to achieve three-dimensional double curvature façades in construction using metal forming technology influenced by the automotive industry.
“For many years, architects have designed facades featuring three-dimensional curves but because of the complications of manufacture, they have always been installed as optimised two-dimensional faceted curves – not at all what the architect wants to see,” says John Gould of Formtexx.
“Our technology now gives architects the freedom to create freeform structures never before attempted because of the high cost, weight and time of manufacturing sheet metal for bespoke design,” he adds.
Traditionally, sheet metal development falls into two categories – manual analogue techniques of wheeling, rolling and incremental sheet forming that produce unique shapes in small quantities with inherent dimensional deviation; or die stamping, or fabrication of identical shapes in mass production quantities.
![]() |
A double curvature 4-mm aluminium panel. |
Formtexx anticipates an entirely new third category, which combines the benefits of digital manufacture with non-repeating freeform geometry as standard, and which is compatible with CAD/CAM/CNC metal plate/sheet forming and CAD in mass production quantities with automotive precision. With this technology, Formtexx has closed the gap between digital design and digital manufacturing in the facade sector.
Gould likens the digitally-controlled system to a large desktop printer that can handle vast amounts of data spooled to individual sheets. A curvature panel is said to be produced every 20 minutes no matter how complex and different each panel may be.
“Formtexx combines the expertise and resources of luxury automotive bodywork manufacture, high level software development and 3D surface manipulation,” he says.
The first M-Form machine is now operational and the company says it can produce façade components using thin, lightweight metals, such as aluminium, stainless steel and titanium. Other suitable materials include mild steel, Cor-Ten weathering steel and metal/polymer composites.
The manufacturing quality is said to be equal to automotive tolerances by simulating the effects of variable tool forming on plates for dimensional accuracy, spring back, residual stress, surface quality and throughput.
![]() |
A computer-generated image of a double curvature shape. |
Additionally, the non-impact Formtexx machine, which handles sheet metal as thin as 0.7 mm, does not touch the surface of the panel that the world sees, which means that pre-polished or painted sheets can be used. Even perforated sheets for use as sunshades can be fabricated as well as sheets with Islamic designs laser cut on to the surface or through the metal. Using thin materials means less weight on the structure and it is ideal as a rainscreen.
“This truly unique process is set to change the appearance of buildings with some really different shapes. Ideally suited to mosque domes, spheres or just 3D facades, there is now no limit to an architect’s imagination to create a smooth almost seamless façade and turn a fantasy into a reality,” says Gould.
Formtexx was established specifically to manufacture freeform metal facades and formwork for the architecture and construction industries using new, purpose-built design-to-manufacture software and revolutionary metal forming technologies. It offers customised freeform metal surfaces to automotive quality standard in production quantities.
The company combines the expertise and resources of leading companies in the fields of automotive bodywork manufacture, high level software development and 3D surface manipulation.
The company is represented in the Middle East by Euro Façade Products, which has offices in Saudi Arabia and the UAE.