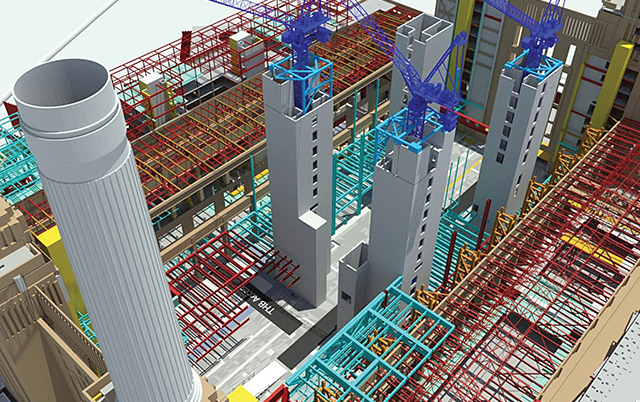
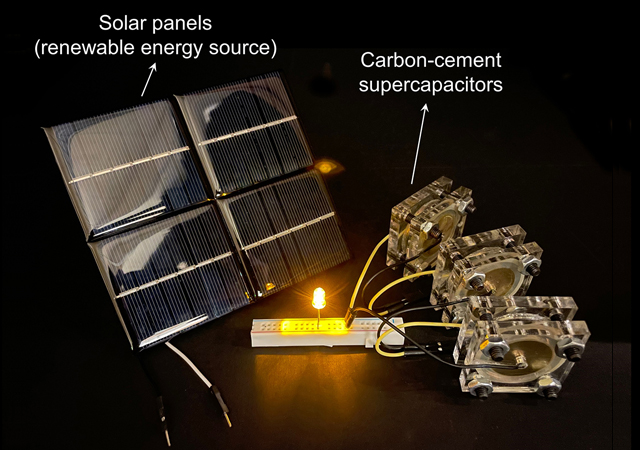
Two of the most ubiquitous historical materials, cement and carbon black (which resembles very fine charcoal), may form the basis for a novel, low-cost energy storage system, according to a recent study at Massachusetts Institute of Technology (MIT). The technology could facilitate the use of renewable energy sources such as solar, wind, and tidal power by allowing energy networks to remain stable despite fluctuations in renewable energy supply.
The two materials, the researchers found, can be combined with water to make a supercapacitor – an alternative to batteries – that could provide storage of electrical energy. As an example, the MIT researchers who developed the system say that their supercapacitor could eventually be incorporated into the concrete foundation of a house, where it could store a full day’s worth of energy while adding little (or no) cost to the foundation and still providing the needed structural strength. The researchers also envision a concrete roadway that could provide contactless recharging for electric cars as they travel over that road.
The simple but innovative technology is described in a paper by MIT professors Franz-Josef Ulm, Admir Masic, and Yang-Shao Horn, and four others at MIT and at the Wyss Institute for Biologically Inspired Engineering.
Capacitors are, in principle, very simple devices, consisting of two electrically conductive plates immersed in an electrolyte and separated by a membrane. The amount of power a capacitor can store depends on the total surface area of its conductive plates.
The key to the new supercapacitors developed by this team comes from a method of producing a cement-based material with an extremely high internal surface area due to a dense, interconnected network of conductive material within its bulk volume. The researchers achieved this by introducing carbon black – which is highly conductive – into a concrete mixture along with cement powder and water, and letting it cure. The water naturally forms a branching network of openings within the structure as it reacts with cement, and the carbon migrates into these spaces to make wire-like structures within the hardened cement. These structures have a fractal-like structure, with larger branches sprouting smaller branches, and those sprouting even smaller branchlets, and so on, ending up with an extremely large surface area within the confines of a relatively small volume. The material is then soaked in a standard electrolyte material, such as potassium chloride, a kind of salt, which provides the charged particles that accumulate on the carbon structures. Two electrodes made of this material, separated by a thin space or an insulating layer, form a very powerful supercapacitor, the researchers found.
The two plates of the capacitor function just like the two poles of a rechargeable battery of equivalent voltage: When connected to a source of electricity, as with a battery, energy gets stored in the plates, and then when connected to a load, the electrical current flows back out to provide power.
