.jpg)
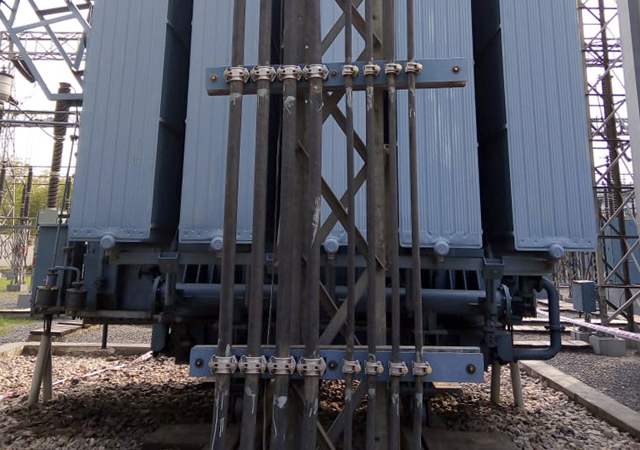
When you consider large construction projects in the Gulf states, it would be a fair assumption to say that currently, cable cleats wouldn’t feature particularly high on a list of products that people would name amongst the vital elements of the build.
However, the importance of cable cleats must not be underestimated. They are safety-critical products that need to be correctly specified in order to safely secure electrical cables not only during normal operating conditions, but also to ensure they are able to withstand extreme dynamic electromagnetic forces during a short circuit without sheath damage.
Effective cleating of cables, using a tested, proven product ensures the continuation of potentially vital electrical supplies and prevents cables leaping out of their containment systems during a short circuit, which would pose a very real threat to the building’s integrity and the lives of those in the vicinity of the affected installation.
![]() |
Lee Frizzell |
Put simply, for any electrical installation to be deemed safe, cables need to be protected and restrained by devices proven to withstand the forces the cables generate – especially during a short circuit – and this is exactly what cable cleats are designed and tested to do.
Without effective cable restraint, there’s risk of damage to expensive cables and cable management systems, and the previously mentioned threat that poorly restrained live cables pose.
So, what are the key things to consider when it comes to specifying cable cleats?
A question of trust
There are lots of cable cleats out there and it’s fair to say they can look very similar and claim to have very similar attributes. Therefore, it’s important to specify with confidence. You’d think twice about buying an expensive new phone from an unknown telecoms manufacturer - do the same with cable cleats. Look at the company behind the product; its technical expertise; the post-sales support it offers; where else have its cleats been used and are any of the installations similar? Cable cleats have a long lifespan and could be called upon to withstand a short circuit at any stage in their service life – so be certain you’re making the correct specification decision for the right reasons.
![]() |
CMP Products’ heavy-duty cable cleats. |
Testing, testing
Will the cable cleats you’re considering be up to the job? Some manufacturers will highlight the strength of their products based solely on a static mechanical tensile test. Unfortunately, this can be misleading as the forces applied in this type of test are applied in a slow and controlled manner, unlike in a short-circuit fault, where dynamic forces are applied almost instantaneously and oscillate in every direction.
A short circuit test really is the only reliable way of knowing a cable cleat is capable of withstanding a specific set of fault conditions and is essential in order for anyone, anywhere to specify with confidence.
Make space
It’s not just a question of getting the right cleats – they need to be correctly spaced to ensure they perform properly: Too close and you’ve over-specified; too far apart and they won’t be strong enough to match the performance outlined in the certified short circuit test.
A trustworthy manufacturer will advise on cleat spacing and demonstrate the force calculations conducted to reach this recommendation.
![]() |
CMP cable cleats securing HV cables. |
Corrosive issues
The risk of material corrosion also needs to be considered. Stainless steel is the material of choice for the vast majority of cable cleats and fixings due to its non-magnetic and excellent corrosion-resistant properties, with 316L being the most commonly used variant. Its corrosion resistance is the result of its chromium content, which reacts with oxygen and forms a self-healing impervious layer of chromium oxide on the surface of the steel.
Final considerations
The final three things to verify before specifying cable cleats are very much down to common sense:
• Fire safety: Make sure the cleats being specified have the same flame retardancy as the cable they’re securing;
• Operating temperatures: Most cable cleats are designed for use in ambient temperatures ranging from -60 deg C to +60 deg C and with cable conductor temperatures up to +90 deg C.
• Ultraviolet (UV) resistance: Metallic cable cleats are impervious to UV attack. Composite and polymer products aren’t. If they’re likely to be exposed, they should be supplied in materials containing carbon black or other UV stabilised additives.
Cable cleats may not currently be seen as the most vital element of an electrical installation, but their performance is paramount to their functionality, safety and the longevity. Therefore, it is important to specify with certainty and not be tempted to cut corners or costs.
* CMP Products (www.cmp-products.com) is the leading UK-based manufacturer of cable glands, cleats and accessories, which has an office in Dubai.