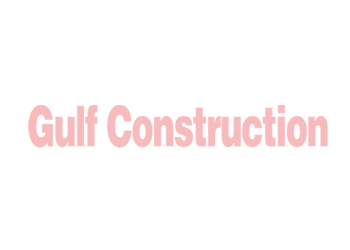
THE civil engineering stage of the first phase of the major expansion of the LNG Port at Ras Laffan, Qatar, is now nearing completion after almost three years.
This phase is the first step in a major expansion of the port facilities at Ras Laffan Industrial City, which already has two of the world largest natural gas terminals.
The contract, valued at $2 billion, by Hofstade-Aalst, Belgium and Qatar Petroleum, is being undertaken by Jan de Nul Group in a 50:50 joint venture with Boskalis. Van Oord is under contract to the main contractors to undertake construction of the breakwaters and associated works.
As the first phase nears completion, the massive volume of material deployed is evident by the several kilometres of structures standing several metres above the water line.
Over 10.6 million tonnes of local rock, together with a further 4.2 million tonnes imported from the UAE, has been put in place, either by side dump barges or by dumptrucks. Over 1 million cu m of concrete was used by the prefabrication yards for production of 185,000 precast concrete antifers and 36,000 concrete acropods, for the armour layer construction of the breakwaters. The antifers are 1.5 cu m, 3.0 cu m and 3.5 cu m in size while the acropods range from 3.0 cu m to 5.0 cu m.
The rock and precast concrete elements were used to profile and protect the land reclaimed from the placing of more than 20 million cu m of dredged limestone and 25 million cu m of offshore sand.
There is also more than 900,000 sq m of geotextiles incorporated into the structures and the causeways and breakwaters are finished off with 3.4-m-high crown walls and 50-m-wide by 2.15-m-deep reinforced road slabs (typical) for which more than 170,000 cu m of concrete was poured.
Throughout the project, the contractors have utilised 45 heavy-duty excavators and high-capacity crawler cranes, 40 rigid and articulated dumptrucks and 20 wheel loaders as well as other support equipment. The number of people on site deployed by Van Oord and specialist marine and coastal engineering plant hire company Abeko peaked at over 700. Work has progressed non-stop, 24 hours a day, seven days a week.
Abeko has the contract to provide the machinery and operators required by Van Oord for the construction of the 22.5 km of causeways and breakwaters. They are now applying the finishing touches before handing over to client for fitting out.
The contractors are currently undertaking the final surveys and, as appropriate, are working with the Abeko team to do any remedial and finishing work to ensure that all constructions are in accordance with design specifications.
This work calls for precision working in order not to disturb material already in place both from a variety of land-based equipment and from the sea, where an O&K RH90C mounted onboard the Abeko Server 1 is helping with final underwater profiling of the breakwaters.
Precision working
“All the works are designed to very demanding specifications,” says a spokesman for Abeko. “The many kilometres of breakwaters have varying specifications depending on their location. However, a typical cross-section is, at sea bed level, approximately 133 m wide from toe extension on one side to extremity of armour rock on the other side. They rise to a maximum height of almost 21 m (of which 12 m is below the waterline). The breakwaters are profiled to a slope of 33 degrees on the seaward side and 37 degrees on the harbour side.”
Typically, the seaward-side of the embankments comprise 3.0 m layer of selected quarry stone up to 500 kg; a 1.8 m layer of heavier 500 to 2,000 kg rock and a 3.2 m protective layer of antifers or acropods depending on position. At the foot, there is a large breakwater toe with 5 m extension.
On the harbour side, the composition is a 1.80 m layer of 500 kg quarry stone; a 1.15-m-thick under-layer of 100 to 500 kg quarry stone and an outer layer, 1.80 m thick, of armour rock (500 to 2,000 kg).
However, such is the variation in the dimensions – according the water depth and where additional protection is required such as on the roundheads against possible ship impact – that there is nothing ‘typical’ about the project. This is why it has proved to be so challenging, says the spokesman.
The challenges for the contractors were many and included the scale of the project, the time restraints, logistics, the many variations, very demanding quality control for materials and the construction tolerances (as little as ±0.2 m). To achieve this, they had to deploy the very latest technology, advanced computer-aided systems, sophisticated, heavy-duty machines configured specially for the works and a team of highly skilled operators, he says.
Men & machines
Critical to the works has been the 52 m long, 470-tonne Abeko Server 1, which, with 30-m-long spud legs, is able to work in water depths of up to 24 m. The large deck area of 6 m by 40 m allows the use of larger, heavy-duty excavators. For Ras Laffan, the machine selected was a 230-tonne O&K RH90C with triple boom, equipped with a 30 m boom and GPS Prolec Digmaster system enabling precision working in deep water.
