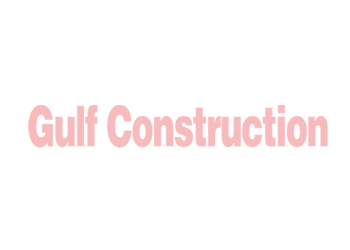
Damage to reinforced concrete caused by reinforcement corrosion can be greatly reduced or eliminated by the use of stainless steel reinforcement.
The main durability issue for reinforced concrete in aggressive environments, such as those of the coastal regions of the Gulf, is the ingress of chloride. The presence of chloride (ions) around reinforcement in the presence of moisture and oxygen may cause the corrosion of carbon steel.
As the rust formed occupies a greater volume than the original steel, the surrounding concrete is put under pressure and cracking or bursting can occur. The first defence is good quality concrete and sufficient depth of concrete to the steel (cover) to extend the time taken for chloride (ions) to penetrate and build up around the reinforcement.
There are several protective materials and systems to add protection to the concrete and reinforcement but the best way to prevent such damage is to use non-ferrous, non-corroding, materials such as fibre composite or stainless steel reinforcement. Fibre composite reinforcement is developing and has only been used in very specific and controlled research projects. Stainless steel is in use, it can be used in all structural elements and its availability and use is increasing.
So why, in view of its benefits, is it not more widely used? The answer seems to be that there is a lack of knowledge and some earlier concerns about its use. The most obvious concerns are cost, availability, its use in design and the possibility that if used in combination with carbon steel there may be bi-metallic corrosion.
Costs
Stainless steel costs more than carbon steel. At present, the cost difference ranges from six to eight times that of carbon steel. The real significance of this should be considered in terms of performance. There is a relationship between initial costs and performance (in life) costs.
A structure with the lowest initial cost can require high levels of maintenance and repair during its service life. So it can be more expensive in the medium or long term than a slightly more initially expensive structure with a reduced need for maintenance and repair operations.
There is much literature on such 'life cycle costing' and its potential for selecting the most cost-effective design. Using life cycle costing, the justification for the use of stainless steel is well-supported. Within a project, the extra civil engineering costs of replacing carbon steel with stainless steel may represent a small increase in total structural cost. In some structures with a large M & E content, such as offices, hotels and hospitals there is only a small increase in total project cost. And when savings in maintenance and repair costs are taken into account, there can then be an overall saving.
The full cost benefit can be even more attractive by using a combination of stainless steel in places where concrete is exposed to the most aggressive environment, say externally, and carbon steel in more protective areas or zones, say internally. In such a case, life cycle cost benefit even in the medium term will sweep away any concerns about any percentage increase in reinforcement costs.
As an example, a bridge over the River Rhine in Switzerland at Schaffhausen used a combination of stainless and carbon reinforcement following a life cycle cost benefit study. The use of the combination of steels only increased the initial project cost by 0.5 per cent. The cost study showed that using stainless steel in areas exposed to an aggressive chloride-bearing environment reduced repair, maintenance and disruption costs during the bridge's service life, giving an overall saving of some 13 per cent for an increase of only 0.5 per cent to the cheapest initial cost.
Electrochemical effects
Recent work has shown that for normal use and combinations, the risk of bi-metallic corrosion is small and is certainly less than when using a combination of carbon steels.
Types of stainless steel
Austenitic and duplex stainless steels are recommended for use as reinforcement.
Austenitic stainless steels:
- Have chromium and nickel as the main elements alloyed with the iron;
- Good general corrosion resistance;
- Strength characteristics improved by hot or cold working;
- Good toughness and ductility properties at low temperatures; and
- Low magnetic properties.
- Duplex stainless steels:
- Have high chromium and low nickel contents;
- Generally a corrosion resistance greater than that of most austenitic steels. In most cases in practical terms, it will not corrode;
- Is magnetic.
The various specification designations for the types of steel in use are given in the Table 1.
![]() |
Availability
Stainless steel can be supplied from Europe but as an important development for the Gulf, Acciaierie Valbruna of Italy, Europe's largest manufacturer of stainless steel reinforcement, is expanding its worldwide operations into the region, By the end of this year, Valbruna Gulf FZE will be operating from Jebel Ali Free Zone in Dubai.
The Acciaierie Valbruna trademark for stainless steel reinforcement is Reval and this has been used worldwide on numerous major projects. One of the most recent is the prestigious Guest Complex at Qsar Al-Alam, Muscat, where duplex stainless steel was used.
Design
Stainless steel reinforcement can be used in any situation where high yield steel bars are normally used. As they do not have a well-defined tensile yield point, for proof, strengths are determined as the stress at which plastic extension equals a specified strain. For stainless steels, this is usually at 0.2 per cent. For design, a statistical measure of strength is used - a characteristic strength, The characteristic strengths for austenitic and duplex stainless steels are shown in the table together with the old and newer steel designations'.
An engineer can either design to a characteristic strength of 450 N/sq mm - as for high yield steel reinforcement - or the actual characteristic strength shown in the table. The actual characteristic strength will give a more efficient use of the material.
Bond
Stainless steel ribbed bars meet a Type 2 bond classification in accordance with BS 6744. Minimum lap and anchorage lengths need to be selected to meet the needs of relevant national code. In most situations, the lapping of stainless steel bars with carbon steel presents no galvanic coupling problems.
Cover
The increased resistance to corrosion means that good-quality concrete cover to reinforcement can be reduced. In very aggressive environments, the minimum cover should still be at least 40 mm.
Reducing cover can allow the use of smaller diameter bars or reduction of a section's size. If sizes are reduced, there could be a saving in superstructure weight, reducing foundation loading.
A reduction of cover could also give better crack control in tension zones.
For precast sections made in factory conditions, the possibility of reducing cover should always be considered.
Way forward
A re-examination of the role of stainless steel reinforcement will result in its wider use in the Gulf, where the environment is aggressive to reinforced concrete, as its use, where appropriate, will lead to cost and structural performance benefits.