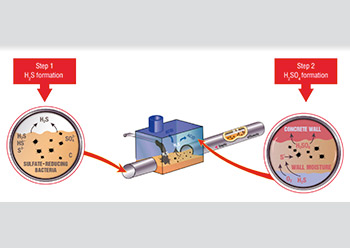
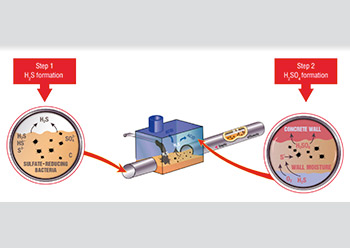
Around the world, deterioration of wastewater collection infrastructure due to hydrogen sulfide (H2S) biogenic corrosion – also known as microorganism-induced corrosion – is a serious headache for owners and operators.
Wastewater collection infrastructure such as gravity pipes, manholes, tanks, lift stations, control structures, and force mains are typically constructed with Portland cement concrete. Portland cement is a calcium silicate and its hydration inescapably liberates calcium hydroxide Ca(OH)2.
![]() |
Severe H2S biogenic corrosion seen in a Portland cement manhole. |
Sewer bacteria excrete sulfuric acid (H2SO4) which reacts with the liberated calcium hydroxide according to the following reaction:
Ca(OH)2 + H2SO4 —> CaSO4 + 2H2O
This reaction produces gypsum and water. In a humid sewer environment, gypsum is dissolved. This ongoing disruptive phenomenon continually leaves a fresh layer of Portland cement for attack.
The H2S biogenic corrosion mechanism is a well-known phenomenon but the specifics of the process are sometimes misunderstood. Surprisingly, wastewater itself is rarely corrosive. The corrosion begins with H2S created by anaerobic bacteria using oxygen from sulfates (SO4) within the wastewater. This H2S builds in concentration in the areas of laminar flow and is then released into the sewerage network in areas of turbulent flow (outfall and force main type situations). Turbulent flow can occur in numerous areas of the system, including piping systems, manholes, pumping situations, treatment plants, etc. This turbulent flow causes the dissolved H2S to become an airborne H2S gas, which is heavier than air and initially exists above the effluent level, dissolving in the moisture on the concrete surfaces above the flow level.
![]() |
A Portland cement manhole rehabilitated with SewperCoat. |
As water is formed by the oxidation of the hydrogen, the H2S gas deposits elemental sulfur onto these surfaces, which is a food source for naturally-occurring bacteria present in the sewerage system. These bacteria, present generally in the slime layer, actually “eat” the elemental sulfur in the presence of oxygen from air. The by-product of the bacteria’s digestion process is sulfuric acid. It is this sulfuric acid that is corrosive to wastewater structures, not the H2S gas itself.
Factors that can enhance this biogenic corrosion cycle include long retention times, high ambient temperatures, flat terrain, and low flow values. With the current growth of outlying suburban areas, feeding into the existing infrastructure of larger metropolitan areas, these factors are becoming increasingly prevalent throughout the world as treatment plants are commonly several miles from the city centre, requiring very long distances to transport the effluent.
Contrary to the chemistry of Portland cement, the hydration process of calcium aluminate cement does not produce calcium hydroxide but liberates calcium aluminate hydrates and Al2O3.3H2O “gibbsite”. The gibbsite liberated from calcium aluminate cement hydration is not susceptible to H2S attack. At pH levels above 3.5, the gibbsite is insoluble, protecting it from the ingress of acid. Below a pH of 3.5, the gibbsite contributes to neutralising the acid at the surface by the consumption of hydrogen ions:
2[Al2(OH)3]3- + 6H+ —> 2Al3+ + 6H2O
![]() |
SewperCoat being applied at the Dubai Sports City sewage treatment plant in January 2016, when one of its four fine grit chambers was emptied for four hours. |
The measure of an acidic pH indicates the level of the molecular concentration of hydrogen ions (H+). Therefore, the more H+ ions there are in solution, the lower the measured surface pH will be. In the equation above, 6 H+ ions are removed from solution making them neutral. This is the “neutralisation capacity” of a calcium aluminate. This neutralisation reaction releases alumina ions (Al3+), which have an inhibitory effect on the metabolism of the bacteria creating the acid. By removing hydrogen ions from solution, the surface pH is locally raised. The released alumina ions react with the bacteria present to slow their activity. Calcium aluminates act as a protective-reactive barrier, greatly reducing the corrosion of the concrete.
