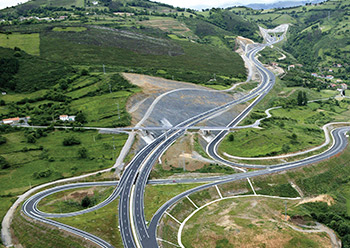
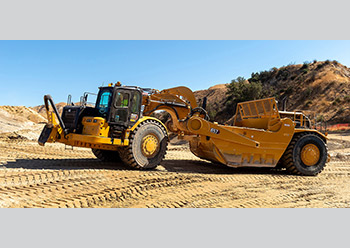
Caterpillar has launched a new wheel tractor-scraper (WTS) which is claimed to be the next generation of ultra-class material moving equipment, offering greater productivity, efficiency and operator comfort while incorporating a range of advanced operating features.
Featuring the field-proven, twin-power design to boost cycle times, the new Cat 657 WTS elevates productivity and operating efficiency to deliver low-cost earthmoving. A seven per cent increase in fuel efficiency over its preceding model, the 657G WTS, means more material moved per unit of fuel burned, and improved onboard payload estimating accuracy helps optimise productivity, says a spokesman for the construction equipment major.
The Cat 657, the largest open-bowl scraper in the Caterpillar line with a rated load of 46.4 tonnes, now has a more spacious cab to boost operator comfort and efficiency in high volume earthmoving, highway construction and mining applications.
![]() |
The new WTS has a rated load of 46.4 tonnes. |
“This new 657 is the next generation of ultra-class material moving systems,” says John Gerhold, wheel tractor-scraper application specialist for Caterpillar. “It delivers improved productivity, safety and technology, which our customers can use to strengthen their business today – and it is equipped to grow with them to meet tomorrow’s requirements.”
The 657 features on-the-go weighing through Payload Estimator, allowing the new WTS to achieve 95 per cent load accuracy, so operators more easily reach target load goals, he says. “When working in colder climates, the unique Auto-Stall feature quickly brings the transmission to operating temperature at start-up, so the 657 gets to work faster. Ground Speed Control lowers fuel consumption by allowing the operator to set the desired top speed, allowing the machine to find the gear that works best for the engine and transmission,” Gerhold adds.
The two-engine design includes the Cat C18 powering the tractor and Cat C15 in the scraper, both meeting stringent US EPA Tier 4 Final/EU Stage V emissions standards. “Its Advanced Productivity Electronic Control System (APECS) allows the machine to better utilise engine power and torque, resulting in more material moved throughout the shift. The transmission features Electronic Clutch Pressure Control, which improves shift quality and fuel efficiency. New hydraulic disc brakes improve braking performance and reduce maintenance,” he states.
Comfortable operation
Detailing the features of the cab, Gerhold says: “A 21 per cent larger cab interior than the 657G improves operator comfort and provides excellent visibility to the bail, cutting edge and bowl of the new 657. The air suspension comfort seat adjusts and rotates 30 degrees to reduce fatigue, while the new Advance Ride Management adjusts damping to match ground conditions, resulting in a smoother ride for the operator. Automatic HVAC (heating, ventilation and air-conditioning) temperature control and defroster come standard for increased operator comfort. The new power access ladder enhances operator safety when entering and exiting the cab.”
The new high-pressure steering system requires less steering input, which bolsters operator efficiency and productivity. Automatically engaging when the machine is in eighth gear, engine overspeed protection assists in slowing machine speed when approaching engine limits. Sequence Assist, a new option on the 657, automates many operator inputs each cycle to simplify machine operation.
Increased efficiency
The 657 tractor includes a new hydraulic on-demand fan that increases engine fuel efficiency. The machine also has draft-arm overflow guards, which prevent material accumulation between the draft arms and bowl sides. Ground-level access for fuel fill and all daily maintenance points increase service efficiency and safety to increase machine uptime.
Integrated Payload Estimator and Cat Product Link technologies provide real-time payload, machine location, fuel usage and idle time information as well as diagnostic fault codes – all to significantly increase fleet management efficiency, he points out.