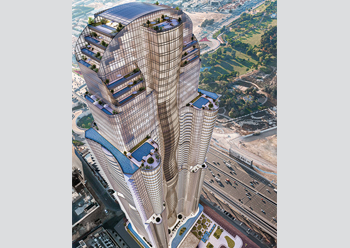
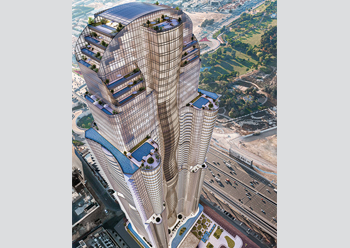
The Al Habtoor Group has appointed China Railway 18th Bureau Group as the main contractor for its newest landmark development, the Al Habtoor Tower, coming up in the heart of Dubai. It has also broken ground for the project, which is expected to be the largest residential building in the world with ultra-luxurious living facilities.
Strategically located on the banks of the Dubai Water Canal overlooking the Burj Khalifa, the 81-storey Al Habtoor Tower will comprise 1,701 keys over a built-up area of 3.5 million sq ft. The project, which is being built using innovative, creative, and selective construction techniques, is estimated to cost around AED3.7 billion ($1 billion) and is scheduled to be completed by mid-2026.
The new tower will be built at Al Habtoor City, home to Dubai’s most luxurious lifestyle destinations which was officially launched in 2016, with its three internationally branded hotels – The Habtoor Palace, LXR Hotels & Resorts, the V Hotel, Curio Collection by Hilton, and the Hilton Dubai Al Habtoor City – La Perle, a world-class theatrical experience in a specifically designed state-of-the-art aqua theatre, and three deluxe residential towers, Noora, Amna and Meera.
Announcing the contract award, Founding Chairman Khalaf Ahmad Al Habtoor said: “Knowing the complexity of taking on such a project, which requires a progressive and unique approach to construction, selecting the right contractors for the construction works was crucial, as our goal is to complete Al Habtoor Tower at the highest quality in record time.”
“China Railway 18th Bureau Group was selected based on a list of criteria, mainly for: Meeting the projected target for completion of 36 months: its full technical compliance for state-of-the-art quality, and successful track record in mega projects.”
On the non-conventional construction method, Al Habtoor said: “This is a project that has many challenging firsts, following a structural system used for the first time in Dubai and validated by a detailed engineering peer review from world-renown experts: Structural San Francisco, Imperial College London and Terrasol Paris. We are choosing to save the current structure instead of demolishing it and building afresh at a lower cost, which would have meant more than 3,000 trucks of wasted concrete and sand.”
“That is why we are using a top-down construction method whereby we have employed very heavy equipment from Bauer (the piling contractors), ranging from 60 to 100 tons each, to manoeuvre on top of the current building, reutilising, and reusing the existing structure,” he noted.
“Once completed, our carbon footprint will be less than half of any similar construction; building 1 sq m of equivalent projects is usually 1 ton of CO2, using our method, our CO2 footprint will be less than 0.5 ton per sq m. Environmental experts will follow the Al Habtoor Tower’s construction journey closely as we work towards achieving LEED (Leadership in Energy and Environmental Design) Platinum Certification,” he added.
Bauer is using a deep barrette foundation solution to enable the construction of the superstructure above an existing three-level deep basement.