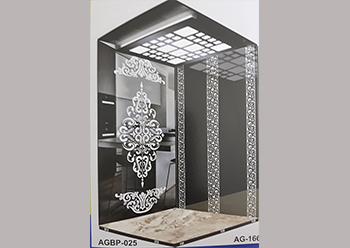
.jpg)
Tunisia’s Sebri group subsidiary Somevam turned to solutions from wet processing equipment specialist CDE when it wanted to diversify into the glass industry and ensure that its sand offering was unique in the region.
Somevam has been operating sand quarries in Oueslatia, Tunisia, serving the country’s construction market since 2001. Following testing of material, the company saw the opportunity to diversify into the glass industry in North Africa and Europe and produce a range of supplementary products, including industrial sand and silica flour. The company also wanted to produce a 30- to 150-micron fraction that would make its offer unique in the region.
Somevam extracts 3,000 tonnes per day (tpd) of sand. In order to handle such quantities efficiently while also adhering to stringent quality standards requires the most advanced, durable and sustainable processing equipment.
![]() |
Somevam’s quarries produce a variety of sand fractions. |
Together, Somevam and Northern Ireland-headquartered CDE have developed a tailor-made wet processing solution to support the Tunisian company in achieveing its commercial growth aspirations.
The Somevam plant was delivered and commissioned by the CDE MEA (Middle East and Africa) team based out of Dubai. The design process, underpinned by CDE’s co-creation approach, allowed the company’s engineers to work directly with the Somevam team to develop a modular wet processing installation perfectly suited to the feed material and the company’s production targets.
Habib Sebri, CEO of Somevam, explains: “Before we got into glass sand, we operated the Oueslatia site for the production of building materials. However, it was clear that the material on site presented an interesting commercial opportunity in the field of silica for flat glass applications such as windows, mirrors and flat glazing.”
Sebri says it was important to invest in the right sand treatment equipment to guarantee the success of the project.
“After exhaustive research of the various options at our disposal, we chose a modular wet processing solution from CDE. The expertise of the company’s engineers and sales team, its investment in innovation and new technologies, and the quality of the materials used during the manufacturing process were the key determining factors in our decision.”
![]() |
The M4500 demonstrates the effectiveness of CDE’s cyclone technology. |
CDE solution
To guarantee precise control of sand cut points, Somevam opted for a complete turnkey CDE solution. The CDE plant has the capacity to treat up to 200 tonnes per hour (tph) of sand, producing 100 tph of silica glass sand for the glass industry, as well as a range of secondary products including fine silica sand for silica flour production, foundry sand, concrete sand and road base.
The installation features a combination of CDE equipment operating in perfect synergy: an M4500 primary wash plant to classify materials, five high-frequency Infinity screens, four attrition cells, spiral separators, CDE’s Counter Flow Classification Unit (CFCU), a nano-cyclone, magnet, four EvoWash sand washing units and an AquaCycle water management solution.
Combined, the system processes fine and coarse materials and eliminates contaminants to produce high-specification glass sand.
Bassem Idriss, Project Manager for the Europe and Mena (Middle East and North Africa) region at CDE, explains: “The M4500 demonstrates the effectiveness of CDE’s cyclone technology and the flexibility of our process and engineering teams, who have designed the process to produce very high-quality glass sand to meet Somevam’s requirements.
“The hydrocyclones were built according to the specific needs of the client, based on analysis of the feed material carried out by CDE during the pre-project phase.
“The process water, loaded with undesirable fines, is removed at the level of the overflow of the cyclones while the treated sand enters the dewatering and stockpiling phase. With cutting points of incomparable precision, the products are treated according to the required standards and without risk of mixing.”
![]() |
CDE’s equipment at Somevam’s quarries helped achieve the quality of sand required. |
Efficient water management
The new installation incorporates CDE’s cutting-edge water management system, the AquaCycle thickener with a capacity of 1,500 cu m per hour. Waste water from the plant is processed by the AquaCycle thickener which recovers up to 90 per cent of the process water to be recirculated back into the washing plant.
Idriss continues: “In Tunisia, a hot and dry country, it is important to consider the difficulties of accessing fresh water. It is essential not to waste a drop of water. CDE’s AquaCycle allows Somevam to recycle process water in a closed circuit for immediate reuse in the system.
“The wastewater, after passing through the deaeration chamber and after having been in contact with the flocculant injection, passes to the centre of the AquaCycle so that the flocculation process operates and acts on the sedimentation of the fines. The integrated flocculation unit allows precise dosing of premixed flocculant for effective decantation. A single motor drives the AquaCycle rake arms for optimal sludge treatment before disposal.”
The result
The CDE installation for Somevam transforms the feed material into five high-specification products with exceptional commercial value. It produces glass sand (150-650 microns) and related products, including oversized (3 mm), ready to be used in water filtration systems, coarse sand (650 microns-3 mm) ready to be ground to make flour silica, ultrafine (30-150 microns) for ceramics or other industries, and iron-rich sand that can be used in sports fields. With a typical moisture content of 12 per cent, the materials are market-ready straight from the belts.
Sebri comments: “Our CDE solution has made a huge impact on the glass sand industry in Tunisia and in the North African market. It represents the most advanced technology available in the North African market and has enabled us to become ultra-competitive in an industry with extremely high-quality standards.
“Our glass sand is sold for the production of white glass, and the other fractions are sold for various industrial applications. Our quick return on investment was thanks to the power and efficiency of our CDE solution.
“We have succeeded in expanding our offer and positioning ourselves in new markets, which has strengthened Somevam’s reputation with its customers for quality and consistency of service.”
CDE MEA’s (Middle East and Africa) expert engineers and CustomCare team, based out of Dubai, continue to provide industry-leading after-sales support to maximise the efficiency and uptime of the Somevam plant through responsive on-the-ground support, replacement parts and maintenance.
A natural focus for business development, the MEA team has expanded to meet the growing demand for its wet processing technologies throughout the Middle East, Africa, and in the Gulf region which has grown significantly over the past decade.
Today, CDE has over 75 wet processing plants successfully utilising its water management and recycling technologies in the MEA region.