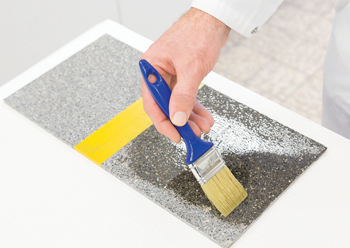
Wacker, the globally renowned chemical company, offers an innovative solvent-free binder that can be used for impregnating cementitious flooring to ensure excellent stain protection and consolidate and optically enhance the floor surface.
Silres BS 6920, which was unveiled at the European Coating Show 2017, has received good response from the Middle East region, according to Mayur Upadhyay, Wacker sales manager for MEA region.
Based on alpha-silane technology, Silres BS 6920 is a highly-effective alternative to water glasses or silanes. Its stain-protection effect, in particular, makes it superior to other binders. It shows its strengths particularly where the flooring is subject to considerable loading from soiling agents or foot and wheel traffic, and is still required to permanently maintain an attractive appearance, says a company spokesman.
![]() |
A cement-bound test plate ... the left half is untreated, while the right half was impregnated with Silres BS 6920. The drop at the left soaks into the construction material and leaves behind stains that are difficult to remove. |
According to him, property developers and planners have been increasingly turning to concrete or cement-screed floors that can be used directly – without the application of tiles, wood-block flooring, linoleum or other coverings. These surfaces are ground and polished to meet high aesthetic standards.
“Cement-bound designer floors can be found today in many fashion stores, exhibition and sales rooms, shopping malls, bistros, galleries and museums. They are also very popular for living rooms in homes,” he adds.
However, while these floors are sturdy and durable by nature, if left untreated, they are prone to dirt pick-up, are difficult to maintain and wear quickly.
“To protect them, they are usually impregnated. However, the impregnation agents that are generally available often prove ineffective in practice. Many of the liquids that fall onto floors produce stains despite the treatment,” he says.
But this can be remedied with Silres BS 6920, which enables the production of highly-effective one-component impregnating agents, offering excellent stain protection and consolidating the floor surface.
![]() |
Stain test showing the effectiveness of Silres BS 6920 protection: three concrete plates impregnated with silicate (left), silane (centre) and Silres BS 6920 (right) were wetted with red wine, cola, coffee, mustard, ketchup and other staining substances. |
Elaborating further, the spokesman says untreated concrete and cement-bound floor screeds have a porous surface. This allows liquids such as engine oil, plasticisers (from car tyres), edible oils, spilt drinks, ketchup or other foods to soak into the pores. The porosity also reduces the floor’s mechanical strength.
Another aspect of cementitious surfaces is that they are not very wear resistant – a problem not only for homes, but also for warehouses and sales rooms. As such, it becomes necessary to protect these surfaces against soiling and abrasion before they can be used.
The method used will depend on the type of loading to be expected and the aesthetic requirements. If there is no likelihood of contact with aggressive chemicals, then the developer will usually choose impregnation.
According to the EN 1504-2 standard, concrete impregnation is a treatment that partially or entirely fills the surface pores. Depending on the absorbency of the concrete and how much preparation is used for the treatment, a thin film also forms on the concrete surface.
Impregnating agents using different technologies have been developed for treating cementitious flooring. Amongst those widely used are waterborne silicate impregnating agents known as waterglass systems and solvent-based silane impregnating agents.
However, both of these technologies are severely challenged by many common soiling materials, as has been reported by customers from the construction industry and as shown by Wacker’s own tests. In lab tests, coffee, red wine, cola or mustard left persistent stains on impregnated test plates after 24 hours of contact.
Silres BS 6920 belongs to the group of alpha-silane-terminated polyethers, which have attracted increasing attention in the adhesive and sealant industry in recent years. As with all silane-terminated polyethers, the Silres BS 6920 undergoes silane crosslinking, forming a siloxane network as soon as it is exposed to moisture.
Sufficiently rapid curing is achieved in the presence of an aminosilane catalyst.
