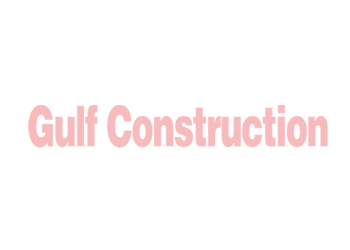
Although well known for its durability, concrete is subject to corrosion as a result of the onslaught of humidity and chloride-ion penetration, which not only have a destructive impact on the concrete itself, but also on the reinforcement steel used to improve the tension of the structure.
When rebar corrodes, the rust expands, cracking the concrete and unbonding the rebar from the concrete1.
The water in the pores of the cement is normally alkaline – and in such an environment steel is passive and does not corrode. However, the carbon dioxide from the air reacts with the alkali in the cement and makes the pore water more acidic. The acidity in combination with humidity leads to corrosion of the rebar – and the process is hastened by the presence of chloride ions.
Table 1
Bitumen coatings
All this destructive reactions require water. Hence, keeping the concrete dry is an important feature for concrete protection and maintenance. Water-repellent protection, which leaves the concrete surface breathable (vapour permeable) and reduces (or suppresses) the chloride ion penetration, is required.
Broadly used for that purpose are bitumen coatings. However, bitumen coatings are reported to have limited durability and after a while the corrosion process will start.
Water-based siloxane emulsion
Siloxanes and water-based siloxane emulsions however, have been considered as the latest solutions to contain corrosion. Tests conducted on the use of siloxane emulsions on roadwork applications such as tunnels and bridges by independent and authorised institutes in Germany2 and Sweden3, having proved their efficiency. Recent tests for US highway applications according to National Cooperative Highway Research Program Report 244-II have also confirmed the European test results4. The main subjects of the tests were water absorption, drying (vapour permeability) and chloride-ion absorption.
For this test the concrete formulation used was as follows:
• Type I Portland cement 439 parts
• Eau Claire sand 1,500 parts
• Eau Claire coarse aggregates 1,758 parts
• Water 225 parts
The impregnant Silblock WA, which is supplied as an emulsion with 60 per cent content of active ingredient, was diluted with water in a 1:3 ratio, which meant that the content of active ingredient of the applied material was 15 per cent. The application rate was 400 sq ft/gallon which is equal to approximately 5 sq m/litre.
The diluted Silblock WA was applied on to the concrete after a day of drying as well as after the fifth and the 21st day of drying (curing). After seven days of curing of the impregnant, the prepared specimen was exposed to an aqueous 15 per cent NaCl solution and the water intake was measured frequently for 21 days. Following this, the specimen was stored in dry conditions and the rate of water evaporation (drying) was also measured regularly for 21 days. Parallel to the drying, the intake of chloride ions after 21 days of exposure to the salt bath was analysed in comparison to an untreated reference. The results can be seen in Figure 1 and 2.
The high efficiency of Silblock WA as a protective impregnant for concrete could be proved decisively on comparing the results. In the treated block, water absorption is reduced by approximately 80 per cent and chloride intake by approximately 85 per cent compared to the untreated block during 21 days of exposure to the salty water bath, irrespective of what stage of the concrete drying the impregnant was applied. In addition, the breathability (vapour permeability) does not suffer.
Chart 2
Long-term durability
Having indicated that siloxane emulsions is a more modern solution, let us look at the durabilty of a siloxane impregnation.
Based on their use in hydrophobation of constructions or construction materials, silicones or silanes can be subdivided into three classes (Figure 3):
• Monomeric alkyl alkoxy silanes;
• Oligomeric alkyl alkoxy siloxanes; and
• Polymeric siloxanes (methyl silicone resins).
All three types produce a stable, three-dimensional, resin-like network once the concrete is cured. The chemical similarity of building materials to silicate components results in a stable and durable bonding of most mineral substrates. At the same time, the alkyl groups orient to the exterior (air) side and afford protection, similar to little umbrellas, against penetration of humidity (Figure 4).
Depending on the chemical structure (see Table 1), the mode of action or the site of attachment of the siloxanes must be distinguished. While polysiloxanes create a film particularly at the substrate surface, the low molecular-weight silanes and oligomeric siloxanes penetrate into the available pores - the low molecular products are subject to capillary absorption. Embedded in the pores and chemically reacting to the building material, they reduce the capillary absorption of water. Therefore, low molecular-weight silanes and oligomer silanes have nearly no influence upon the substrate surface, and the appearance of the building material remains visually unchanged. The polymeric siloxanes, on the other hand, form a surface film that leads to a visual change resulting in a dark, wet looking surface.
Chart 3
Silblock WA belongs to the second group - the oligomeric siloxanes, and is quite effective in penetrating the pores of the concrete and doesn’t change the surface appearance. Because of not remaining on the surface of the substrates, it is re-coatable and can be used as a primer for coatings and plaster. The strong chemical bond of the product leads to long-term durability. Figure 5 shows its performance after 7.5 years of exposure in Leverkusen, Germany in a heavy industrial climate. It can be seen that the water repellency did not suffer over the years – while the untreated specimen was eroded, with approximately 3 to 4 mm having been abraded by the time. The dirt pick-up and growth of algae on the untreated specimen are quite high, while the one treated with WA is still clean. The modern water-based material behaves even better than the solvent-based siloxane.
Summary
• Modern siloxane emulsions offer highly effective protection of concrete construction.
• In particular, the high durability, easier application and low volatile organic components content makes Silblock WA superior to traditional bitumen coatings.
References:
1. https://en.wikipedia.org/wiki/Reinforced_concrete
2. Polymerinstitut, Floersheim, Germany, Report no. P5277 / 02-183
3. SP, Swedish National Testing and Research Institute, Boras, Sweden, Report no. BTmP005229
4. CTL, Skokie, IL, US/Report no. 1064702 of Feb. 12th 2006
5. Kaesler, “German specialist keep water out”; published in Gulf Construction, Nov. 2005
Chart 4