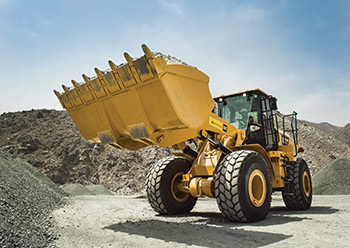
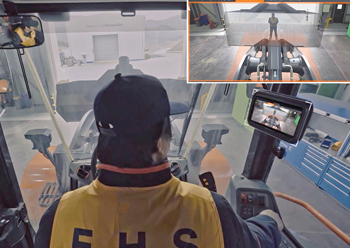
Leading construction equipment maker Doosan Infracore has launched what it claims to be the industry’s first wheel loader ‘transparent bucket’ system.
The transparent bucket is a system that allows the wheel loader driver to see blind spots in front of the bucket on the machine, using the monitor in the cab. The innovative system records images in front of the wheel loader with top and bottom front-loaded cameras and shows combined images on the cab monitor in real time using a curved projection method.
“Owing to blind spots caused by the buckets on wheel loaders, the area in front of the machines has been considered one of major concern in terms of safety,” says a spokesman for Doosan Infracore. “With the new Doosan transparent bucket function, however, the driver can easily check the blind spots in front of the bucket via the cab monitor, to increase safety and prevent accidents.”
“Another advantage of the transparent bucket system is that it can significantly improve work efficiency by providing a forward-view perspective for the driver during loading/unloading or when carrying materials such as aggregates, sand and soil,” he adds.
Doosan Infracore says it is the first company in the world to develop and apply a front projection function with the transparent bucket for construction machines and has applied for patents in Korea, North America, Europe and China.
It has also developed further sophisticated cutting-edge safety systems for the company’s machinery range, such as the around view monitor (AVM) system, which can observe the machines’ surroundings, and a rear warning system using ultrasonic sensors – which have both received very favourable responses from customers, according to the spokesman.
“As machinery and site safety standards continue to be significantly raised around the world, advanced safety systems have become a key factor in selecting equipment. We plan to continue developing safety features that can protect drivers and other workers on site, and we aim to be at the forefront in creating construction sites that are safer and accident-free,” he comments.
Meanwhile, Doosan Infracore was set to introduce its quarrying, mining and construction solution, XiteCloud at the Hillhead Digital event in the UK, which was held online at the end of last month (March 30 to 31). In addition, the company was rolling out its new wheel loader, excavator and articulated dumptruck (ADT) at the event.
XiteCloud is the first step towards the commercialisation of Concept-X, the company’s integrated unmanned and automated control solution, first demonstrated to the world in 2019. It is said to maximise productivity by incorporating complex 3D drone construction surveys and earthwork calculations into a cloud platform, allowing them to be completed in just one to two days.
With XiteCloud, a customer can manage multiple tasks such as surveys, terrain analysis, machine purchases, equipment operation and construction management on a single platform, thereby reducing construction costs and saving time while increasing work accuracy, which in turn raises productivity.
XiteCloud also allows customers to manage multiple projects on a single platform, accumulating and managing data that can be utilised for future decision-making/business.
The solution even makes it possible to digitise earthwork site information into three dimensions as well as to analyze rock formations. Since it is cloud-based, XiteCloud makes it easy for stakeholders, including contractors and clients, to join forces and manage the progress of a given project together, the spokesman says.