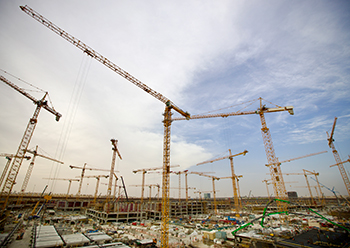
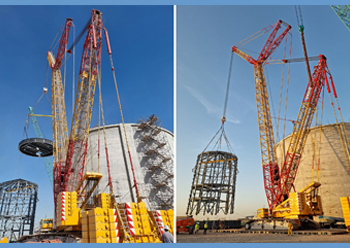
A fleet of Liebherr mobile cranes and Demag, Kobelco and IHI crawler cranes was recently deployed by UAE-based Al Faris Group – a leading provider of safe and innovative solutions for heavy lifting and transport in the region – to complete a challenging lifting operation for a penthouse structure on a clinker silo in Fujairah.
The scope of the project for JSW Cement’s facility involved erection of steel structures such as the ring beam, rafter frames, penthouse, and conveyor galleries on the clinker silo.
The cranes comprised Liebherr mobile cranes – 110-tonne, 250-tonne and 450-tonne models – as well as Demag’s 650-tonne, Kobelco’s 250-tonne and IHI’s 250-tonne crawler cranes.
Demag’s 650-tonne crawler crane was rigged up and lifted the 70-tonne ring beam assembly above the silo. Stay cables were used to secure the ring beam at 44 m. Then two 250-tonne cranes were used to connect the rafter assembly (25 tonnes each). Once the rafters had been assembled, the silo’s load was gradually released.
The entire penthouse set, weighing 150 tonnes and measuring 15 m x 15 m x 22 m was then lifted and placed on top of the ring beam with a rafter.
![]() |
Demag’s 650-tonne crawler crane was rigged up and lifted the ring beam above the silo. |
As per the scope, Al Faris initially lifted the 40-m-long conveyor, weighing 48 tonnes, in tandem with 450-tonne and 250-tonne cranes and erected it over the existing column and silo.
Outlining the challenges of the project, the company states that the main crane had to hold the ring beam above the silo for 15 days, during which time the rafters and purlins were installed, increasing the load from 70 tonnes to 135 tonnes.
The rigging arrangement of the penthouse assembly was designed to lift the load with minimal stress on the steel structure. A detailed load analysis was done, and counterweights were added to the structure to ensure the centre of gravity of the load remained at the centre of the structure.
Another challenge was presented by the fact that the site is near a mountain, where the wind speed created a tunnel effect, and the load surface area was also large, requiring Al Faris to calculate the permissible wind speed.
To complete the project, a complex rigging system was created.
Meanwhile, Al Faris’s Saudi operation successfully executed the upending and loading operation of a tank using Liebherr’s 500-tonne mobile crane with super lift and Liebherr 250-tonne mobile crane.
Given the limited space available, the company says its team expertly manoeuvred the cranes to ensure the safe upending and loading of the gas tank onto the multi-axle trailer. The project demanded a crane with a higher capacity as the distance between the crane and the underground lines was significant, and the radius of operation was constrained, Al Faris points out.
Implementing the project required meticulous planning and use of the best-in-class equipment to overcome the challenges posed by space limitations and safety considerations, it adds.