Wacker developers have custom-designed the new polymer for use in impregnating agents for cementitious flooring. The key parameters were the chemical structure of the silane building blocks and the lengths of the polyether chains.
For example, the silane building blocks were modified so that Silres BS 6920 cures to form a particularly close-meshed network of quartz-like structural units. Thanks to the optimisation, the new binder has a low viscosity which penetrates deep into the pores of the cementitious substrate, filling them more or less completely before curing to form a hard material.
The chemical structure of the new binder makes the treated surface of the flooring both water- and oil-repellent.
Since the crosslinked Silres BS 6920, with its quartz-like structure, mechanically reinforces the substrate, the treated floor becomes abrasion resistant and can withstand heavy pedestrian traffic, or can even be driven on by forklift trucks, cars or heavy-duty vehicles.
In terms of safety, Silres BS 6920 is solvent free and classified as nonhazardous. Its flash point is over 100 deg C, thus reducing any fire risk.
Because of its low viscosity, Silres BS 6920 can also be processed without using solvents. However, processors can also add solvents if needed. Likewise, quartz flour, pigments or other solids can be added to adjust the mechanical and optical properties of the end product within wide limits.
Easy to use
Impregnating agents made from Silres BS 6920 are very easy to use: they can be applied to the relevant floor using a mop, a short-hair roller or an airless spray gun. After 24 hours, curing is largely completed, and the floor can be walked on or treated by other means. If the substrate is highly porous (therefore, very absorbent), two coats may be necessary to achieve the best results.
If an impregnating agent is applied to an absorbent substrate, the first coat mainly fills the pores and consolidates the floor. Most of the agent soaks into the substrate and the surface looks quite inhomogeneous. Only the second coat results in a homogeneous, polishable, glossy surface. The resulting film reduces the surface roughness considerably and produces a uniform, high-gloss surface.
Results
Excellent stain protection, colour intensification and mechanical consolidation are the three main features resulting from impregnation with Silres BS 6920.
The spokesman says the colour intensifying effect is very pronounced. “If a cement-bound floor is treated with a transparent formulation of Silres BS 6920, the surface appears darker and the colours look more intense. On polished flooring, the aggregate stones are more prominent.
“These optical effects are desirable to many property developers. They emphasise the high-quality appearance of the designer floor. The consolidating effect improves the scratch and scrub resistance,” he adds.
However, the key benefit of the Silres BS 6920, he says, is dirt resistance. Wacker’s engineers compared it to commercially available silicate- and silane-based impregnating agents.
“Twenty substances were tested. They were wiped off first with dry and then with wet kitchen towels after 24 hours. In the case of the silicate impregnation, 14 of the 20 test substances left stains.
“In the case of the silane impregnation, it was seven; and in the case of Silres BS 6920, only three. These results (see above) show that the product offers significantly more protection against soiling agents than the agents based on conventional technologies,” he remarks.
According to Upadhyay, Wacker customers in the Middle East and Africa have been successfully using hybrid flooring solutions as a protective floor coating of warehouses, parking lots, stamped concrete, terrazzo, etc.
He says Silres BS6920 is a one-component and fast-curing solution, which enhances the ease of application thus saving time and energy of the applicator.
“We have received great response for this product in the region so far. BS6920 can be formulated for both interior and exterior applications and is also being used as a binder for decorative stone carpets,” he adds.
“Benefits such as one-component formulation, ease of repair, excellent stain and scratch resistance, solvent-free and enhanced breathability of the coating differentiates our product compared to traditional applications used in the industry at present,” he concludes.
The Wacker Group’s activities in the Middle East date back to the 1980s. To boost regional sales activities particularly for polymer products, Wacker Chemie Dubai was founded in 1999. And in 2000, the first liaison office in Dubai opened to more closely support the Gulf region. Two years later, Wacker Chemicals Middle East was founded as a 100 per cent subsidiary. Today, Wacker Chemicals Middle East in Dubai serves the Arabian Peninsula, the African continent, and in the East Gulf countries.