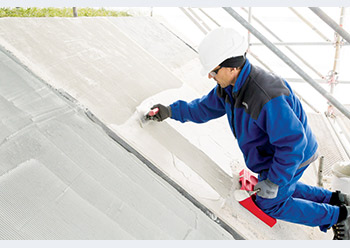
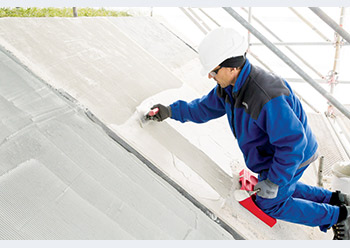
There is no doubt that managing our water infrastructure is one of the biggest challenges facing the water sector. Local communities across the Middle East are facing challenges, as their water infrastructure often comprises aging systems in need of significant upgrade and repair.
Water in liquid or vapour form is the most destructive weathering element as regards building materials such as concrete, masonry, and natural stone. Hence, proper waterproofing is the first line of defence against gradual structural weakening caused by water seeping into a house from above and below.
Traditional sealing and waterproofing systems include bituminous materials, plastic waterproofing films, and metal tapes for interior and exterior applications. Different types of materials can be used to seal and protect the surface of buildings or their structural components against the intrusion of dampness and water. Nowadays, products for this purpose are based on reactive resins like epoxy and/or polyurethane, dispersions (paintable waterproofing membranes) and mineral binders like cement, which are known as waterproofing membranes or sealing slurries.
Cementitious membranes (slurries) are used to waterproof wet rooms and water tanks, and, due to their excellent weathering resistance, for exterior surface protection as well. Further typical applications are the sealing and waterproofing of basement walls and swimming pools, as well as walls and floors in bathrooms, and on balconies and terraces as a waterproofing layer to be tiled over.
Some of the main advantages of cement-based waterproofing membranes are their excellent resistance to water (even if exposed permanently) and long-term weathering resistance, good scratch resistance and load-bearing capacity, and much higher water-vapour permeability than most of the other systems.
Pure (unmodified) cement-based mortars are still used to afford protection against surface water, but they are not suited to sealing against water under hydrostatic pressure. In order to improve the poor adhesion, poor watertightness, and extremely low deformability or flexibility of these pure cementitious mortars, polymers are added in the form of liquid dispersions on site or in the form of a dispersible polymer powder already mixed into the dry-mix mortar. The use of special additives in dry-mix mortars – such as water-retention agents, thickening agents and rheological additives in combination with Vinnapas dispersible polymer powder from Wacker of Germany – creates excellent workability and ensures that there is no need to subject the applied slurry to subsequent water-treatment.
CEMENT WATERPROOFING
![]() |
|
There are various cementitious waterproofing membrane systems available, which can be summarised based on the following classification (Their typical composition is presented in Table 1):
• Standard or rigid mineral waterproofing mortars: These are polymer-modified, pre-packed dry-mix mortars that are mixed with water before being applied as a slurry by brush, roller or airless spraying, as well as by trowel if less gauging water is used. These mortars can only be used for mineral substrates which are stable and solid, and if there is no risk of crack formation, movement or dimensional change (for example, shrinkage).
Watertightness depends on the cement content, the fillers’ shape and particle-size distribution, the type of chemical additives used and the amount of polymer in the form of Vinnapas dispersible powder. Dispersible powders are used as polymer binders in order to improve the adhesion of the slurry on different substrates, its cohesion, flexibility, abrasion resistance and toughness and the watertightness and density of the mortar. Such polymer-modified cementitious waterproofing mortars can withstand water pressure not only from the positive side, but to a limited extent – due to their excellent adhesion and cohesion – from the negative side, too, if this is necessary in specific applications.
• Flexible cementitious waterproofing membranes (two-component systems): These membranes are capable, to a limited extent, of bridging small cracks (up to 1 mm) in the substrate. The flexibility of such products depends considerably on the polymer/cement ratio and, to a lesser extent, on the flexibility of the polymer itself.
Two-component flexible cementitious waterproofing membranes can be supplied in two different types: As a two-pack system composed of a pre-packed dry-mix mortar based on cement, fillers and other additives plus a liquid dispersion in the second pack, which are later mixed on site; and as a system based on a wet premix, with an aqueous dispersion, fillers and additives which is blended on site with Portland cement, resulting in a flexible waterproofing slurry that will be determined by the exact dosage and quality of the cement.
• One-component flexible cementitious membranes: The disadvantage of two-component systems is the risk of mixing errors due to the construction workers’ lack of knowledge, experience and training concerning the appropriate dosage of the liquid component. This means that the resulting membrane may lose its waterproofing capability if exposed to hydrostatic pressure or will at least reduce flexibility, thereby causing system failure. Apart from difficult and risky handling, other reasons for not using two-pack systems include the expense and logistical difficulties, not to mention the higher cost of labour on site whenever two-pack systems are being handled.
Because of the many disadvantages associated with modifying mortars with liquid dispersions, more and more one-component flexible cementitious membranes in the form of a premixed dry-mix mortar are in use today. Wacker has developed specialty Vinnapas dispersible powders with low glass-transition temperatures and high water resistance in order to be able to formulate one-component flexible cementitious waterproofing membranes.
The fact that the dispersible powder requires a high dosage makes the product more expensive. But this is compensated by the advantages of having a one-component, premixed, polymer-modified dry-mix mortar. These benefits include low-cost logistics and packaging, application consistency, and reliability as a result of eliminating on-site mixing errors and achieving higher on-site productivity.
STANDARD FOR SLURRIES
The most applicable standard currently used to test and evaluate waterproofing membranes is EN 14819. This standard mainly focuses on applied waterproofing membranes for use beneath ceramic tiling. The two main tests that are normally carried out to evaluate waterproofing are hydrostatic pressure and crack-bridging tests.
ROLE OF POLYMERS
When the morphology of such polymer-modified waterproofing is investigated by a scanning electron microscope (SEM), large continuous areas of polymer film can be noted, irrespective of whether the mortar is applied by hand or using machinery.
The polymer films are concentrated along the capillary cavities and voids in the mortar. Such images make it evident that the dispersible polymer powder does indeed act as a binder for the cement and aggregate particles and that the polymer film will also bridge over voids and cracks. Since the polymer films coat the walls of the pores and cavities in the mortar like a sort of a covering membrane, it follows that capillary absorbency and penetration by liquids and gases will be reduced, since it is via these pores that they are transported.
SUMMARY
Thanks to its many advantages, Vinnapas polymer powder plays an effective role as regards waterproofing membranes. It exhibits very good adhesion on organic substrates and good cohesion even under permanent water impact. Its high degree of flexibility produces crack-bridging properties (which makes flexible systems possible). It is also characterised by good vapour permeability, low water uptake and considerable resistance to weathering (surface protection), abrasion and scratches. What is more, it exhibits good sealing properties against water under high hydrostatic pressure.