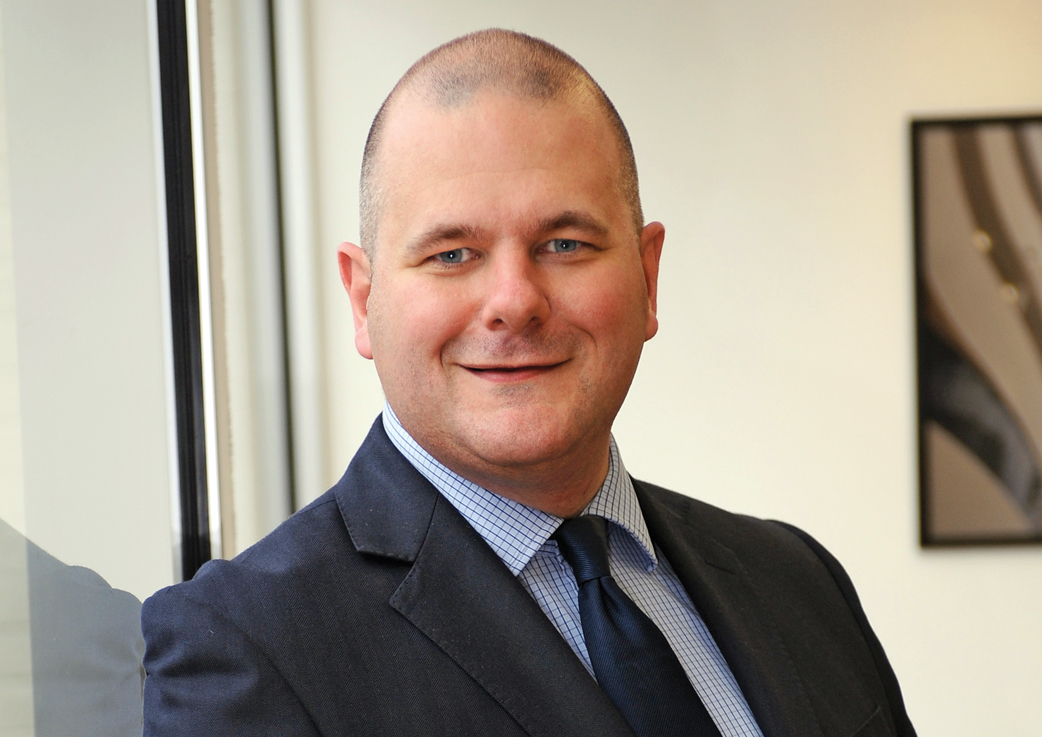
Thre is no doubt that BIM (building information modelling) brings with it a number of advantages and benefits, from cost savings and faster project delivery to lower emissions and elimination of waste.
In Europe, the EU Public Procurement Directive, published in 2014, recommends the use of electronic tools such as BIM for public works contracts and design contests.
In the UK, BIM was being used for publicly funded building projects, and the UK government requires BIM Level 2 to be used on all public sector projects by 2016 after estimating that it helped save taxpayers some £800 million ($1.6 billion) in construction costs in 2013-2014.
BIM is being used in the Middle East as well. Dubai Municipality mandated the use of BIM for buildings over 40 storeys or more than 300,000 sq ft, as well as for government projects including hospitals, universities and schools. It is now also used across several complex and large-scale infrastructure developments, roadways and railway projects. For example, it is playing a vital role in the development of Abu Dhabi International Airport’s new $2.94-billion terminal, which will cover an area of 630,000 sq m and serve up to 20 million passengers per year. Riyadh’s light rail system is another case in point.
In order to fulfil the requirements in a region where the construction industry is booming, while preparing for global events such as the Expo 2020 in Dubai or the 2022 Fifa World Cup in Qatar, a rapid transition to BIM will be necessary to meet the specified project demands. However, as much as we are talking about an electronic tool, BIM adoption requires more than just a compatible software; it requires changing expectations, roles and responsibilities – and here is where the potential pitfalls might lie.
The people factor – the collaboration and communication between clients, architects, contractors and manufacturers – is crucial.
The product manufacturer’s data is the key driver to the overall success of BIM and is directly dependent on the quality of the input. Unfortunately, there seems to be a discrepancy between users about how BIM is used and what information is required; some may need fully detailed 3D models with COBie (Construction Operations Building Information Exchange) data, some would request COBie data only, some have content size restrictions while others want it all. The COBie spreadsheet should contain relevant information for the specific product or system – too little or unusable data could potentially be disadvantageous in the specification process. What should then be included without causing information overload?
When BIM objects get updated, it is of utmost importance that all copies of these objects are updated – whether hosted on the manufacturer’s own website or a third-party website; manufacturers need to put procedures in place that will guarantee accuracy of the data presented. Accurate data is the key to success.
BIM is digitising the supply chain and the whole construction process, bringing together all the parties that design, construct and operate a facility. It is a real force for collaboration but it requires the entire team to be on board – when architects and designers develop a project in BIM, the contractors need to be able to work within that frame. This then requires their supply chain to invest in BIM. Can the building and construction industry break down the silos?
The collaboration should not end once the project is finished; property developers need to make sure that facility managers understand how the completed building is operating and using energy in order to make further decisions as well as savings. BIM can be used to design the most efficient building, but if the staff/tenants are not operating and managing it properly, then many of those innovative features will not be performing as they were intended to.
BIM users
While everyone seems to understand what BIM as a software tool does, the collaboration part of the process tends to be omitted. Experienced architects, engineers, contractors and product manufacturers need to communicate long before design work starts on a building; discuss more cost-efficient options that would perform and help achieve certain environmental ratings, and whether a certain product is appropriate in the first place.
Even though a virtual mock-up is cost efficient in comparison to a physical one, a physical mock-up may still be required if a product needs to go through a series of physical tests. Although architects and designers are using BIM to construct a building, they will often request a physical mock-up so they can visualise, better understand and make decisions about the aesthetics and the functionality of part of the project.
BIM specialist
One of the issues many regions face is the lack of clarity of BIM standards, guidance or regulations to ensure the most productive use of the system.
Furthermore, qualified BIM specialists are often rare; in-house training is still seen as a costly investment and expertise is provided by international architecture and design companies rather than regional and local practices.
BIM training and education needs to be implemented in order to create expertise in the region – this is not just from the technology point of view, but also from the co-operation and collaboration perspective – everyone in the company should understand what their responsibilities are when it comes to BIM.
* SAS International is a UK-based interior fit-out products provider.