The more gibbsite available, the more corrosion-resistant a calcium aluminate-based product will be. A typical calcium aluminate mortar contains 20 to 35 per cent calcium aluminate cement, with the remaining 65 to 80 per cent being a natural aggregate system such as silica sand, limestone, granite, etc. While a calcium aluminate/natural aggregate material will perform better than a Portland cement-based material, only the 20 to 30 per cent cement portion will have the ability to neutralise acid and inhibit bacterial activity.
![]() |
View of the SewperCoat rehabilitation on walls and beams at Dubai Sports City sewage treatment plant when inspected one month |
SewperCoat by Imerys is a 100 per cent calcium aluminate mortar (both cement and aggregate system), and 100 per cent of the product has the ability to neutralise acid and inhibit bacterial activity.
SewperCoat is a cured-in-place, spray-applied cementitious liner that delivers a unique, proven, and radically different trenchless repair strategy: trenchless repair with an easy-to-apply cementitious system able to resist the most severe biogenic corrosion conditions. It bonds well to moist surfaces, and provides rock solid structural rehabilitation within a few hours.
Calcium aluminate cement has been used to protect sewer structures since the 1950s when it was applied in Perth, Australia. South African precasters have been lining precast pipes with calcium aluminate cement since the 1960s. Since the late 1970s, ductile iron pipes (DIP) for wastewater have been lined with calcium aluminate concrete which became the EN standard.
The SewperCoat brand was born in 1991 and it was applied for the first time to rehabilitate a manhole at the Hampton Roads Sanitation Department in Virginia, US. In the Middle East, calcium aluminate cement was selected by Moalajah FZC in 2016 to rehabilitate walls and beams of the Dubai Sports City (DSC) sewage treatment plant.
![]() |
View of the SewperCoat rehabilitation on walls and beams at Dubai Sports City sewage treatment plant when inspected 5.5 years after installation. |
At Dubai Sports City, wastewater arrives in tanker trucks and high quantities of H2S gas are released into the grit chambers of the plant. This high level of H2S gas, combined with the warm climate of Dubai, creates very severe H2S-induced biogenic corrosion. The inert liner protecting the Portland cement tanks had failed after only a few years, allowing corrosion of the Portland cement underneath. The challenge for Moalajah was to rehabilitate the corroding grit chambers without interrupting the sewage treatment plant process. With only a four-hour access time to rehabilitate the grit chambers, almost all usual rehabilitation methods were ruled out because they typically require prior drying of the substrate before applying a polymer lining like epoxy. SewperCoat requires the substrate to be water saturated in order to develop a good bonding. After conducting due diligence with a series of manhole rehabilitation projects in Ajman, Moalajah selected SewperCoat to rehabilitate the grit chambers of the Dubai Sport City sewage treatment plant. In total, around 22 sq m were repaired. A recent inspection showed that SewperCoat is intact, with a sound surface, continuing to protect the structure.
Building upon its 100 years of experience in manufacturing calcium aluminate cement, and the 30-year proven solution SewperCoat targeting the rehabilitation of existing wastewater infrastructure assets, Imerys is launching an innovative new product this year. New wastewater infrastructure assets made from Portland cement or new precast elements that will be exposed to H2S corrosion in their lifetime are typically sprayed with a polymer liner as a form of protection, but the lack of durability means they often fail after only a few years. To tackle this issue, Imerys is introducing Sewper Liner, a mineral solution formulated to achieve long-lasting protection against H2S biogenic corrosion of new wastewater infrastructure assets.