“The material is fascinating,” Masic says, “because you have the most-used manmade material in the world, cement, that is combined with carbon black, that is a well-known historical material – the Dead Sea Scrolls were written with it. You have these at least two-millennia-old materials that when you combine them in a specific manner you come up with a conductive nanocomposite, and that’s when things get really interesting.”
As the mixture sets and cures, he says, “The water is systematically consumed through cement hydration reactions, and this hydration fundamentally affects nanoparticles of carbon because they are hydrophobic (water repelling).”
As the mixture evolves, “the carbon black is self-assembling into a connected conductive wire,” he says. The process is easily reproducible, with materials that are inexpensive and readily available anywhere in the world. And the amount of carbon needed is very small – as little as three per cent by volume of the mix – to achieve a percolated carbon network, Masic says.
Supercapacitors made of this material have great potential to aid in the world’s transition to renewable energy, Ulm says. The principal sources of emissions-free energy, wind, solar, and tidal power, all produce their output at variable times that often do not correspond to the peaks in electricity usage, so ways of storing that power are essential.
“There is a huge need for big energy storage,” he says, and existing batteries are too expensive and mostly rely on materials such as lithium, whose supply is limited, so cheaper alternatives are badly needed. “That’s where our technology is extremely promising, because cement is ubiquitous,” Ulm says.
The team calculated that a block of nanocarbon-black-doped concrete that is 45 cu m in size – equivalent to a cube about 3.5 m across – would have enough capacity to store about 10 kilowatt-hours of energy, which is considered the average daily electricity usage for a household. Since the concrete would retain its strength, a house with a foundation made of this material could store a day’s worth of energy produced by solar panels or windmills and allow it to be used whenever it’s needed. And, supercapacitors can be charged and discharged much more rapidly than batteries.
After a series of tests used to determine the most effective ratios of cement, carbon black, and water, the team demonstrated the process by making small supercapacitors, about the size of some button-cell batteries, that could each be charged to 1 volt, comparable to a 1-volt battery. They then connected three of these to demonstrate their ability to light up a 3-volt light-emitting diode (LED). Having proved the principle, they now plan to build a series of larger versions, starting with ones about the size of a typical 12-volt car battery, then working up to a 45-cu-m version to demonstrate its ability to store a house-worth of power.
There is a tradeoff between the storage capacity of the material and its structural strength, they found. By adding more carbon black, the resulting supercapacitor can store more energy, but the concrete is slightly weaker, and this could be useful for applications where the concrete is not playing a structural role or where the full strength-potential of concrete is not required. For applications such as a foundation, or structural elements of the base of a wind turbine, the “sweet spot” is around 10 per cent carbon black in the mix, they found.
Another potential application for carbon-cement supercapacitors is for building concrete roadways that could store energy produced by solar panels alongside the road and then deliver that energy to electric vehicles travelling along the road using the same kind of technology used for wirelessly rechargeable phones. A related type of car-recharging system is already being developed by companies in Germany and the Netherlands, but using standard batteries for storage.
Initial uses of the technology might be for isolated homes or buildings or shelters far from grid power, which could be powered by solar panels attached to the cement supercapacitors, the researchers say.
Ulm says that the system is very scalable, as the energy-storage capacity is a direct function of the volume of the electrodes. “You can go from 1-mm-thick electrodes to 1-mm-thick electrodes, and by doing so basically you can scale the energy storage capacity from lighting an LED for a few seconds, to powering a whole house,” he says.
Depending on the properties desired for a given application, the system could be tuned by adjusting the mixture. For a vehicle-charging road, very fast charging and discharging rates would be needed, while for powering a home “you have the whole day to charge it up,” so slower-charging material could be used, Ulm says.
“So, it’s really a multifunctional material,” he adds. Besides its ability to store energy in the form of supercapacitors, the same kind of concrete mixture can be used as a heating system, by simply applying electricity to the carbon-laced concrete.
Ulm sees this as “a new way of looking toward the future of concrete as part of the energy transition.”
The research team also included postdocs Nicolas Chanut and Damian Stefaniuk at MIT’s Department of Civil and Environmental Engineering, James Weaver at the Wyss Institute, and Yunguang Zhu in MIT’s Department of Mechanical Engineering. The work was supported by the MIT Concrete Sustainability Hub, with sponsorship by the Concrete Advancement Foundation.