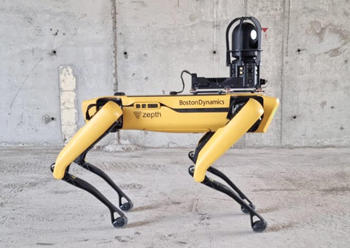
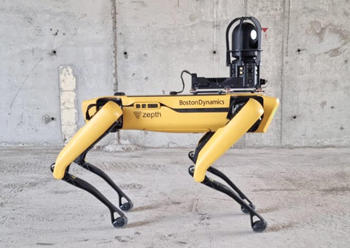
the world is changing faster than ever before, and the construction industry has to keep pace with the rising demand for modern residential, commercial, and industrial infrastructure projects.
Digital transformation in the construction sector of the Arabian Gulf had started to ramp up even before the pandemic, but has accelerated since then especially as completing projects on budget and on schedule becomes more challenging. Because of this, it’s vital that firms continue to adopt technology to remain competitive.
An increase in the utilisation of automation in the construction industry has created a perception that workers will eventually become displaced. However, robotic and automated processes have been implemented for centuries, and industries have always adapted – think of the Industrial Revolution, for example. The transition from hand-produced manufacturing to using machines positively affected modern civilisation as we know it. Additionally, artificial intelligence is not the same as human intelligence. Technology is far from achieving the perceptive abilities that define human creativity and innovation. These new technologies are born out of a desire to make our lives easier, not to create problems.
![]() |
Prasoon Shrivastava, Founder and CEO of Prasoon Design Studio |
Technology has the potential to greatly benefit the construction industry as it would improve efficiency and collaboration without compromising job security. Despite the size of the construction industry, it is still regarded as low-tech, though the Arabian Gulf has made impressive technological strides as of late. For example, the world’s first 3D-printed building was created in Dubai just a few years ago. And more and more firms in the region are using drones to map, survey and monitor construction sites. Even so, there are several misconceptions about robotics in the construction industry that remain:
• Myth #1: Automation will disrupt the construction workforce: As with many industries, the introduction of automated systems enhances the functions of the construction sector, and better manages human error. It does cause jobs to evolve, but it also generates greater demand for new talent. With automated construction management solutions taking the lead, everything from simulating projections or budgeting, to vendor and subcontractor coordination, material management, and revenue analysis, all happens as a unified back-end process. This creates a centralised hub of data and information, making it easy for project managers to leverage.
Even so, a large segment of skilled people in the construction industry has migrated during the pandemic, which will lead to an acute labour shortage once business returns to normal. The impact on the project management function will be quite evident as managers will have to struggle to get the right resources and complete projects on time. The best way to address the challenge is to offer incentives for long-time, skilled employees who are ready to stay and complete projects, and to implement reliable automated project management solutions.
Additionally, investing in intelligent technologies like AR/VR, drone mapping, and smart construction management platforms can effectively identify any risks well in advance and suggest steps for their mitigation. Having a reliable construction safety management software solution keeps projects on track by enabling the identification of the risks and paving the way for a quick resolution.
Robotics can also be used to evaluate sites where it may be unsafe for humans. Many engineering and construction firms are now investing in drones and robotics to streamline remote access and visual data capturing. Areas such as electrical, plumbing, equipment misuse and weak foundation points are being quickly identified through connected technologies for faster decision-making.
![]() |
Spot robot dog by Boston Dynamics ... Zepth recently announced its partnership with the US-based firm. |
• Myth #2: Implementing automated technology in construction is superfluous: Technology solutions allow for better tracking and monitoring of risk events. Risks in critical processes, such as inspections, labour safety, equipment, and material quality, can be instantly detected and remediated when using a synchronous technology solution.
It also enables construction firms to automatically set risk reporting and heat mapping measures within a centralised software solution. Through automation, developers can improve the productivity and efficiency of quality testing and analysis workflows while streamlining the process to eliminate bottlenecks. This reduces the burden on multiple stakeholders having to report individually on potential risk items during various execution stages. Managers can directly engage with the right parties via the project risk management solution and track mitigation plans during daily reporting.
• Myth #3: The transition to automated technology is too expensive: Though the Covid-19 pandemic is unprecedented, it made clear for all industries that they need to be future-ready. An investment in construction technology is the smartest move firms can make to keep business on track should another crisis occur.
Not only does technology future-proof a construction project, but it also helps manage the day-to-day activities. There is no doubt that even a single-day delay could result in a massive butterfly effect. In the current downturn, extra costs, missing resources, and delays are the last things that companies would want to face as they can translate into colossal ROI losses ahead.
In the planning process of a project, comprehensive budget preparation tools can be used by project managers to capture all cost items with greater detail. These solutions can map any budget changes, approvals, inputs and revisions, through their collaboration and workflow management tools.
There are risks of mismanaged variable costs, disconnect between site work and proposals, and chances of rework caused due to delays. As all construction work is connected to a cost factor for every project, it is important to have a reliable solution onboarded to lower the risk of capital mismanagement.
Having a reliable automated technology solution in place has massive downstream financial benefits for a construction project. In fact, according to Boston Consulting Group1, the digitalisation of non-residential construction is expected to result in worldwide annual cost savings of 10 to 21 per cent across diverse stages of a project.
Effective communication, analytics, monitoring and reporting are crucial aspects for completing and delivering the project efficiently and on-time. Construction projects are widely known to experience delays of around two to three years for large-scale projects, owing to complexities arising from lack of reach and management. Digital transformation and automated technology can change this.
The enhanced productivity gained from digitising various processes allows companies to improve project outcomes significantly. Having access to automation tools, standardised workflows, data management systems and chat solutions means better efficiency, a better experience and a better final product.
1. https://www.bcg.com/publications/2016/engineered-products-infrastructure-digital-transformative-power-building-information-modeling