Land-based equipment assisting in the finishing work was varied. In the placement of antifers, 127-tonne Hitachi Zaxis 850s are used. These are equipped with specially-designed rotating grabs to pick up and position the heavy and large-dimensioned blocks, which could be up to 3.0 cu m.
“To the untrained eye, the placement of the antifers seems random, but, in fact, they are carefully placed to ensure their effectiveness in dispersing wave energy and to prevent back-scouring,” he points out.
Other Hitachi ZX850s are configured with long reach booms to give a 30 m reach. “These were modified by Abeko with a special float arrangement on the end of the stick to improve handling. This was essential to enable the necessary precision when placing large rocks and concrete blocks under the water. Apart from the GPS Prolec Digmaster, some of these excavators also feature a sonar radar system to provide the operator with underwater vision,” the spokesman explains.
All available equipment is being put to use in the final stages. Kobelco CKE 800 crawler cranes with an 80-tonne lifting capacity, work alongside 130-tonne Hitachi ZX870 excavators placing antifers as quickly as possible. These are delivered from a nearby stockpile, in a continuous flow, by Cat 988H and Cat 966H wheel loaders with front end handler.
Caterpillar articulated dumptrucks and rigid dumptrucks are being used to haul the final batches of armour rock from the quarry stone stock pile. Highway trucks bring the material into the site. Working the stockpile is a Komatsu PC 600 excavator as the primary loader.
Although centrally positioned, such is the scale of the project that the haul distances can be several kilometres in length. The travel distances, extreme heat, humidity and a dusty environment are very tough conditions for the machines, the operators and workers.
Key equipment in the Abeko fleet includes:
• Four 160-tonne Hitachi EX1200/5 with triple boom giving a reach of 24 m. The track frame on these has been extended and widened for extra stability;
• A 150-tonne Hitachi EX1100 with triple boom for a reach of 24 m;
• Four Hitachi ZX870/3 excavators with triple boom. These 130-tonne machines have a 22 m reach;
• Two Hitachi ZX870/3 Long Reach excavators, with an operating weight of 130 tonnes and a reach of 24 m;
• Five Hitachi ZX850 excavators with triple boom, an operating weight of 127 tonnes and 22 m reach;
• A 160-tonne Hitachi EX1200-5 Long Reach providing 30 m reach. This unit features a special float attachment on the stick to increase stability when work at full reach underwater;
• Two O&K RH25.5 excavators, 80-tonne, with triple booms giving an 18 m reach; and
• The Abeko Server 1, self-propelled, fully-automated, self sufficient jack-up barge.
These specially configured machines worked with a variety of Beco grabs and Krupp Hammers (up to and including the Krupp 7000 model).
Additional excavators and other equipment was brought in as required from the extensive Abeko fleet, which comprises more than 150 pieces of equipment, all selected specifically for marine and coastal engineering works.
Equipment available includes multi-purpose self-propelled spud barges; heavy-duty tracked excavators; wheeled excavators up to 75 tonnes; wheeled loaders up to 90 tonnes; multidockers; bulldozers; articulated dumptrucks and remote-controlled tracked loaders.
Almost all the machines have been extensively modified for the type of work they are required to do.
Service
With conditions being tough and deadlines tight, Abeko was charged with ensuring that the most appropriate equipment was available to the order of the Van Oord and the joint venture.
“It was essential, therefore, that the company ensured that the equipment was reliable, and that the operators had the necessary skills to work with the advanced technology used in placing the various materials,” says the spokesman. “The operating environment in Ras Laffan is not the best for plant and equipment. Servicing was, therefore, deemed a priority. As the machines were virtually on-call at all times, service scheduling was critical.”
Apart from fully-equipped service vehicles used by technicians skilled to work on a wide variety of machines, Abeko also built a fully-equipped workshop with 10 full-time engineers and two full-time site/workshop supervisors. This provided the essential 24-hour-day coverage, seven days a week. To minimise delay in servicing and repairing the equipment, Abeko had more than €1.5 million ($1.89 million) worth of spare parts on site at all times.
Logistic management
“Working on projects where specialised equipment is required takes many months of planning,” the spokesman continues. “From the earliest possible time (even pre-tender stage), Abeko works with contractors in devising the most cost-effective solution to ensure that not only is equipment sized and configured for the project but that it is delivered on time.
“As a global plant hire company, this can mean shipping equipment from different parts of the world as well as making any necessary modifications. Almost every piece of equipment has been extensively modified to meet the challenging work demanded from them. Typical modifications include wider, longer undercarriages on excavators for increased stability and additional counterweights to facilitate handling or large, heavy-rocks and precast elements.”
Dumptrucks typically have Hardox bodies and electrical circuits, giving additional protection from the harsh environment. Some components such as alternators are also upgraded.