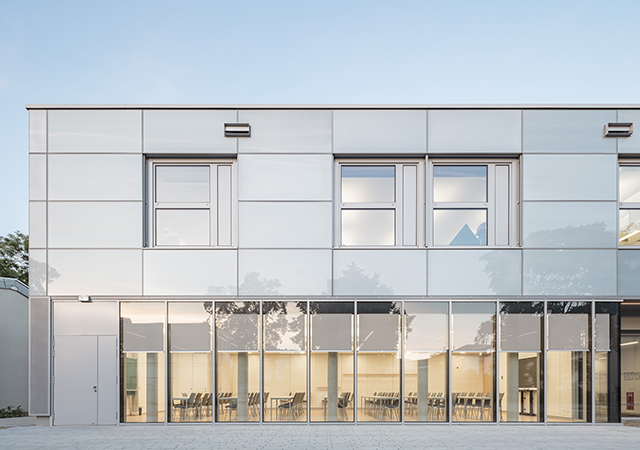
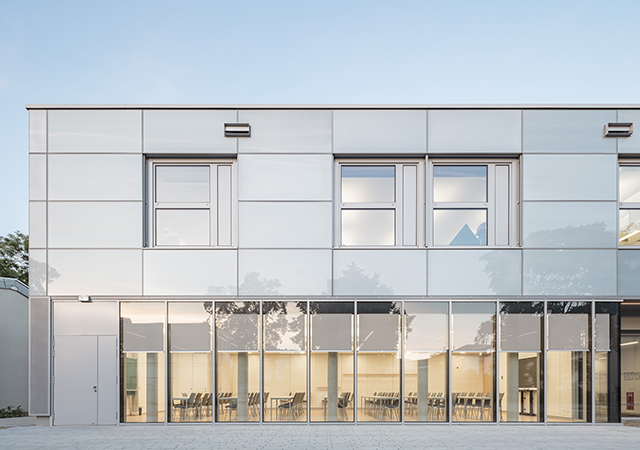
Façades of the future must fulfil various tasks: save energy, react to weather conditions and providing sound insulation; they must also be intelligent and predictive, says seele, a German technology leader in the design and construction of façades and complex building envelopes.
The company says it offers a solution that is ahead of its times with its ISOshade, which is claimed to fulfil all the requirements when it comes to specifications for high-performance, energy-efficient double-skin façades – including solar, thermal and sound insulation.
ISOshade is a closed double-skin façade with integrated sunblinds and a simple structure without external ventilation that offers an alternative to conventional closed cavity façades.
This high-performance façade with integrated sun shading fulfils all the requirements of an economical building envelope, says Michael Seele, Sales Director. “In addition to effective sound insulation, low heat loss and efficient sun and glare protection, ISOshade impresses with its particularly low energy consumption and thus makes an important contribution to the sustainability of building operation,” he says.
![]() |
ISOshade is a closed double-skin façade with integrated sunblinds. © seele |
“Maintenance of the external venetian blind or vertical awning is particularly straightforward: an inspection flap provides unhindered access to the sun shading system and integrated sensors control the maintenance intervals. The simple design of the façade element also makes it easier to maintain ISOshade,” he adds.
The façade impresses with its minimalist design and is easy to handle – similar to insulating glass, he points out.
ISOshade is a slim insulating glass unit consisting of triple insulating glass and a cavity with a factory-integrated solar shading system (external venetian blind or vertical awning). An external pane protects the sunblinds from dirt and the effects of the weather.
“An innovative technology is concealed in the closed cavity. A pressure equalisation system specially developed by seele regulates climate loads and reduces moisture ingress. This means that ISOshade requires no external ventilation, no compressors and no pipework. Energy is only used to control the sun shading system,” he points out.
The simple, self-sufficient ISOshade façade regulates pressure differences caused by temperature fluctuations in the space between the panes itself using a maintenance-free mechanism. In contrast to the complex closed cavity façade, ISOshade eliminates acquisition, installation and construction costs for compressors or pipework systems. This reduces the planning effort in advance and the energy costs during building operation.
![]() |
Butterfly House ... surrounded by two intertwining, curving free-form roof surfaces, covered in golden flowers. © Torsten Seidel |
ISOshade controls the heat and cold by synchronising the façade with the building automation. The sunblind in the cavity reacts actively to the weather data and acts with foresight. From the sensor technology in the space between the panes to the building control system and artificial intelligence, the smart façade element is an important building block for achieving “net zero” buildings.
ISOshade has already proven its efficiency in many projects, its latest project being a 2,700-sq-m façade in Munich, Germany. It has also been just installed at a building in in the German city of Leipzig.
Since its market launch, seele has continued to optimise ISOshade so that the façade element not only keeps up with the times, but is also ahead of them, he says.
“ISOshade is already a smart façade product that is connected to the building management system and can react automatically to environmental influences. We are already researching the next generation: in future, AI will link the data from the ISOshade sensors with other building automation systems. This will maximise the efficiency of building operation and predictive maintenance,” he concludes.
Seele, which was established in 1984, has two branch offices in the GCC, which offers ISOshade.
![]() |
The King Abdulaziz Center for World Culture ... a 30,260-sq-m stainless steel tube façade. © Diemo Schillack / seele |
The company creates high-quality façades and roof constructions for numerous prestigious building projects around the world. Among its most striking projects in the Gulf region are the King Abdulaziz Center for World Culture, also known as Ithra, in Saudi Arabia’s Eastern Province and Butterfly House in Sharjah.
The unique Ithra complex comprises five individual buildings with cultural facilities, including a library and a concert hall, that shine in the sun like bright “pebble stones”. The spectacular, three-dimensional freeforms soar up to 90 m high into the sky, and are clad with a futuristic façade of metal. The 30,260-sq-m stainless steel tube façade comprises 350 km of 3D-curved stainless steel tubes.
Seele’s scope of work included 28,600 sq m of standing seam façade, 2,170 sq m of insulated glass panels/glass fins at the Children Oasis, Administration Oasis and Great Hall Oasis; 1,700 sq m of twisted glulam columns/double glazed units at The Source; 150 sq m of vertical glass screens at the main and second entrance; a 50-sq-m post-and-rail grid structure at entrance façades; 37 sq m of keystone façade; 14 monosurface skylights (2.4 sq m each): elliptical and sloped flat glass skylights; 1,800-sq-m tower of window stripes; and a 90-sq-m tower skylight.
The artistic Butterfly House on Noor Island in Sharjah, depicts traditional designs of Islamic ornamentation. In this architectural gem, two intertwining, curving surfaces, covered in golden flowers, surround a glazed butterfly house and a café. Its roof of steel and aluminium composite panels appears light and delicate.
The curving free-form surface of the roof structure is bordered by 3D-curved circular hollow sections that are supported at nine points only and achieve a clear span of more than 20 m over the entrance zone. Between these peripheral members, a triangular lattice of welded steel sections allows plenty of daylight to reach the interior. A golden flower made from an aluminium composite panel decorates every node. This principle is reversed at the edge, where isolated petals are punched out of solid surfaces. The façade of this structure, which creates a unique atmosphere of light and shade in the building’s interior, comprises 3,375 steel sections, 4,060 petals made from aluminium composite panels; 325 sq m of 3D-curved peripheral aluminium composite panels; and 260 m of 3D-curved circular hollow sections.